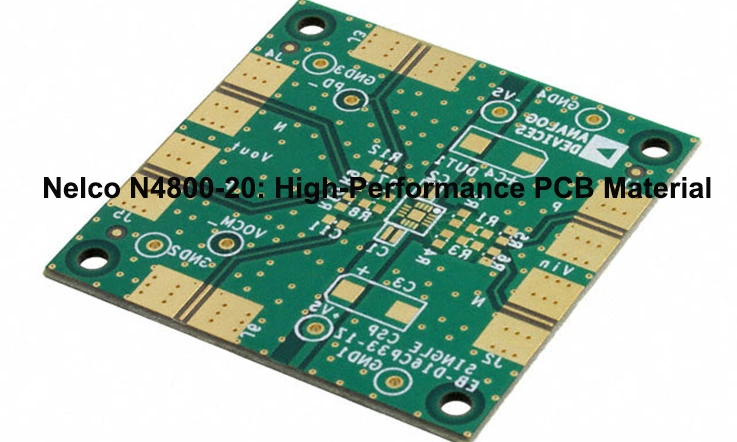
In industries where precision, durability, and electrical stability drive innovation, selecting the right PCB laminate is more than a material choice—it’s a strategic decision. Nelco N4800-20 has gained traction among engineers and manufacturers tackling high-speed signal transmission, thermal management, and miniaturization challenges.
From 5G infrastructure and aerospace systems to medical electronics, this advanced laminate is engineered to meet stringent performance demands while optimizing manufacturing efficiency. By offering low dielectric loss, enhanced CAF resistance, and controlled thermal expansion, it supports reliable circuit performance in even the most demanding applications.
This article dives into real-world applications, processing advantages, and cost-benefit considerations for Nelco N4800-20, helping you determine whether it aligns with your next PCB project.
The Hidden Challenges in High-Performance PCB Design – Why Nelco N4800-20 Solves Them
Designing multilayer PCBs for high-frequency applications comes with a fair share of obstacles. Many design engineers face unexpected failures due to material limitations, leading to unnecessary revisions and production delays.
If you’ve ever faced impedance shifts, thermal expansion strain, or signal loss, you know laminate choice goes beyond cost. Nelco N4800-20 is tailored to handle GHz-speed circuits, extreme thermal conditions, and reliability concerns without the usual setbacks.
This section explores common issues in high-performance PCB designs and how this advanced material provides a stable foundation for demanding applications.
The Growing Complexity of High-Speed PCB Designs & Why Standard Laminates Fall Short
Electronic systems today demand faster data rates, compact layouts, and higher durability. While standard laminates may work fine for lower-speed applications, they tend to struggle as frequency and environmental stress increase.
Common Challenge | What Happens with Standard Laminates? | The Result |
Signal Degradation | Higher dissipation factor (Df) leads to energy loss over traces. | Weak signals, poor transmission in RF and 5G networks. |
Thermal Expansion | Different coefficients of expansion (CTE) create mechanical stress on vias. | Cracked plated-through holes (PTHs), layer separation over time. |
Impedance Variations | Inconsistent dielectric constant (Dk) values affect controlled impedance traces. | Signal distortion, data errors, and performance instability. |
For designers developing 5G infrastructure, aerospace systems, and high-frequency devices, these problems often lead to board failures that could have been prevented at the material selection stage. Let’s explore how Nelco N4800-20 provides an advantage.
How Nelco N4800-20 Handles Signal Integrity, Thermal Expansion & Reliability?
Not all PCB materials are built the same. Nelco N4800-20 is formulated to address challenges that many laminates struggle with.
1. Maintaining Signal Quality Across High-Speed Circuits-
Signal integrity issues often arise when using materials that introduce excessive loss or allow impedance to fluctuate. Nelco N4800-20 minimizes these risks by offering:
●Low dissipation factor (~0.0026 @ 10 GHz) → Allows signals to travel without unwanted loss or distortion.
●Stable dielectric constant (~3.8) → Prevents impedance shifts that could cause data transmission issues.
●Optimized loss tangent → Supports cleaner, more predictable waveforms.
