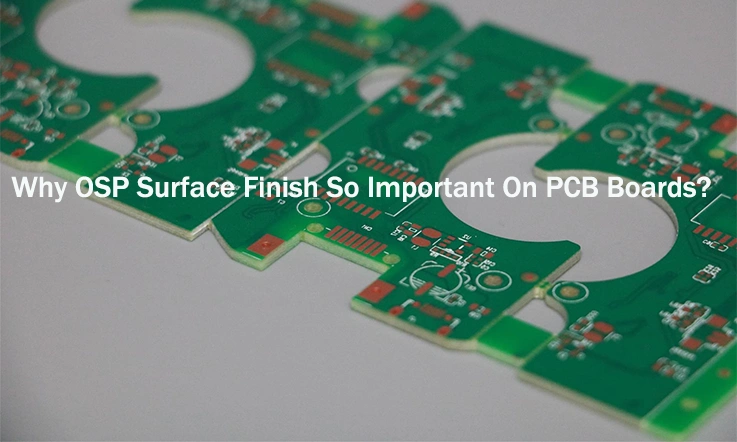
The electrical connectivity on a printed circuit board (PCB) relies heavily on the conductivity of copper. However, copper is a chemically active substance that is prone to oxidation when exposed to atmospheric humidity. This oxidation can cause significant issues, particularly during high-temperature soldering processes. It jeopardizes the secure attachment of components to the PCB and diminishes the overall reliability of the end products. Consequently, the choice of surface finish on a PCB plays a crucial role in addressing these concerns by protecting the copper from oxidation and providing a solderable surface for component assembly.
Surface finishes for PCBs can be categorized based on different technologies and the chemical substances involved. Common classifications include HASL (hot air solder leveling), Immersion Tin/Silver, OSP, ENIG, and ENEPIG. Among these finishes, OSP has gained popularity due to its cost-effectiveness and environmentally friendly characteristics. This article aims to provide a comprehensive understanding of OSP, considering its increasing prevalence and the need for better comprehension of this surface finish.
What is Organic Solderability Preservative (OSP)?
Organic Solderability Preservatives (OSP) is a surface finish utilized in the production of printed circuit boards (PCBs). Also known as anti-tarnish, OSP provides a protective layer of organic material on the clean copper surface of the PCB through an adsorption process.
The primary function of OSP is to safeguard the copper from oxidation and the potential detrimental effects of moisture and environmental factors. During the soldering process, the OSP layer can be easily removed through the application of PCB flux. This enables the clean copper to interact with the molten solder, facilitating the formation of solder joints in a more efficient manner.
In the OSP surface treatment, a water-based compound containing azole groups, such as benzimidazoles, imidazoles, and benzotriazoles, is employed. These compounds are absorbed into the copper surface, creating a thin film. It is worth noting that the film thickness generated by benzotriazoles is generally thinner compared to that of imidazoles. Typically, the film thickness ranges from tens to hundreds of nanometers.
Features of OSP PCB Surface Finish
OSP (Organic Solderability Preservatives) is a popular surface finish used in the manufacturing of printed circuit boards (PCBs). It offers several notable features that make it advantageous in various applications. Here are the key features of OSP PCB surface finish:
1. Cost-effective: OSP is known for its cost-effectiveness compared to other surface finishes like ENIG or immersion gold. It is a relatively affordable option, making it suitable for budget-conscious projects.
2. Environmental friendliness: OSP is considered an environmentally friendly surface finish. It does not contain heavy metals like lead or gold, which are present in finishes like HASL or ENIG. This makes OSP a more sustainable choice, aligning with eco-friendly manufacturing practices.
3. Good solderability: OSP provides excellent solderability, allowing for reliable and robust solder joints. The organic compound in OSP forms a thin protective layer on the copper surface, ensuring good wetting and adhesion of solder during the assembly process.
4. Surface planarity: OSP offers good surface planarity, especially for fine-pitch components. The organic layer helps to smoothen the copper surface, reducing the risk of solder bridging or insufficient solder coverage on small pads or traces.
5. Shelf life and reworkability: OSP has a relatively long shelf life compared to some other surface finishes. It maintains its solderability properties for a reasonable duration, allowing for extended storage or handling time. Additionally, OSP is easily reworkable, as the organic layer can be readily removed using PCB flux, enabling efficient repair or reflow processes.
