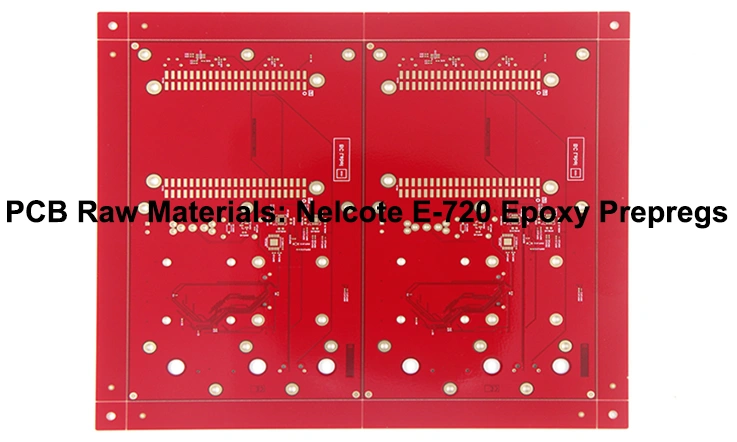
The Nelcote E-720 Epoxy Prepreg, 581 Quartz Reinforced is a two-part epoxy resin material that incorporates fiberglass stiffenings and a hardener. It is primarily utilized in the manufacturing of composite parts for industrial applications, and has also proven to be advantageous in the automotive sector.
This material is commonly employed by aircraft and vehicle manufacturers for the production of their components. Its success has been particularly notable in the aircraft manufacturing industry, exemplified by its utilization in the production of aircraft by companies like JarnisTech PCB & Assembly. Furthermore, it has demonstrated its efficacy in the manufacturing of orthopedic implants, boats, automotive items including clutch facings, and various other products.
The Nelcote E-720 Epoxy Prepreg, 581 Quartz Reinforced offers a combination of fiberglass reinforcement and epoxy resin, resulting in a material that delivers strength, durability, and versatility. Its widespread adoption in diverse industries attests to its reliability and suitability for a range of applications.
What Is Nelcote E-720?
Nelcote® E-720 is a specially formulated epoxy resin system that has been engineered to maintain exceptional mechanical properties even when subjected to prolonged exposure to high temperatures. This unique resin system has a well-established track record in various challenging aerospace applications.
Key Features & Benefits of Nelcote E-720:
Excellent retention of mechanical properties: Nelcote E-720 has been specifically designed to maintain its mechanical properties even after prolonged exposure to high temperatures. This ensures that the material remains structurally sound and reliable in demanding environments.
Long out-time for easy processing: The extended out-time of Nelcote E-720 makes it easier to work with during the manufacturing process. This allows for better control and flexibility in shaping and forming the material as needed.
Good electrical properties: In addition to its mechanical strength, Nelcote E-720 also exhibits good electrical properties. This makes it suitable for applications where reliable electrical performance is required.
These key features and benefits of Nelcote E-720 contribute to its suitability for use in various aerospace applications and secondary aircraft structures, such as radomes, nacelles, inlet ducts, and fairings.
Product Forms of Nelcote E-720:
Available on a wide variety of reinforcements: Nelcote E-720 can be applied to different types of reinforcements, including fiberglass and quartz. This allows for customization and adaptation to specific application requirements.
Solution coated fabrics: Nelcote E-720 can be applied to fabrics through a solution coating process. This enables the production of large and wide sheets of coated fabric, up to 60 inches in width. This facilitates easier handling and processing during manufacturing.
Compatible with Autoclave or Press Molding processes: Nelcote E-720 is compatible with both Autoclave and Press Molding processes. These molding techniques are commonly used in the aerospace industry for manufacturing components with high strength and precision. The compatibility of Nelcote E-720 with these processes ensures that it can be easily incorporated into existing manufacturing workflows.
These product forms of Nelcote E-720 enhance its versatility and suitability for use in various aerospace applications, where different reinforcement types and molding processes may be required.
How handle Processing for Nelcote E-720?
When selecting Nelcote E-720 for your application, there are several considerations to keep in mind:
1. Strength Variation: Nelcote E-720 exhibits bimorphism, meaning that there is more variation in strength along the X direction compared to the Z direction. This property can be advantageous for bending applications, as it provides technicians with more control over the part’s deformation. Consider the specific requirements of your application and determine if this strength variation aligns with your desired performance.
2. Processing Requirements: The processing of Nelcote E-720 involves grinding and milling the raw material, extruding the fibrous component through a die, and curing it in a closed oven. Additionally, the fibers are stretched in a mold and exothermically cured to cure the resin. Ensure that your manufacturing capabilities and equipment can meet these processing requirements.
3. Mechanical Properties: Evaluate the mechanical properties of Nelcote E-720, such as its strength, stiffness, and thermal stability, in relation to the demands of your application. Consider factors such as temperature exposure, load-bearing requirements, and environmental conditions to ensure the material’s suitability.
4. Application Compatibility: Assess whether Nelcote E-720 aligns with the specific needs and constraints of your application. Consider factors such as weight restrictions, chemical resistance, electrical conductivity, and any other relevant considerations to ensure that the material can perform optimally in the intended application.
5. Cost and Availability: Consider the cost and availability of Nelcote E-720 for your project. Evaluate the material’s pricing, availability from suppliers, and any associated costs for processing and fabrication.
By carefully considering these factors, you can determine if Nelcote E-720 is the right choice for your application and ensure that it meets your performance requirements effectively.
Applications/Qualifications of Nelcote E-720
Nelcote® E-720 finds its applications and qualifications in various areas, particularly in the aerospace industry. Its exceptional mechanical property retention and resistance to high temperatures make it suitable for demanding environments. Here are some specific applications and qualifications of Nelcote E-720:
Secondary Aircraft Structures:
Nelcote E-720 is suitable for use in secondary aircraft structures, which are non-primary load-bearing components of an aircraft. These structures often require high temperature resistance and good mechanical properties, both of which Nelcote E-720 offers.
Radomes:
Radomes are protective enclosures that house radar systems on aircraft. Nelcote E-720’s excellent retention of mechanical properties and good electrical properties make it a suitable material for radomes, ensuring the protection and performance of the radar system.
Nacelles:
Nacelles are the housings that surround an aircraft’s engines. Nelcote E-720’s ability to retain mechanical properties after long-term high temperature exposure makes it a reliable material for nacelles, which are exposed to high temperatures generated by the engines.
Inlet Ducts:
Inlet ducts are responsible for channeling airflow into the aircraft’s engines. Nelcote E-720’s good electrical properties and retention of mechanical properties make it a suitable material for inlet ducts, ensuring efficient and reliable airflow to the engines.
Fairings:
Fairings are aerodynamic structures that cover gaps and joints on an aircraft’s surface. Nelcote E-720’s long out-time for easy processing and excellent retention of mechanical properties make it a suitable material for fairings, providing both structural integrity and aerodynamic efficiency.
The applications and qualifications of Nelcote E-720 make it an ideal choice for various aerospace components, ensuring reliability, durability, and performance in demanding environments.
Conclusion
Selecting Nelcote E-720 for your application requires careful consideration. Factors such as the material’s strength variation, processing requirements, mechanical properties, application compatibility, and cost and availability should be taken into account. By assessing these factors, you can determine whether Nelcote E-720 is the right choice for your specific needs. Its exceptional mechanical property retention, high-temperature resistance, and versatility make it a compelling option for demanding applications. Make an informed decision and leverage the benefits of Nelcote E-720 epoxy prepregs to achieve optimal performance in your projects.