2. Handling Temperature Shifts Without Structural Failures-
When a PCB experiences heat cycling, materials expand and contract. If the laminate doesn’t match the expansion rate of copper, mechanical stress builds up, leading to delamination or cracked vias.
●Low Z-axis CTE (~40 ppm/°C) → Keeps plated vias intact through multiple thermal cycles.
●Tg above 200°C → Endures reflow soldering processes without degradation.
●Balanced resin-to-glass ratio → Reduces stress on interlayer bonding.
3. Stability in Harsh Environments-
PCBs used in radar, medical imaging, and defense applications require materials that stay reliable under extreme conditions. Nelco N4800-20 is chosen for:
●5G base stations & networking → Ensures stable transmission over long distances.
●Aerospace electronics → Resists degradation from radiation and fluctuating temperatures.
●Medical diagnostic equipment → Supports precision RF performance for accurate imaging.
Common Misconceptions About High-Performance PCB Design & How to Avoid Costly Mistakes
Even experienced designers sometimes run into costly misjudgments when selecting PCB materials. Below are some common misconceptions and the reality behind them.
Myth #1: FR-4 Works Just Fine for GHz-Range Designs-
Reality: Once operating frequencies cross into GHz territory, FR-4 starts showing weaknesses—higher insertion loss, fluctuating impedance, and poor thermal management. Nelco N4800-20 delivers lower loss and a more stable electrical profile suited for RF, microwave, and high-speed digital applications.
Myth #2: Thermal Expansion Isn’t a Big Deal-
Reality: PCBs exposed to repeated thermal cycles in industrial control or telecom systems can experience material fatigue, delamination, or via failures if expansion rates are not properly managed. Nelco N4800-20 helps reduce these stresses, enhancing long-term performance.
Myth #3: Advanced Laminates Are Too Expensive-
Reality: While the upfront cost of a premium laminate might be higher, choosing the wrong material often leads to far greater expenses in board re-spins, manufacturing failures, and field replacements. Investing in the right material from the start prevents unnecessary production costs and delays.
Inside the Material Science – What Sets Nelco N4800-20 Apart in PCB Laminate Technology?
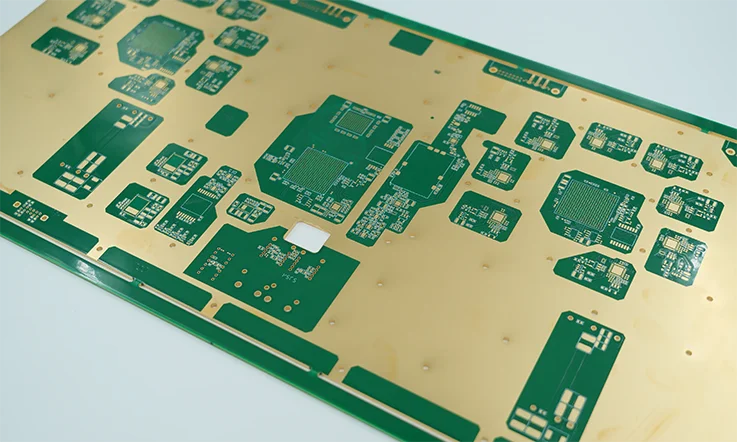
Designing high-frequency and high-speed digital circuits comes with a list of challenges—signal integrity, thermal expansion, and material stability, just to name a few. The choice of PCB laminate directly impacts how well a circuit handles electromagnetic interference, environmental stresses, and long-term use.
Some laminates struggle to maintain consistent electrical properties across a range of operating conditions, which can lead to performance shifts over time. Nelco N4800-20, on the other hand, is built for PCB engineers pushing the limits of high-speed applications.
To understand how this material performs in demanding environments, let’s break down its resin system, dielectric properties, and structural composition.
Breaking Down the Chemistry – Resin System, Fillers & Glass Weave Impact
PCB laminates are not all created equal. Their performance in real-world applications depends on how the resin, fillers, and glass reinforcement interact under stress, heat, and frequency shifts.
Component | Impact on Performance |
Resin System | Influences dielectric stability, thermal expansion, and chemical resistance |
Filler Content | Controls dimensional stability, mechanical durability, and layer bonding strength |
Glass Weave | Affects signal propagation, fiber weave effect, and structural consistency |
How Nelco N4800-20 Stands Out in Material Composition-
Standard FR-4 laminates rely on generic epoxy resins, which tend to shift in performance when exposed to temperature variations or high-speed signals. Nelco N4800-20, however, uses an advanced thermoset resin system, offering predictable behavior across a wide frequency range.