6. Compatibility with multiple assembly processes: OSP is compatible with various assembly processes, including surface mount technology (SMT), through-hole technology (THT), and mixed technology. It can be used for both leaded and lead-free soldering processes, making it versatile for different manufacturing requirements.
7. Thin layer thickness: The OSP layer formed on the copper surface is typically very thin, ranging from tens to hundreds of nanometers. This thin layer minimizes any impact on the overall dimensions of the PCB and allows for precise control over the soldering process.
It’s important to note that OSP does have some limitations. It is sensitive to handling and requires proper storage conditions to maintain its performance. OSP may also have lower shelf life compared to more robust finishes like ENIG. Nevertheless, with proper handling and suitable application, OSP can provide reliable solderability and cost-effective surface finish for many PCB applications.
When to Use OSP as Your PCB’s Surface Finish
OSP, or Organic Solderability Preservative, is a surface finish that finds application in both simple and complex printed circuit boards (PCBs). It is particularly suitable for high-density IC load boards. Below, I will discuss the appropriate cases for using OSP as the PCB surface finish.
Fine-pitch rigid PCB: In cases where the pitch of the rigid PCB is within 0.5mm, the use of HASL, including lead-free HASL, as the PCB surface finish is not viable. Instead, OSP or ENIG can be employed.
Flexible PCB: In the realm of flexible PCBs (FPCs), OSP is used less frequently than ENIG. However, for applications such as flexible LED strips that demand cost-effective fabrication, OSP is a suitable choice. In complex and high-performance FPCs, a combination of selective surface finishes, namely OSP and ENIG, can be employed.
Batch production for consumer electronics: OSP, owing to its cost-effectiveness and good solderability when boards are soldered immediately, is an ideal choice for batch production in the consumer electronics sector. By utilizing OSP, fabrication costs can be reduced while ensuring a desirable outcome. Our experience suggests that OSP is commonly employed for batch fabrication of PCBs for consumer electronics.
Flexible aluminum PCB: Flexible aluminum PCBs are unconventional bendable aluminum substrate PCBs primarily used in LED lamps. With a power rating of 1W, OSP is the recommended surface finish for this specific application.
Low-cost PCB fabrication: If the objective is to minimize the fabrication cost of a project, OSP is an advantageous choice as the PCB surface finish. Additionally, OSP can be utilized on high-frequency PCBs.
However, it is important to note that OSP is not suitable for keyboard PCBs, plug-ins (such as gold fingers), wire-bonding pads, PCBs requiring multiple reflow cycles, and PCB pads that necessitate the exposure of the conductive area. In such scenarios, alternative surface finishes should be considered. It is worth mentioning that selective ENIG can serve as a viable surface finish for all types of PCBs.
Overall, OSP is a versatile surface finish option that can be employed in various PCB applications. Its cost-effectiveness and desirable solderability make it a favorable choice for batch production and low-cost fabrication. However, it is essential to consider the specific requirements of each application to determine the most suitable surface finish.
Comparison of OSP with Other Surface Finishes
When comparing OSP (Organic Solderability Preservatives) with other surface finishes, several factors should be considered, including cost, reliability, ease of application, environmental impact, and compatibility with different assembly processes. Here’s a comparison of OSP with some common surface finishes:
1.HASL (Hot Air Solder Leveling):
●Cost: HASL is generally less expensive than OSP.
●Reliability: OSP offers better planarity and solder joint quality, especially for fine-pitch components.
●Application: HASL requires a high-temperature process, which may not be suitable for heat-sensitive components.
●Environmental Impact: OSP is considered more environmentally friendly as it uses organic compounds instead of lead-based alloys.
●Assembly Compatibility: OSP is compatible with most assembly processes, while HASL may have limitations with certain components or processes.
2. ENIG (Electroless Nickel Immersion Gold):
●Cost: ENIG is typically more expensive than OSP.
●Reliability: ENIG provides excellent corrosion resistance and solderability, making it highly reliable.
●Application: ENIG is suitable for various component sizes and offers good planarity.
●Environmental Impact: ENIG requires the use of chemicals, including gold, which can have environmental implications.
●Assembly Compatibility: ENIG is compatible with most assembly processes.
3. Immersion Silver:
●Cost: Immersion silver is generally more expensive than OSP.
●Reliability: Immersion silver offers good solderability and is suitable for various component sizes.
●Application: Immersion silver can be prone to tarnishing and may require additional protective measures.
●Environmental Impact: Immersion silver involves the use of chemicals, including silver, which can have environmental implications.
