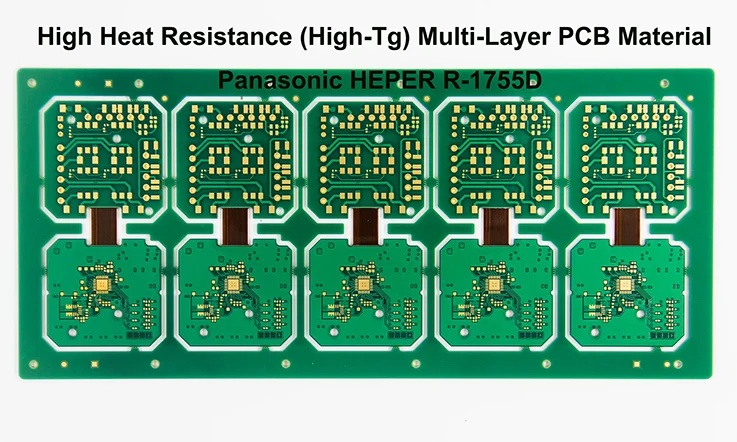
When it comes to selecting a suitable material for your PCB requirements, it is vital to consider both reliability and performance. These attributes are key components found within the properties of the Panasonic HEPER R-1755D material.
For those seeking comprehensive information about the Panasonic HEPER R-1755D, you have come to the right place. In this article, we aim to provide a detailed overview of this material, including its definition, properties, and primary features.
We invite you to continue reading as we expand your knowledge on this subject matter.
Definition of Panasonic HEPER R-1755D
The Panasonic HEPER R-1755D is indeed a high reliability multilayer glass epoxy material that offers several desirable properties for PCB (Printed Circuit Board) applications. One of its notable features is its low coefficient of thermal expansion, which means that it exhibits minimal dimensional changes when exposed to temperature variations. This property is crucial for PCBs as it helps to ensure the stability and integrity of the circuitry, especially in environments with fluctuating temperatures.
Another important characteristic of the HEPER R-1755D is its high glass transition temperature. The glass transition temperature (Tg) refers to the temperature at which the material transitions from a rigid, glassy state to a more flexible, rubbery state. A high Tg is desirable for PCBs because it indicates that the material can withstand elevated temperatures without losing its mechanical strength or electrical properties. This is particularly important in automotive applications where components may be exposed to high temperatures generated by the engine or other heat sources.
The HEPER R-1755D is available in the form of a laminate, which is the main structural layer of the PCB, and the prepreg, which is a partially cured resin used to bond multiple layers of laminate together. The laminate provides the base material for the PCB, while the prepreg acts as the adhesive layer between the laminate and the copper foils or other conductive layers. The use of the R-1650D prepreg in conjunction with the R-1755D laminate ensures compatibility and optimal performance of the overall PCB structure.
Due to its high reliability and heat resistance, the Panasonic HEPER R-1755D material finds extensive use in automotive components. Automotive electronics often operate in demanding environments with temperature variations, vibrations, and other challenging conditions. Therefore, using a material with excellent thermal stability and reliability is crucial to ensure the longevity and performance of the electronic systems in vehicles.
Therefore, the Panasonic HEPER R-1755D is a multilayer glass epoxy material with a low coefficient of thermal expansion and a high glass transition temperature. These properties make it highly desirable for PCB applications, particularly in the automotive industry, where reliability and heat resistance are paramount.
What is Main Features of the Panasonic HEPER R-1755D?
The main features of the Panasonic HEPER R-1755D material are:
1. High heat resistance: It can withstand temperatures up to 163 degrees Celsius, making it suitable for applications that require heat resistance.
2. Excellent through-hole reliability: It maintains its performance and functionality even in harsh environments or under extreme conditions.
3. Overall reliability: It delivers consistent and effective performance over time.
4. Great laminate processability: It is easy to process and work with during the lamination process, enabling efficient production and manufacturing.
5.Compatibility with lead-free soldering: It can be used with lead-free soldering, making it suitable for industries and products that require lead-free materials.
Properties of the Panasonic HEPER R-1755D
The properties of the Panasonic HEPER R-1755D material are:
1. Glass Transition Temperature: The material has a glass transition temperature of 163 degrees Celsius, indicating the temperature at which it turns amorphous during lamination.
2. Thermal Decomposition: The material undergoes thermal decomposition at 345 degrees Celsius, losing about 5% of its mass weight. Heat is required to break the chemical bonds.
3. Coefficient of Thermal Expansion: The material has a CTE value of 10-12 ppm/℃ and 12-14 ppm/℃ at the X and Y axes respectively. It has a CTE value of 43 ppm/℃ at the Z-axis. The CTE indicates the expansion of the material when heated.
4. Dielectric Constant: The material has a dielectric constant of 4.4 at 1 GHz, measuring its ability to store electrical energy in an electric field.
5. Dissipation Factor: The material has a low dissipation factor of 0.016 at 1 GHz, indicating its efficiency as an insulator.
6. Water Absorption: The material has a water absorption rate of 0.11%, preventing moisture from entering and causing device failure.