●Glass Transition Temperature (Tg) Over 200°C – Handles multiple thermal cycles without losing structural stability.
●Low Z-Axis Expansion (~40 ppm/°C) – Reduces stress on vias and minimizes risk of delamination.
●Optimized Glass Weave Structure – Limits fiber weave effects that can distort high-speed signals.
By balancing resin content, filler distribution, and glass reinforcement, Nelco N4800-20 ensures steady electrical performance in RF, microwave, and high-speed digital circuits.
How Low Df and Dk Enhance Signal Performance in Nelco N4800-20?
In 5G infrastructure, aerospace, and high-speed computing, signal consistency determines whether a system runs as expected or faces unexpected losses. Lossy laminates introduce distortion, impedance mismatches, and unexpected performance shifts—issues that can be avoided with the right material selection.
Nelco N4800-20 is built with a low dissipation factor (Df) and controlled dielectric constant (Dk), supporting stable signal propagation even at GHz frequencies.
Property | Nelco N4800-20 Value | What It Means for PCB Performance |
Dielectric Constant (Dk) ~3.8 | Remains steady across a wide frequency range | Maintains consistent impedance matching |
Dissipation Factor (Df) ~0.0026 @ 10 GHz | Limits signal loss | Reduces attenuation in high-speed and RF circuits |
Moisture Absorption <0.1% | Resists environmental humidity effects | Keeps electrical properties stable over time |
Why These Electrical Properties Matter in Real-World Use-
For high-speed data transmission, RF designs, and automotive radar systems, a PCB laminate must support predictable performance over time.
●5G & Telecom Applications → Enables high-bandwidth, low-latency signal flow.
●Aerospace & Defense Electronics → Maintains precision in RF and microwave frequencies.
●Medical Equipment & Imaging Systems → Supports accurate signal detection and transmission.
By keeping Df low and Dk stable, we can design circuits that operate at peak efficiency without unnecessary loss or distortion.
Nelco N4800-20 & CAF Resistance – Long-Term Durability in Harsh Conditions
Conductive Anodic Filamentation (CAF) is an issue that can cause unexpected circuit failures over time. It happens when moisture, bias voltage, and ion migration create metallic paths between conductive traces, leading to short circuits and malfunctions.
What Causes CAF & How Nelco N4800-20 Prevents It-
Issue | Contributing Factors | How Nelco N4800-20 Minimizes Risk |
Short Circuits | High humidity & ion contamination | Moisture-resistant resin system & CAF-resistant fillers |
Layer Separation | Poor bonding & excessive thermal expansion | Optimized glass-resin adhesion & low CTE |
Performance Instability | Ionic movement under voltage stress | Low moisture absorption & chemically stable resin composition |
Why CAF Resistance Makes a Difference-
For industries where PCB durability directly affects reliability, using a CAF-resistant laminate means less risk of failure in the field.
●Aerospace & Satellites → Resists failure in high-altitude, moisture-prone environments.
●Telecom Networks → Holds up in dense, high-speed data center circuits.
●Medical Devices → Maintains function in implantable and diagnostic electronics.
By addressing CAF at the material level, Nelco N4800-20 extends operational life, reducing unexpected failures and costly rework.
When Should You Choose Nelco N4800-20 Over Other PCB Materials?