●Assembly Compatibility: Immersion silver is compatible with most assembly processes.
4. OSP (Organic Solderability Preservatives):
●Cost: OSP is generally cost-effective compared to other surface finishes.
●Reliability: OSP provides good solderability and planarity, especially for fine-pitch components.
●Application: OSP is relatively easy to apply, requiring fewer process steps and lower temperatures.
●Environmental Impact: OSP is considered environmentally friendly as it does not contain heavy metals.
●Assembly Compatibility: OSP is compatible with most assembly processes.
It’s important to note that the suitability of a surface finish depends on the specific application, component requirements, and manufacturing process. Manufacturers should consider these factors and consult with their PCB supplier or surface finish provider to determine the most appropriate choice for their needs.
How OSP Surface Finish on PCB Work?
The initial stage in the manufacturing process of OSP PCBs involves a critical step known as cleaning. This step is essential for eliminating various contaminants such as oxidation, fingerprints, and residual oils from the copper surface. Thorough cleaning ensures uniformity of the copper surface, allowing for consistent film formation throughout.
Following the cleaning process, a preliminary surface modification is performed to facilitate the subsequent deposition of the OSP film. This modification helps remove any remaining oxidation from the copper surface, preventing any hindrance in the attachment of the OSP solution to the copper.
The subsequent step in the manufacturing process is deionization washing. This step plays a vital role in eliminating any additional ions that may have inadvertently contaminated the copper surface. Deionization washing ensures the removal of unwanted impurities, contributing to the overall cleanliness of the copper surface.
The final step in this process involves the formation of the OSP film. This step includes a repeat of the deionization rinse to eliminate any potential contamination from ions. The preservative build used in this step typically exhibits a pH value within the range of 0.4 to 7.0.
By following these sequential steps during the manufacturing process of OSP PCBs, manufacturers can achieve a clean and well-prepared copper surface, facilitating the successful formation of the OSP film.
OSP Problems after Soldering
After soldering, there are a few potential problems that can arise with OSP (Organic Solderability Preservatives) coatings on PCBs. Here are some common OSP problems that can occur after soldering:
1. Insufficient Wetting: One common issue is insufficient wetting of the solder onto the OSP-coated surface. This can result in incomplete solder joints or poor solder flow, leading to weak connections or solder bridges. Insufficient wetting can occur if the OSP coating is not properly activated or if the soldering temperature or time is inadequate.
2. OSP Degradation: Over time, the OSP coating can degrade, especially if the PCBs are exposed to harsh environmental conditions or extended storage periods. Degradation of the OSP coating may lead to reduced solderability, resulting in poor solder joints, increased solder defects, or difficulty in reworking or repairing the PCBs.
3. Contamination: Contamination of the OSP-coated surface can occur during handling, assembly, or storage. Contaminants such as oils, fingerprints, flux residues, or other foreign substances can interfere with the OSP coating and prevent proper solder wetting. This can result in soldering defects, including poor adhesion, solder voids, or unreliable solder joints.
4. Inadequate OSP Thickness: If the OSP coating is applied with an inadequate thickness, it may not provide sufficient protection to the underlying copper surface during the soldering process. This can lead to oxidation or tarnishing of the copper, affecting the solderability and resulting in poor-quality solder joints.
5. Incompatibility with Lead-Free Soldering: Some OSP formulations may not be fully compatible with lead-free soldering processes, which typically require higher soldering temperatures. In such cases, the OSP coating may not withstand the higher temperatures, resulting in degradation, poor soldering performance, or reduced reliability of the solder joints.
To address these OSP problems after soldering, it is important to:
●Ensure proper activation of the OSP coating before soldering, following the manufacturer’s recommendations.
●Implement appropriate storage and handling practices to prevent contamination and degradation of the OSP coating.
●Regularly monitor and evaluate the solderability and performance of OSP-coated PCBs through inspection and testing.
●Consider alternative surface finishes, such as ENIG (Electroless Nickel Immersion Gold) or HASL (Hot Air Solder Leveling), if persistent OSP issues are encountered.
Consulting with PCB manufacturers, surface finish suppliers, or industry experts can provide further guidance on addressing specific OSP problems and optimizing the soldering performance of OSP-coated PCBs.
