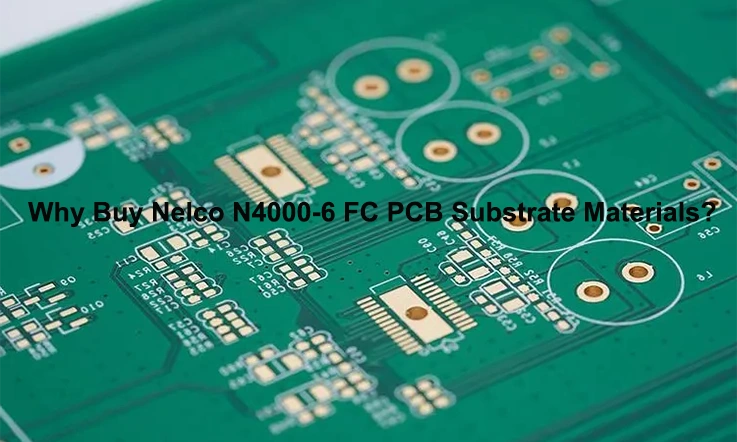
Nelco N4000-6 FC PCB substrate materials are a cutting-edge solution for high-performance electronic applications. Engineered with advanced features and exceptional reliability, these materials have gained widespread recognition in industries such as aerospace, automotive, telecommunications, and more. With a focus on thermal performance, signal integrity, and environmental compliance, Nelco N4000-6 FC offers a comprehensive range of benefits for demanding electronic designs.
Composition of Nelco N4000-6 FC
The composition of Nelco N4000-6 FC PCB substrate materials includes the following components:
1. Reinforcement Material: Nelco N4000-6 FC utilizes a woven glass fabric as the reinforcement material. The glass fabric provides mechanical strength and stability to the substrate.
2. Resin System: The woven glass fabric is impregnated with a flame retardant epoxy resin system. This resin system provides electrical insulation and fire resistance to the substrate.
3. Fillers and Additives: To enhance certain properties of the substrate, fillers and additives may be incorporated into the resin system. These fillers and additives can improve thermal stability, dimensional stability, and other performance characteristics of the material.
It is important to note that the specific composition and formulation of Nelco N4000-6 FC may vary depending on the manufacturer and specific product grade. Manufacturers may have proprietary formulations to achieve specific performance characteristics and meet industry standards. Therefore, it is recommended to refer to the manufacturer’s datasheet or technical documentation for the exact composition details of Nelco N4000-6 FC PCB substrate materials.
Features of Multifunctional Nelco N4000-6 FC
The Nelco N4000-6 FC is a multifunctional PCB substrate material that offers several features and benefits. Some of its key features include:
1.High thermal performance:
The N4000-6 FC has a high glass transition temperature (Tg) of 180°C, which allows it to withstand high operating temperatures without losing its mechanical and electrical properties. This makes it suitable for applications that require high thermal performance.
2.Low loss tangent:
The material has a low loss tangent of 0.010 at 10 GHz, which means it has low signal loss and good signal integrity. This makes it ideal for high-frequency applications such as RF and microwave circuits.
3.Low dielectric constant:
The N4000-6 FC has a low dielectric constant of 3.45 at 10 GHz, which helps in minimizing signal delay and distortion. It also provides excellent electrical performance, especially in high-speed digital circuits.
4.Low coefficient of thermal expansion (CTE):
The material has a low CTE of 17 ppm/°C, which ensures dimensional stability and reliability of the PCB even under extreme temperature variations. This is particularly important for applications that experience frequent temperature cycling.
5.Excellent mechanical properties:
The N4000-6 FC offers high flexural strength and modulus, making it resistant to bending and warping. It also has good dimensional stability, ensuring the PCB maintains its shape and integrity during manufacturing and operation.
6.Compatibility with lead-free assembly processes:
The material is compatible with lead-free assembly processes, which are now mandated by regulations in many countries. It can withstand the higher temperatures required for lead-free soldering without compromising its properties.
7.RoHS and REACH compliance:
The N4000-6 FC is compliant with RoHS (Restriction of Hazardous Substances) and REACH (Registration, Evaluation, Authorization, and Restriction of Chemicals) regulations, ensuring it is free from harmful substances.
Manufacturing and Processing of Nelco N4000-6 FC
The manufacturing and processing of Nelco N4000-6 FC involve several steps and considerations. Here’s an overview of the manufacturing and processing aspects related to Nelco N4000-6 FC PCB substrate material:
1. Material Preparation: Nelco N4000-6 FC is typically supplied as pre-preg sheets or laminates. Pre-preg sheets consist of a fiberglass reinforcement impregnated with epoxy resin. The material is available in various thicknesses and sheet sizes, depending on the specific application requirements.
2. Cutting and Sizing: The Nelco N4000-6 FC pre-preg sheets are cut and sized according to the desired dimensions for the PCB. This process may involve using automated cutting machines or manual cutting methods.
3. Layer Stacking: In multi-layer PCB designs, the individual Nelco N4000-6 FC sheets are stacked together with the appropriate copper foils interleaved between them. The layer stacking process ensures the alignment and registration of the different layers in the PCB stack-up.
4. Lamination: Once the layer stacking is complete, the Nelco N4000-6 FC stack-up goes through a lamination process. The stack-up is placed in a hydraulic press or vacuum press, and heat and pressure are applied to bond the layers together. The heat cures the epoxy resin, creating a solid and stable structure.