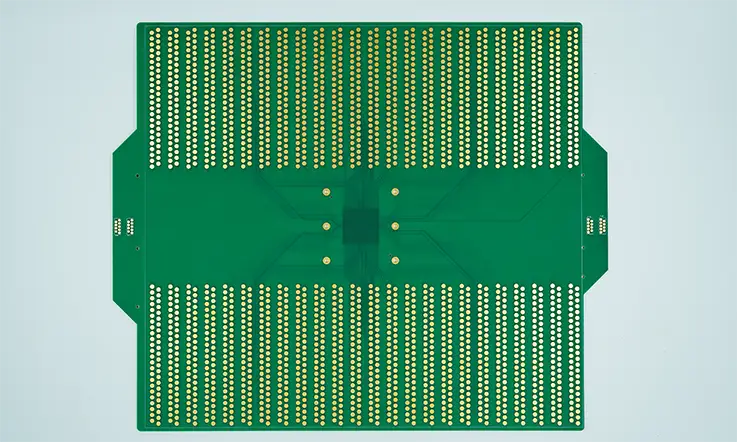
Choosing a PCB material involves multiple factors, such as signal integrity, cost efficiency, and durability. For high-speed, high-frequency applications, laminate selection plays an even bigger role. Comparing Nelco N4800-20 with other options provides better insight for making well-informed decisions.
This material is particularly useful for designs that need excellent high-frequency characteristics, dimensional stability, and reliable performance under both thermal and mechanical stress. Let’s explore when Nelco N4800-20 is the right choice compared to other commonly used PCB laminates.
Nelco N4800-20 vs. PTFE-Based Laminates – Performance, Cost & Processing Considerations
PTFE-based laminates, such as Teflon, are often chosen for low dielectric loss and high-frequency performance. However, they come with higher processing costs and more complex manufacturing processes. These laminates are known for their low thermal conductivity and difficulty in handling during fabrication.
Comparing Nelco N4800-20 to PTFE Laminates-
Aspect | Nelco N4800-20 | PTFE-Based Laminates |
Dielectric Constant (Dk) | ~3.8 | ~2.0-2.2 |
Dissipation Factor (Df) @10 GHz | ~0.0026 | ~0.003 |
Glass Transition Temperature (Tg) | >200°C | ~250°C |
Processing Cost | Lower | Higher due to complex handling and processing |
Manufacturing Ease | Moderate (requires careful handling, but easier than PTFE) | Difficult, requires specialized equipment |
What This Means for Your Design-
●Processing Efficiency: Nelco N4800-20 is generally more cost-effective compared to PTFE-based laminates. Its simpler manufacturing process allows for faster production with fewer complex steps.
●Performance Considerations: While PTFE laminates provide excellent signal performance, Nelco N4800-20 offers a reliable solution for high-frequency and RF applications, while keeping costs in check.
Why High-Density Interconnect (HDI) PCBs Benefit from Nelco N4800-20’s Properties?
HDI PCBs are designed to fit more interconnections into a compact space, accommodating miniaturization in electronics. These designs often require fine-pitch traces, small vias, and increased signal density, all while ensuring optimal electrical and thermal performance.
How Nelco N4800-20 Enhances HDI Designs-
●Dimensional Stability: Nelco N4800-20’s low coefficient of thermal expansion (CTE) keeps vias and traces aligned with precision, making it a strong choice for fine-pitch designs.
●Impedance Control: The material’s low Dk and Df ensure that signal integrity is preserved even in high-frequency circuits.
●Thermal Performance: With excellent thermal stability, Nelco N4800-20 holds up well under high-power applications and thermal cycling, ensuring long-term reliability.
HDI Design Feature | How Nelco N4800-20 Improves Performance |
Microvias | Stable dimensions ensure reliability even after thermal cycling |
Fine-Line Traces | Maintains signal integrity and helps achieve precise impedance matching |
Stacked Layers | Minimizes thermal expansion, preventing layer delamination during assembly |
Why This Matters for Your HDI Designs-
●When dealing with HDI designs, signal integrity and thermal stability are a major concern. Nelco N4800-20 offers the right balance of performance and reliability, making it a reliable choice for dense designs.
●It also brings manufacturing efficiency, helping reduce the overall cost of complex PCBs.
Is Nelco N4800-20 the Best Fit for Your Next PCB Project? Key Factors to Consider
When evaluating materials for your next PCB project, it’s important to consider a variety of factors, such as frequency requirements, thermal considerations, and budget constraints. Nelco N4800-20 is an excellent choice for several high-performance applications, but it may not suit every design. Let’s explore how to determine whether this laminate material is the best fit for your project.