7. Peel Strength: The material has a peel strength of 1.3 kN/m, indicating its bond strength.
8. Delamination Time: The material has a delamination time of 15 minutes, indicating the time it takes for copper and resin or reinforcement and resin to separate.
9. Flexural Modulus: The material has a flexural modulus of 23 GPa for warp and 21 GPa for fill, denoting its ability to bend or undergo flexural deformation.
10.Flammability: The material has a flammability rating of 94 V-0, indicating that it stops burning within ten seconds.
Key Considerations for Selecting Panasonic HEPER R-1755D Material
When considering the Panasonic HEPER R-1755D material for your application, there are several factors you should take into account:
1.Thermal Expansion:
The low coefficient of thermal expansion of the HEPER R-1755D material ensures minimal dimensional changes with temperature fluctuations. Consider the temperature range your application will be exposed to and ensure that the material’s thermal expansion properties align with your requirements.
2.Glass Transition Temperature (Tg):
The high glass transition temperature of the HEPER R-1755D material indicates its ability to withstand elevated temperatures without compromising its mechanical and electrical properties. Evaluate the operating temperature range of your application and ensure that the material’s Tg exceeds the maximum temperature it will encounter.
3.Reliability:
The HEPER R-1755D material is known for its high reliability, which is crucial for applications that require long-term performance and durability. Consider the specific reliability requirements of your application, such as expected lifespan, environmental conditions, and any industry standards or certifications that need to be met.
4.Heat Resistance:
Automotive components, in particular, often face high temperatures generated by the engine or other heat sources. Assess the heat resistance capabilities of the HEPER R-1755D material and ensure that it can withstand the anticipated temperature levels without significant degradation or loss of performance.
5.Electrical Properties:
PCB materials should possess good electrical properties to ensure signal integrity and minimize losses. Evaluate the dielectric constant, dissipation factor, and electrical insulation properties of the HEPER R-1755D material to ensure they meet your application’s electrical requirements.
6.Compatibility:
Consider the compatibility of the HEPER R-1755D material with other materials and processes involved in your PCB fabrication. Ensure that it can be effectively bonded with copper foils or other conductive layers using suitable prepreg materials such as the R-1650D.
7.Cost:
Evaluate the cost-effectiveness of the HEPER R-1755D material for your specific application. Consider factors such as material availability, manufacturing processes, and any additional requirements or treatments that may affect the overall cost.
By considering these factors, you can determine whether the Panasonic HEPER R-1755D material is suitable for your application and ensure that it meets your performance, reliability, and cost requirements.
Applications of Panasonic HEPER R-1755D PCB Materials
The Panasonic HEPER R-1755D PCB material offers various applications due to its unique properties. Some notable applications include:
1. Printed Circuit Boards (PCBs): The material is primarily used in the manufacturing of PCBs. Its excellent thermal stability and low dissipation factor make it suitable for high-frequency applications, such as telecommunications, aerospace, and automotive industries.
2. High-Speed Signal Transmission: The material’s low dielectric constant and low dissipation factor enable efficient and reliable high-speed signal transmission. It helps to minimize signal loss and maintain signal integrity, making it ideal for high-speed data communication systems.
3. RF and Microwave Applications: The material’s low dielectric constant and low loss tangent make it well-suited for RF (Radio Frequency) and microwave applications. It enables the construction of high-performance antennas, wireless communication devices, and radar systems.
4. Power Electronics: The material’s high glass transition temperature and thermal stability make it suitable for power electronics applications. It can withstand high operating temperatures and provide efficient thermal management, making it ideal for power modules, inverters, and motor drives.
5. Automotive Electronics: The material’s flame-retardant properties (94 V-0 rating) and resistance to moisture absorption make it a reliable choice for automotive electronics. It can withstand high temperatures, vibrations, and harsh environments commonly encountered in automotive applications.
6. Consumer Electronics: The material’s excellent electrical properties and dimensional stability make it well-suited for consumer electronic devices. It can be used in smartphones, tablets, laptops, and other electronic gadgets to ensure reliable signal transmission and performance.
7. Industrial Control Systems: The material’s high peel strength and resistance to delamination make it suitable for industrial control systems. It ensures robust and reliable connections in control boards and PLCs (Programmable Logic Controllers).
8. Medical Electronics: The material’s low water absorption and biocompatibility make it suitable for medical electronics applications. It can be used in medical devices and equipment where reliability and safety are crucial.
Overall, the Panasonic HEPER R-1755D PCB material finds extensive use in various industries, ranging from telecommunications to automotive, due to its exceptional electrical, thermal, and mechanical properties.
Conclusion
Panasonic HEPER R-1755D stands as a reliable and heat-resistant material that meets the stringent requirements of PCB designers. Its low coefficient of thermal expansion ensures stability and integrity even in fluctuating temperature environments, while the high glass transition temperature enables it to withstand elevated temperatures without compromising performance. With its excellent reliability and compatibility with prepreg materials like the R-1650D, the HEPER R-1755D is a go-to choice for automotive components and other applications where durability is paramount. By choosing the Panasonic HEPER R-1755D, PCB designers can achieve optimal performance and longevity for their electronic systems.