5. Drilling: After lamination, the PCB undergoes the drilling process to create holes for component mounting, interconnection, and vias. Special attention should be given to drilling parameters, such as drill bit selection, speed, and feed rates, to ensure clean and accurate holes without damaging the substrate material.
6. Copper Plating: The drilled holes and exposed copper surfaces are typically subjected to a copper plating process. This process involves depositing a thin layer of copper onto the exposed surfaces, ensuring electrical conductivity and facilitating the subsequent steps of the PCB fabrication process.
7. Etching and Imaging: The copper layers are then subjected to a photoresist application and imaging process. The photoresist is selectively exposed to UV light through a photomask, and the unexposed areas are chemically removed through an etching process, defining the copper traces and circuit patterns.
8. Surface Finishing: After etching and imaging, the PCB may undergo surface finishing processes to protect the copper traces and provide solderability. Common surface finishes include HASL (Hot Air Solder Leveling), ENIG (Electroless Nickel Immersion Gold), and OSP (Organic Solderability Preservative).
It’s important to note that the specific manufacturing and processing steps may vary depending on the PCB manufacturer and their specific equipment and processes.
Comparison with Other PCB Substrate Materials
The Nelco N4000-6 FC PCB substrate material is a high-performance material that offers several advantages compared to other PCB substrate materials. Here is a comparison of Nelco N4000-6 FC with other commonly used PCB substrate materials:
1.FR-4:
FR-4 is a widely used PCB substrate material known for its low cost and availability. However, compared to FR-4, Nelco N4000-6 FC offers better electrical properties, including lower electrical loss, improved signal integrity, and higher frequency performance. It also has better thermal stability, allowing it to withstand higher operating temperatures.
2.Rogers RT/duroid:
Rogers RT/duroid is a well-known high-frequency PCB substrate material. While RT/duroid offers excellent electrical performance, Nelco N4000-6 FC provides similar or even better electrical properties at a lower cost. This makes Nelco N4000-6 FC a more cost-effective option for high-frequency applications.
3.PTFE (Teflon):
PTFE-based PCB substrates, such as Teflon, are known for their excellent electrical properties, including low dielectric loss and high thermal stability. However, PTFE materials can be expensive and challenging to process. Nelco N4000-6 FC offers comparable electrical performance to PTFE materials at a lower cost and with easier processing, making it a more practical choice for most applications.
4.Ceramic:
Ceramic PCB substrates are known for their excellent thermal conductivity and high-temperature resistance. They are commonly used in power electronics and high-power applications. While Nelco N4000-6 FC may not match the thermal conductivity of ceramic materials, it offers good thermal stability and electrical performance at a significantly lower cost. It is also easier to manufacture and handle compared to ceramic substrates.
Applications and Qualifications of Nelco N4000-6 FC PCB Substrate Materials
The Nelco N4000-6 FC PCB substrate material has a wide range of applications across various industries. Some of the common applications include:
1. High-frequency RF and microwave circuits: The low loss tangent and low dielectric constant of the N4000-6 FC make it suitable for high-frequency applications, such as wireless communication systems, radar systems, satellite communication, and microwave devices.
2. High-speed digital circuits: The low dielectric constant and excellent electrical performance of the material make it ideal for high-speed digital circuits, such as high-speed data transmission, servers, routers, and other high-performance computing applications.
3. Automotive electronics: The N4000-6 FC’s high thermal performance, dimensional stability, and compatibility with lead-free assembly processes make it suitable for automotive electronics, including advanced driver-assistance systems (ADAS), infotainment systems, and engine control units (ECUs).
4. Aerospace and defense: The material’s high thermal performance, low signal loss, and excellent mechanical properties make it suitable for aerospace and defense applications, such as avionics systems, radar systems, communication equipment, and military-grade electronics.
5. Industrial equipment: The N4000-6 FC’s dimensional stability, high flexural strength, and compatibility with lead-free assembly processes make it suitable for industrial equipment, including power electronics, motor control systems, and automation systems.
In terms of qualifications, the Nelco N4000-6 FC PCB substrate material meets various industry standards and qualifications, including:
1. UL 94 V-0 flame rating: The material is self-extinguishing and meets the UL 94 V-0 flame rating, ensuring it has excellent fire resistance.
2. IPC-4101/21 and IPC-4101/24 qualifications: The material meets the requirements of IPC-4101/21 and IPC-4101/24, which are industry standards for high-performance multilayer printed boards.
3. RoHS and REACH compliance: The N4000-6 FC is compliant with RoHS and REACH regulations, ensuring it is free from hazardous substances.
4. ISO 9001 and ISO 14001 certifications: The manufacturer of the material holds ISO 9001 and ISO 14001 certifications, indicating their commitment to quality management and environmental responsibility.
These qualifications ensure that the Nelco N4000-6 FC PCB substrate material meets the necessary standards and requirements for reliability, safety, and environmental compliance in various applications.
Conclusion
In conclusion, the Nelco N4000-6 FC PCB substrate materials prove to be an excellent choice for electronic manufacturers seeking high-performance solutions. With their exceptional thermal performance, low signal loss, dimensional stability, and compatibility with lead-free assembly processes, these materials enable the development of reliable and efficient electronic circuits.
Further, RoHS and REACH compliance ensures environmental responsibility and product safety. Whether it’s for high-frequency RF and microwave circuits or high-speed digital applications, Nelco N4000-6 FC delivers the reliability and versatility that industry professionals demand. By choosing Nelco N4000-6 FC PCB substrate materials, manufacturers can ensure the success of their electronic projects while staying ahead in today’s competitive market.