Questions to Consider-
Question | Why It Matters |
What are the frequency requirements of my application? | For high-speed designs, Nelco N4800-20 performs well but may not be the best option for extreme frequencies above 50 GHz. |
What is my material budget? | Nelco N4800-20 is a cost-efficient option for mid-range and high-performance designs. |
What thermal conditions will my PCB face? | Nelco N4800-20’s thermal stability helps it handle heat-intensive applications without affecting performance. |
When Nelco N4800-20 Works Best-
●High-Speed Digital Circuits: For high-frequency applications, this laminate provides a solid balance between performance and cost.
●RF and Microwave Circuits: Nelco N4800-20 excels in maintaining low signal loss for wireless communications.
●HDI Designs: It works well with dense interconnections, maintaining stable signal paths for compact PCBs.
When to Consider Other Options-
●Ultra-High Frequency Circuits: For designs that demand ultra-low Df and extreme performance, PTFE may still be preferable.
●Thin PCBs: If you need thin laminates with specific material flexibility, other specialized materials might be more suitable.
What This Means for Your Project-
Choosing the right laminate comes down to understanding the specific demands of your design and balancing material costs with performance requirements. For many high-speed digital and RF applications, Nelco N4800-20 proves to be a reliable, cost-effective solution.
Manufacturing Innovations – How to Maximize Performance with Nelco N4800-20 Processing
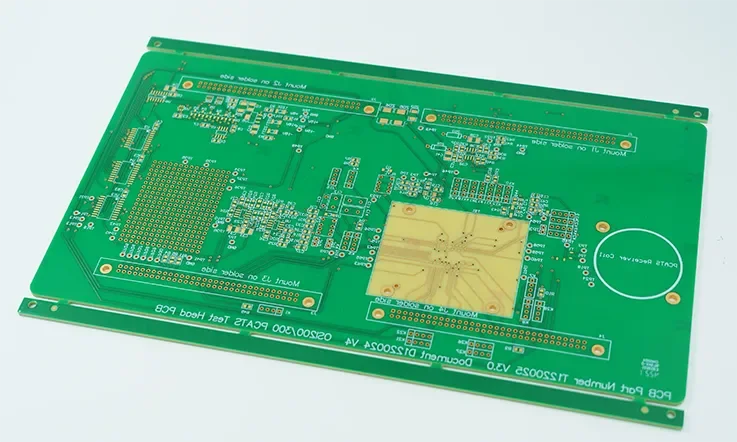
Maximizing the benefits of Nelco N4800-20 starts with careful handling at every production stage. From initial material setup to final assembly, each detail affects the final PCB. Adjusting layer configuration, copper thickness, and processing methods ensures the best possible performance.
This section explores how we can enhance their PCB outcomes by focusing on material handling, defect reduction strategies, and process optimization, ensuring consistency and reliability in high-performance applications.
How to Optimize Multilayer Stack-Up & Copper Thickness for Best Results?
Optimizing multilayer stack-ups and copper thickness is a main factor in working with high-performance laminates like Nelco N4800-20. The structure of the PCB stack-up, along with the correct copper thickness, directly impacts signal integrity and thermal management. Here’s how to approach these aspects for better outcomes:
Stack-Up Configuration and Copper Interaction-
The stack-up configuration defines how layers are arranged in a multilayer PCB, influencing signal performance and thermal management. The thickness of the copper impacts both thermal regulation and structural durability.
Copper Thickness (oz/ft²) | Effect on Performance |
1 oz/ft² | Suitable for designs with moderate signal speeds. |
2 oz/ft² | Enhances power distribution and thermal management. |
3 oz/ft² | Ideal for designs requiring better heat dissipation and signal integrity. |
Optimizing for Nelco N4800-20 Performance-
For Nelco N4800-20, adjusting the stack-up configuration helps enhance signal integrity and manage thermal conditions. Proper layer combinations and choosing the right copper thickness allow the laminate to maintain stable performance under electrical stress and temperature changes.
Design Tips:
●Use power and ground planes to improve performance by providing consistent signal paths.
●Maintain layer balance to avoid issues related to thermal expansion.
●Adjust the distance between signal layers to reduce the risk of crosstalk.
Etching & Lamination Techniques to Minimize Defects with Nelco N4800-20
Etching and lamination are fundamental steps in the manufacturing process that must be managed carefully to prevent defects like delamination or trace lifting. With Nelco N4800-20, here are the best practices for achieving precise results:
Precision Etching-
To achieve clean, accurate traces during the etching process, consider the following:
●Solution Composition: The etching solution should be balanced to ensure even copper removal.
