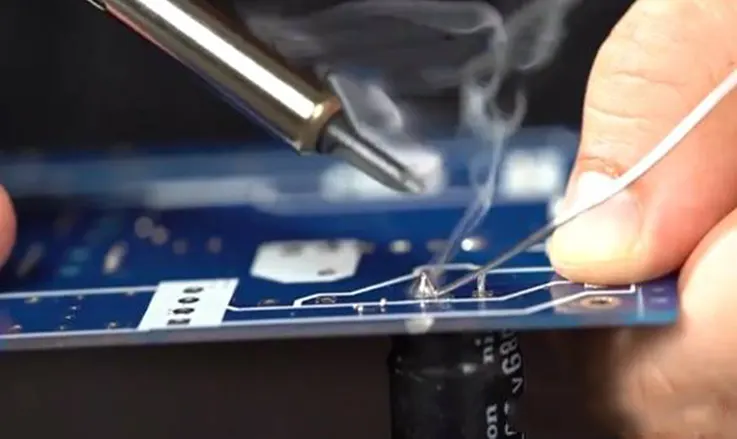
For a prolonged period, lead solder has been the preferred material for employment in PCB manufacturing. However, there has been a recent upswing in apprehensions of consumers regarding the environmental and health effects of products containing lead. As a result, the European Union’s Restriction of Hazardous Substances in Electrical and Electronic Equipment (RoHS) Regulation mandating the restrictions on leaded electronic products was enacted in July 2006.
Despite the absence of legal restrictions on the utilization of lead in consumer goods in certain countries, including the United States, some businesses demand lead solder usage for their electronic products. Given this scenario, which solder is considered the optimal choice for use within the electronics industry ?
This article will provide an overview of lead and lead-free solder, their characteristics and properties, and a comparison of their advantages and disadvantages. By examining these factors, we hope to provide a better understanding of the use of solder in various industries and the current trends towards more sustainable and environmentally friendly solutions.
Roles of Solder in Electronics Manufacturing
● Solder is a fundamental aspect of electronic device manufacturing, as it is used to join electronic components, such as resistors, capacitors, diodes, and integrated circuits, to a printed circuit board (PCB). This soldered joint provides mechanical stability, electrical conductivity, and thermal transfer between the component and the PCB.
● Without good quality and proper application of solder, these connections can become weak or fail entirely, leading to unreliable or non-functioning electronic devices. For example, a poor solder joint could result in a lack of electrical connectivity between the component and PCB, leading to a malfunction in the device.
● Additionally, the quality and composition of solder used for electronic devices affects their overall reliability and performance. The properties of solder (such as melting temperature, thermal expansion coefficient, and electrical conductivity) must be compatible with the electronic components being soldered to the PCB and the temperature requirements of the manufacturing process.
In a word, solder plays a critical role in electronics manufacturing by ensuring that electronic components and PCBs are connected in a secure and reliable way, allowing for functional and durable electronic devices.
What is Solder ?
Solder, a metal alloy, is applied to bond two metals, with extensive use, in electronics production. A variety of solder types cater to different metals to be joined, sorted by three elemental features, namely:
● Composition
● Core Style
● Form
It’s crucial that the solder’s melting temperature remains inferior to that of the metals being joined.
In electronics, soldering refers to the process of connecting one component to a printed circuit board by heating a metallic junction. Assemblers then apply solder to the joint to create a strong, durable bond before cutting the component leads. This action secures the electronic component to the circuit board, rendering it functional.
Many PCB Hardware Electronic engineers, it can be challenging to select the appropriate solder given the multitude of options available in the market. However, you can simplify your search by concentrating on the two fundamental types of solder, which include distinct categories based on:
● Lead Solder.
● Lead Free Solder.
By using these parameters, you should be able to narrow down your selection to identify the optimal solder type for your specific project requirements.