Key Considerations for Selecting PCB OSP Surface Finishes
When selecting an OSP (Organic Solderability Preservatives) finish for your PCB, there are several crucial aspects to consider. These factors will help ensure the appropriate choice based on the PCB design, finishing process, and desired end result. Here are some key considerations:
1. Solderability: Solderability is of utmost importance to prevent any soldering issues that may arise and to ensure the effective functioning of the OSP PCB. Evaluate whether the OSP finish can solder effectively to copper, as copper is a common material for OSP finishes, making it a suitable choice in such cases.
2. Processing Duration: Take into account the processing duration required for the OSP finish. Different finishes have varying processing times, with finishes like HASL (Hot Air Solder Leveling) typically having longer processing durations. Consider this aspect when selecting an OSP surface finish to ensure it aligns with your manufacturing timeline and requirements.
3. Reliability: Consider the reliability factor associated with the chosen OSP finish. Assess how well the OSP finish will withstand the intended operating conditions and environment. It is essential to choose an OSP finish that can provide the necessary reliability and durability for the specific application.
4. Corrosion Resistance: Evaluate the vulnerability of the OSP finish to corrosion, especially in relation to the materials involved. Some surface finishes, such as silver, are more prone to oxidation and corrosion compared to others. Take this into consideration to ensure the OSP surface finish offers adequate protection against corrosion, considering the expected operating environment.
By carefully considering these aspects, you can make an informed decision when selecting an OSP surface finish for your PCB. It is crucial to prioritize solderability, processing duration, reliability, and corrosion resistance to ensure the chosen OSP finish meets the requirements of your specific application. If you require further assistance or have additional inquiries, feel free to ask.
Storage Requirements for OSP Coating PCB
Proper storage of OSP (Organic Solderability Preservatives) coated PCBs is essential to maintain the effectiveness of the OSP coating over time. Here are the recommended storage requirements for OSP coated PCBs:
1. Temperature: Store OSP coated PCBs in a controlled environment with a stable temperature. The ideal temperature range for storage is typically between 10°C and 30°C (50°F and 86°F). Avoid exposing the PCBs to extreme temperatures, as high temperatures can accelerate the degradation of the OSP coating.
2. Humidity: Control the humidity levels in the storage area. The recommended relative humidity range is between 40% and 60%. Excessive moisture can negatively impact the OSP coating, leading to reduced solderability and potential corrosion issues.
3. Moisture Protection: Protect OSP coated PCBs from direct exposure to moisture during storage. Store the PCBs in sealed moisture-barrier bags or containers to prevent moisture absorption. Use desiccants or humidity control devices within the storage containers to maintain low humidity levels.
4. Light Exposure: Minimize exposure to direct sunlight or ultraviolet (UV) light. Prolonged exposure to UV light can degrade the OSP coating and affect its solderability. Store OSP coated PCBs in a dark or low-light environment to preserve the integrity of the coating.
5. Avoid Contaminants: Keep the storage area clean and free from contaminants that could potentially affect the OSP coating. Avoid storing OSP coated PCBs near sources of chemicals, gases, or airborne particles that could contaminate the surface.
6. Handling Precautions: When handling OSP coated PCBs, use proper ESD (Electrostatic Discharge) precautions to prevent electrostatic damage. ESD-safe packaging and handling procedures should be followed to protect the sensitive electronic components and the OSP coating.
7. Shelf Life: Take note of the manufacturer’s recommended shelf life for the OSP coating. OSP coatings typically have a limited shelf life, and it is important to use the coated PCBs within the specified timeframe to ensure optimal solderability and performance.
By adhering to these storage requirements, you can help ensure the longevity and effectiveness of the OSP coating on your PCBs, maintaining their solderability and protecting them from potential degradation or corrosion.
Summary
The Organic Solderability Preservative (OSP) finish is an economical and solderable coating option for PCBs when implemented correctly. It effectively safeguards copper traces against oxidation for extended periods under proper control.
Nevertheless, it is important to acknowledge that OSP does have limitations in terms of shelf life and durability through multiple reflow cycles. Therefore, it is crucial to match OSP with designs that have short shelf life or low assembly complexity.
OSP presents several advantages, including its environmental friendliness, cost-effectiveness, and ease of application. It strikes a favorable balance for many less demanding applications. However, it is essential to be mindful of the tradeoffs compared to more robust surface finishes.
To maximize the benefits of OSP, collaborating with your PCB manufacturer to selectively apply OSP based on specific design requirements is key. This ensures that you derive the utmost advantage from this beneficial surface finish where it is most appropriate.