●Etching Duration and Temperature: Control these factors to avoid excessive etching that could damage traces.
●Use of Masking Materials: High-quality masks help define precise areas for etching and avoid contamination.
Optimized Lamination for Nelco N4800-20-
Lamination is core for bonding multiple layers together. To ensure high-quality lamination with Nelco N4800-20:
●Temperature and Pressure Control: These must be carefully monitored to ensure strong bonding between layers.
●Curing Time: Prolonged curing at controlled temperatures ensures a uniform bond.
●Prepreg Thickness Control: Maintaining consistent prepreg thickness across the laminate helps to achieve an even pressure distribution during the process.
Defect Prevention:
By adhering to best practices in etching and lamination, we can reduce defects like delamination and trace lifting, ensuring long-term performance stability for Nelco N4800-20 boards.
The Future of PCB Manufacturing – AI-Driven Fabrication & Process Automation
As the electronics industry advances, AI-driven fabrication and process automation are becoming increasingly integrated into PCB manufacturing. These technologies enhance precision, reduce human error, and streamline processes, especially when working with advanced materials like Nelco N4800-20.
AI in PCB Design and Optimization-
AI can assist in optimizing stack-up configurations and analyzing signal integrity, improving both design efficiency and manufacturing quality. By analyzing large datasets and providing recommendations, AI systems help us ensure the most effective use of materials.
Automation in Manufacturing-
Automation improves consistency across the manufacturing process, ensuring that etching, lamination, and copper deposition are performed with high accuracy. This reduces variation between production runs and enhances the final product’s quality.
AI and Automation in Action-
Incorporating AI and automation into the manufacturing process with Nelco N4800-20 allows us to achieve higher production yields, reduce waste, and streamline operations. These technologies not only improve product quality but also optimize material handling throughout the fabrication process.
The Economic Impact – Is Nelco N4800-20 Worth the Investment?
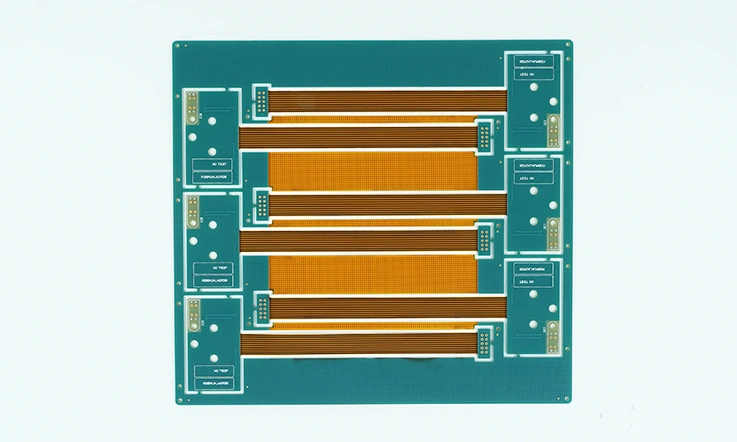
Selecting the right PCB material for advanced applications requires careful thought, balancing both cost and performance. Nelco N4800-20 is designed to meet the demands of high-performance circuits, making it suitable for industries like medical electronics, aerospace, and high-end computing. This section breaks down the financial considerations of adopting Nelco N4800-20, comparing performance versus cost and highlighting how its features can influence the total cost of ownership (TCO).
Cost vs. Performance Analysis: Why High-End Electronics Require High-End Laminates
When dealing with high-frequency applications, selecting the right material goes beyond just price. The overall performance of the laminate becomes a decisive factor in the quality and longevity of the final product. Nelco N4800-20, while priced higher than basic laminates, is engineered for high-reliability scenarios where performance under extreme conditions is non-negotiable. So, if it’s managing signal integrity in complex circuits or dealing with demanding thermal loads, Nelco N4800-20 offers superior performance characteristics that outperform standard materials.