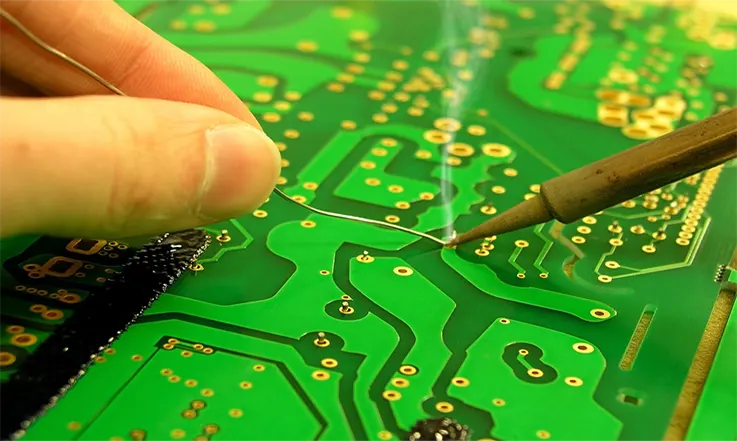
Lead Solder
As PCB assembly manufacturers, it is essential to understand that SNPB solder, or lead solder, is a metal alloy primarily composed of lead (Pb) and tin (Sn). There has been increasing awareness of the potential occupational risks associated with lead soldering, which is leading to it being seen as a health concern within the workplace. This is due to the fact that lead solder is a toxic substance, and the dust and vapours created during soldering can contain neurotoxic elements that pose risks to human health.
Due to its detrimental impact on both human health and the environment, lead solder is gradually being phased out of production processes. Despite its undeniable benefits, it is crucial to adopt alternative soldering methods that are safer and more sustainable in the long run. As printed circuit boards factory, it is our responsibility to prioritize the health and well-being of workers and the wider community while still ensuring the effectiveness and reliability of electronic manufacturing processes.
Advantages of Lead Solder
Lead solder offers several advantages over lead-free alternatives:
● Firstly, it produces fewer joint quality issues and reduces the risk of harmful thermal effects on soldered components due to its lower melting point of 183°C, compared to lead-free solder at 217°C.
● Furthermore, lead solder exhibits a brighter color when cooling, which makes it easier to identify potential issues such as oxidation. This color distinction aids in the detection of any anomalies in the soldering process and assists in ensuring the quality of the final product.
● Lastly, lead solder is more cost-effective and easier to use than lead-free solder, as it costs only ten times as much as tin-based substitute solders. This affordability and ease of use make lead solder a more accessible and widely used option in electronic manufacturing. However, it is important to consider the potential health and environmental risks associated with lead solder and to make informed decisions accordingly.
Disadvantages of Lead Solder
● As electronic manufacturers, preserving the environment and ensuring the safety and well-being of workers are paramount concerns. The neurotoxic properties of lead are a significant cause for the increasing adoption of lead-free solder as a safer alternative to lead-based solder.
● Even minor but prolonged exposure to lead can result in its accumulation in the human body, leading to potential health risks. Workers engaged in industries with high lead emissions from production processes face continuous exposure to lead hazards by inhaling lead vapors or via contact with contaminated surfaces. Lead can also quickly enter the body through the skin, mouth, or nose.
● To this end, there has been a phase-out of lead-based paints, a shift towards unleaded petrol, and increasing adoption of lead-free soldering practices among EMS service providers. The RoHS directive (Restriction of Hazardous Substances) implemented by the European Union (EU) in 2006 and tax credits provided in 2008 by the United States to businesses that reduced their usage of lead-based solders highlight the growing awareness of the need to minimize the use of lead and other hazardous substances, especially in the production of electronic manufacturing equipment.
The adoption of lead-free soldering presents a viable solution that is safer and gaining momentum in the electronics manufacturing industry to safeguard worker health while also prioritizing environmental conservation.
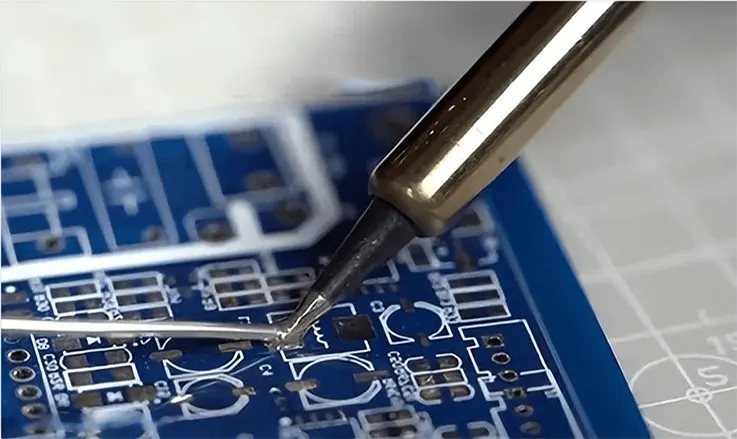
Lead Free Solder
In the electronics industry, lead-free solders have emerged as a viable alternative to commonly used 60/40 and 63/37 SnPb lead solders. These solders are composed of elements such as copper, tin, silver, nickel, zinc, bismuth, and antimony, among others, and are often reinforced with trace metals to enhance their mechanical properties.
By incorporating various elements and trace metals, lead-free solders produced offer superior mechanical properties, meeting stringent quality requirements. Their mechanical properties often surpass those of traditional lead-based solders, promoting longer-lasting, high-quality products.
Tin-copper, a lead-free soldering compound, is the most widely used alternative, with a composition of 99.3 percent tin and 0.7 percent copper and a melting point of 217 degrees Celsius. The utilization of these elements produces high-performance solder alloys that are easy to work with and offer high-quality mechanical properties that meet the required standards.
By adopting alternatives to traditional lead-based solders, such as tin-copper, PCBA manufacturers can reduce their impact on the environment while delivering products that meet the highest industry standards.
Advantages of Lead Free Solder
The utilization of non-lead solders in electronic manufacturing processes is gaining popularity due to their positive impact on both the environment and human health. As a consequence, a growing number of EMS manufacturers and service providers are opting for lead-free soldering. This trend is driven by a common commitment among electronic engineers to reduce the ecological footprint of their products, while simultaneously enhancing the well-being of industry personnel.
Disadvantages of Lead Free Solder
It has been acknowledged that the use of lead solders is backed by a sound rationale as a result of the distinct characteristics of lead-free solders. These characteristics may render lead-free solders unsuitable for certain purposes. Thus, it is reasonable for certain industries and applications to rely on lead solders to meet their specific needs.
● Lead-free solders pose greater challenges in terms of workability when compared to solders containing lead. This is due to their inferior surface wettability and a softer composition as compared to lead solder, which makes it more difficult to achieve comparable joint dependability. Moreover, lead-free solders tend to form surface oxides, flux contamination, and alloy deposits, which may lead to insufficient contact resistance. As a result, switching from lead-containing solder to lead-free solder may not provide the same level of electrical and mechanical qualities of the solder joint.
● It is worth noting that wire flux core and lead-free fluxes often comprise severe reducing agents that can cause substantial irritation to employees’ mucous membranes. Prolonged exposure to these substances can cause sinus, throat, and eye irritation, thus posing a potential threat to the health and safety of workers.
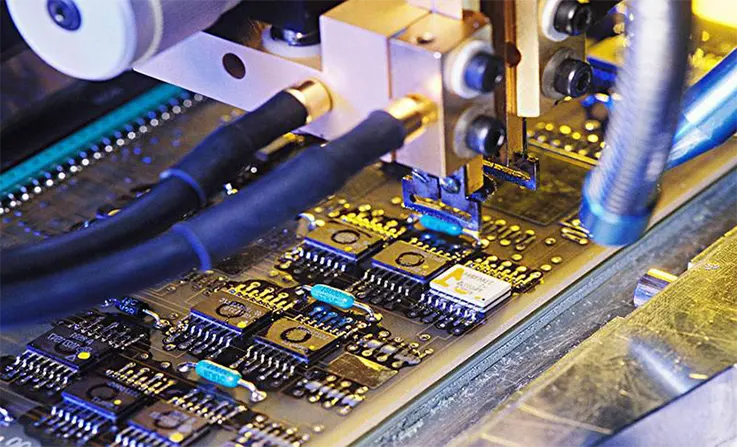
How to Choose the Right Type of Solder ?