Material Type | Cost per Square Foot | Performance Rating (Frequency Range) | Best Use Case |
Standard FR4 | Lower | Standard frequency ranges | Consumer Electronics |
Nelco N4800-20 | Higher | High-frequency, high-reliability | Aerospace, Medical |
For applications that require precise signal control, Nelco N4800-20 is built to handle high-frequency signals with less signal loss compared to standard materials like FR4. The reduced signal degradation means the circuits maintain signal clarity, better performance, and overall reliability in environments where failure is not an option.
Reducing Total Cost of Ownership (TCO) with Nelco N4800-20’s Durability & Reliability
Considering TCO requires looking at long-term performance, not just initial material costs. Nelco N4800-20 offers extended durability and reliability, which directly impacts the lifecycle costs of a PCB. The material’s ability to resist moisture absorption and thermal stress can reduce the risk of field failures and product recalls, which ultimately lowers the total cost of maintaining and supporting high-reliability products.
Minimizing Rework and Waste-
One of the main contributors to increased costs in PCB manufacturing is the need for rework or dealing with defects that arise during the production phase. Nelco N4800-20’s low Df and low Dk values minimize signal loss and heat generation, which reduces the chances of failure due to manufacturing defects. This results in fewer wasted materials and lower rework costs, making the overall process more cost-effective over time.
How to Balance Material Costs & Yield Optimization in PCB Production?
Yield optimization is a delicate balancing act between controlling material costs and ensuring the highest possible performance from the PCB. Nelco N4800-20 provides a solid foundation for achieving high yields in production by offering exceptional reliability while keeping material usage at a reasonable level.
Optimizing Stack-Up and Copper Thickness-
The stack-up design directly impacts the final product’s performance. By carefully choosing copper thickness and layer arrangement, we can create a balanced design that minimizes material waste and enhances overall functionality. For high-speed applications, Nelco N4800-20 can be configured to optimize signal integrity while avoiding excess material usage.
Process Improvements and Cost Savings-
Improving the PCB manufacturing process through automation and enhanced process control can lead to significant cost savings. Automated systems can help detect defects early, reduce human error, and optimize yield, ensuring that Nelco N4800-20 delivers its performance benefits without excessive material costs.
Optimization Strategy | Impact on TCO |
Optimized Copper Thickness | Reduces material costs while maintaining signal integrity. |
Improved Process Control | Enhances yield rates, minimizing waste and rework. |
Automation in Testing | Improves quality and consistency, lowering failure rates. |
Case Study: How Industry Leaders Are Using Nelco N4800-20 to Push Technological Boundaries
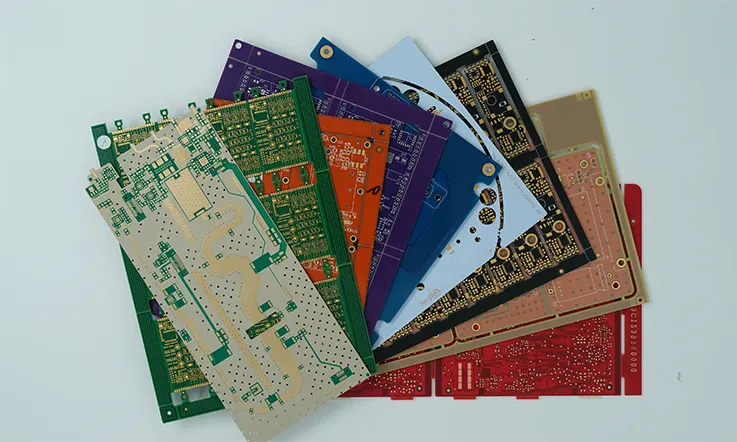
In industries where precision, durability, and electrical performance are necessary, selecting the right material can make the difference between a product that meets expectations and one that doesn’t. From 5G telecommunications to aerospace systems and miniaturized medical devices, there’s a consistent need for PCB materials that provide steady performance, long-term stability, and streamlined processing.
Nelco N4800-20 has been widely adopted by companies facing stringent design challenges, proving its value in applications that demand low dielectric loss, thermal stability, and resistance to harsh conditions. Below are examples of how we are using this advanced laminate to push the limits of technology.
How a 5G Network Provider Improved Signal Integrity with Nelco N4800-20-Based PCBs?