To choose the right type of solder for your application, consider the following factors:
● Composition: Decide whether you want leaded or lead-free solder. Lead-free solder is often required by regulations, but leaded solder may still be used in some applications.
● Melting point: Look for a solder alloy with a melting point appropriate for your application. Higher melting point solders may be more suitable for applications that require higher temperatures or involve heat-sensitive components.
● Flux: Consider the type of flux that is best suited for your application. Some solders come with a built-in flux core, while others require a separate flux application.
● Size: Choose a solder diameter appropriate for the size of the components being soldered. Thicker solder may be needed for larger components or heavier connections.
● Application method: Consider the method of application, such as hand-soldering, wave soldering, or reflow soldering, and choose a solder alloy that is compatible with the equipment and techniques being used.
● Environmental considerations: Consider any environmental or safety concerns related to the materials and processes used in your application, and choose a solder alloy that meets the appropriate regulatory standards.
● Compatibility: If you are working with pre-existing components or surfaces, consider the materials being used and choose a solder alloy that is compatible with those materials.
In addition, consult with the manufacturer or supplier of the solder for guidance on choosing the appropriate type of solder for your specific application.
Comparison of Lead Solder and Lead-Free Solder
● Chemical composition: Lead solder typically contains lead and tin, whereas lead-free solder may contain a variety of other metals, such as silver, copper, and zinc.
● Melting point: Lead solder typically has a lower melting point than lead-free solder. This can make it easier to work with but may also make it less reliable under certain conditions.
● Strength and durability: Lead solder tends to be more ductile and have higher tensile strength than lead-free solder. However, lead-free solder can be engineered to have similar properties.
● Environmental impact: Lead solder is known to be toxic to humans and the environment. As a result, many countries have banned or restricted its use. Lead-free solder is generally considered to be more environmentally friendly.
● Cost: Lead-free solder can be more expensive than lead solder, depending on the specific composition and manufacturing process.
● Compatibility: Lead-free solder may not be compatible with some older components or manufacturing equipment that were designed for use with lead-based solder.
These are just a few factors to consider when comparing lead and lead-free solder. The choice of which type to use will depend on the specific application and any relevant regulations or industry standards.
When to Use Lead Solder or Lead Free Solder ?
Whether to use lead or lead-free solder may depend on several factors, including the specific application, local regulations, and personal preferences. Here are some considerations:
● Application: Lead-based solder may provide better flow, wetting, and adhesion characteristics and may be preferred when working with certain materials or components. On the other hand, lead-free solder has a higher melting point and may be better suited for high-temperature applications.
● Regulations: In many regions, the use of lead-based solder is restricted or banned due to environmental and health concerns. In such cases, lead-free solder is the only option.
● Compatibility: Lead-free solder may not be compatible with some older components or equipment designed for lead-based solder. This may require modifications or replacement of parts to ensure proper performance.
● Safety: Lead-based solder releases hazardous fumes when melted, and exposure can lead to lead poisoning. However, if proper ventilation and safety precautions are taken, the risk can be minimized.
In general, if environmental regulations allow and compatibility is not an issue, lead-based solder may be preferred for its ease of use and excellent wetting properties. However, if environmental concerns or safety considerations are a factor, lead-free solder may be the better option. Ultimately, the choice of solder will depend on the particular application and the specific requirements of the user.
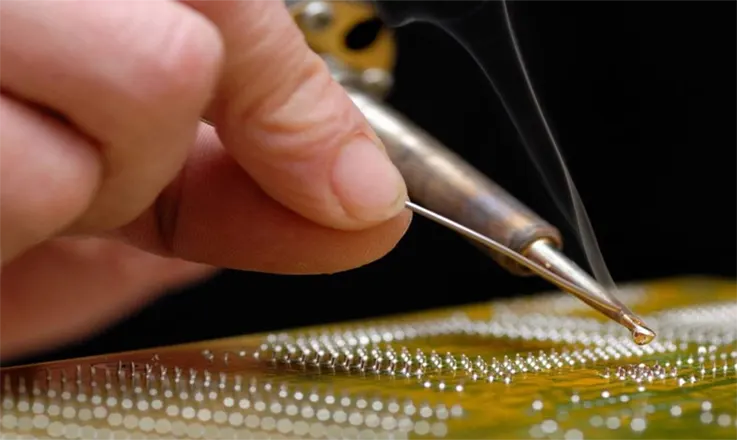
Safety Precautions when Working with Solder
Here are some possible safety precautions when working with solder:
● Use proper ventilation: Soldering releases fumes that can be harmful if inhaled, so it’s important to work in a well-ventilated area or use a fume extractor.
● Wear protective equipment: Safety glasses can protect your eyes from hot solder or debris, while gloves and aprons can protect your hands and clothing from burns.
● Avoid skin contact: Solder can get very hot and cause burns if it comes into contact with skin. Avoid touching hot solder, and wash your hands thoroughly after working with it.
● Use the right equipment: Make sure you use the right soldering iron or gun for the job, and keep it in good condition. Check that the equipment is grounded and has no exposed wires.
● Store solder safely: Keep solder and flux in sealed containers in a cool, dry place, away from heat sources and open flames.
● Dispose of waste safely: Used solder and flux can be hazardous waste and should be disposed of properly. Check with your local authorities for guidelines.
● Know what to do in case of emergency: Have a fire extinguisher nearby and know how to use it. Know where the first aid kit is located, and seek medical attention if you get burned or exposed to fumes.
Future Directions and Challenges in Solder Technology
The field of solder technology is constantly evolving to address emerging challenges and requirements in electronics manufacturing. Some future directions and challenges in solder technology include:
● Lead-free solder: The use of lead in solder has environmental and health concerns, and regulations worldwide are shifting towards lead-free solder. However, lead-free solder has its own technical challenges due to its higher melting temperature and effects on reliability.
● Miniaturization: Electronic devices are continually becoming smaller and more compact. This presents challenges for soldering smaller components, as well as for ensuring that the solder joint is reliable and mechanically resilient.
● Alternative materials: New materials and alloys are being developed to improve the properties of solder and address environmental concerns. For example, there is interest in using various metals, such as copper, silver, and bismuth, in solder alloys.
● Advanced manufacturing techniques: Advanced manufacturing techniques, such as 3D printing and laser-assisted soldering, have the potential to improve precision and control in soldering, as well as enable new designs and functionality.
● Thermal management: The increasing power density of electronic devices requires improved thermal management, which can affect the properties and performance of solder joints. New thermal management techniques are being explored to address this challenge.
Summary
Solder is a metal alloy that is used to create a permanent bond between two metal surfaces in a variety of applications. While traditional lead-based solder had long been used, modern environmental concerns have led to the increased use of lead-free solder. Choosing the right type of solder for an application and using proper techniques are important for achieving a strong and reliable bond while ensuring safety and environmental responsibility. With the right equipment and precautions, soldering can be a useful and necessary skill in many industries.
The utilization of lead solder in the production of electronics has been widely favored due to its numerous advantages. However, it is evident that the shift towards lead-free soldering is inevitable and may occur shortly across all industries that frequently use solder in their processes.
At JarnisTech, we are a PCB manufacturing and assembly factory, we understand that varied projects may necessitate the utilization of different soldering techniques. Hence, we offer both lead and lead-free soldering options specifically for PCB assembly. Whether you require any of these distinct soldering methods, we are ready to provide you with tailored services. Contact us now to receive a no-obligation quotation for turnkey PCB assembly.