The push for faster data transmission and lower latency in 5G infrastructure has made signal integrity a major concern. Standard PCB materials often struggle to maintain low signal loss at millimeter-wave frequencies, leading to higher bit error rates and weaker network performance.
Challenge:
A leading 5G equipment manufacturer needed a PCB material that could support high-speed signals without introducing unwanted losses or interference.
Solution:
By switching to Nelco N4800-20, the company achieved:
●Reduced signal attenuation across high-frequency bands.
●Improved impedance control for multilayer stack-ups.
●Consistent performance across wide temperature ranges.
Performance Factor | Standard FR4 | Nelco N4800-20 |
Signal Loss (GHz range) | Higher | Lower |
Dielectric Constant (Dk) | 4.5 | 3.7-3.9 |
Moisture Absorption | 0.8% | <0.1% |
Results:
After implementing Nelco N4800-20, the 5G network provider reported a 10-15% reduction in signal degradation, leading to better data throughput and increased efficiency in their network hardware.
How an Aerospace Manufacturer Achieved Unmatched Reliability in Harsh Environments?
Aerospace electronics must function flawlessly in extreme heat, vibration, and radiation. Standard laminates often degrade over time, leading to component failure and costly replacements.
Challenge:
An aerospace defense contractor needed a PCB material that could handle:
●Wide temperature fluctuations from -55°C to 125°C.
●Constant mechanical stress due to aircraft vibrations.
●Exposure to moisture, fuel, and corrosive chemicals.
Solution:
Nelco N4800-20 was chosen due to its:
●Outstanding thermal expansion properties, reducing stress on plated through-holes.
●CAF (Conductive Anodic Filament) resistance, preventing electrical failure over time.
●Superior moisture resistance, protecting circuits from environmental hazards.
Environmental Factor | Standard PCB Materials | Nelco N4800-20 |
Thermal Expansion (Z-axis) | High | Low |
Moisture Absorption (%) | 0.8-1.0% | <0.1% |
Vibration Resistance | Moderate | High |
Results:
After two years of testing, the company found zero PCB failures, increasing the lifetime of their avionics systems and reducing long-term maintenance costs.
Medical Devices & Miniaturization – How Nelco N4800-20 Enables Ultra-Precise Circuits
The medical industry is moving toward smaller, more powerful electronic devices. Wearable health monitors, implantable medical devices, and diagnostic equipment demand high-density PCBs with precise signal transmission.
Challenge:
A medical device manufacturer developing miniaturized imaging equipment needed a PCB material that could:
●Maintain electrical performance in ultra-small traces.
●Resist thermal cycling from sterilization processes.
●Ensure long-term stability for implanted applications.
Solution:
Switching to Nelco N4800-20 allowed the company to:
●Reduce circuit dimensions, enabling more compact designs.
●Enhance reliability, ensuring the device functions for years without degradation.
●Improve processing consistency, minimizing defects during fabrication.
Miniaturization Factor | Standard PCB Materials | Nelco N4800-20 |
Minimum Trace Width | 75 microns | 50 microns |
Thermal Cycling Durability | Moderate | High |
Sterilization Compatibility | Variable | Excellent |
Results:
With Nelco N4800-20, the manufacturer successfully produced a new generation of miniaturized medical imaging devices, allowing higher-resolution diagnostics in a smaller footprint.
Nelco N4800-20 & FAQ
1.Can Nelco N4800-20 be used for RF and microwave applications?
Yes, its low Dk and Df values make it suitable for high-frequency signal transmission.
2.What are the recommended PCB stack-up configurations for Nelco N4800-20?
It depends on application needs, but it works well in multilayer HDI and hybrid PCB designs.
3.Does Nelco N4800-20 require special processing techniques?
Standard PCB fabrication techniques apply, but optimized drilling and lamination parameters help achieve the best results.
4.How does Nelco N4800-20 contribute to reducing PCB manufacturing defects?
Its consistent resin system minimizes delamination, CAF formation, and etching issues.
5.Can Nelco N4800-20 be mixed with other laminates in hybrid PCB designs?
Yes, it can be combined with other materials to balance cost and performance.
6.What industries benefit the most from using Nelco N4800-20?
Aerospace, 5G infrastructure, medical electronics, automotive radar, and high-speed computing.