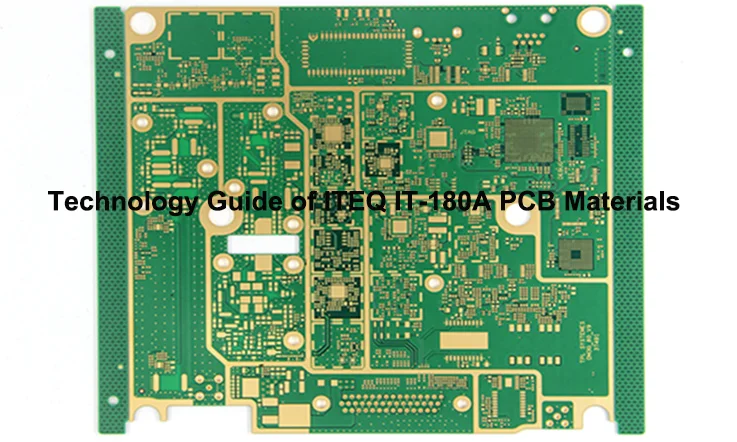
ITEQ IT-180A is a high-performance PCB material that offers exceptional thermal reliability and stability. It is specifically designed for demanding applications that require high glass transition temperature (Tg) and resistance to conductive anodic filamentation (CAF). With its unique combination of properties, IT-180A provides reliable insulation and superior thermal performance for complex PCB designs.
Therefore, we invite you to delve deeper into the world of IT-180A. In this article, we will explore the properties, processing guidelines, key features, benefits, and various applications of this exceptional material. By continuing to read, you will gain a comprehensive understanding of the subject matter at hand.
Introduction of ITEQ IT-180A
Iteq 180A is a high-Tg (glass transition temperature) laminate that is meticulously crafted with a phenolic-cured resin system. This laminate is specifically designed to cater to the requirements of applications demanding exceptional thermal reliability. With its remarkable low coefficient of thermal expansion (CTE) and resistance to conductive anodic filamentation (CAF), Iteq 180A stands as an exemplary base material for printed circuit boards (PCBs).
Manufactured using a phenolic-hardened epoxy resin system, Iteq 180A boasts a glass transition temperature of no less than 175°C. This high glass temperature serves as a testament to the material’s ability to withstand elevated thermal conditions reliably. In fact, Iteq 180A is particularly well-suited for applications that impose rigorous thermal demands.
One of the distinguishing features of Iteq 180A is its impressive decomposition temperature, surpassing 345°C. This exceptional attribute renders it an ideal choice for applications exposed to high thermal stress. Additionally, its resistance to conductive anodic filamentation (CAF) makes it highly suitable for the fabrication of multi-layer boards, where the prevention of conductive paths is paramount.
Features of ITEQ IT-180A PCB Materials
The features of Iteq IT-180A PCB materials include:
1. High thermal performance: IT-180A has a high glass transition temperature (Tg) of 180°C, allowing it to withstand high temperatures during operation and soldering processes.
2. Low thermal expansion: The material has a low coefficient of thermal expansion (CTE), which helps to reduce stress and ensure dimensional stability in different temperature environments.
3. Excellent electrical performance: IT-180A has low dielectric loss and low dissipation factor, enabling high signal integrity and low signal loss in high-frequency applications.
4. Good mechanical strength: The material offers good mechanical strength and rigidity, ensuring the reliability and durability of PCBs even in harsh conditions and during handling.
5. RoHS compliance: IT-180A is compliant with RoHS (Restriction of Hazardous Substances) regulations, ensuring that it does not contain harmful substances like lead, mercury, or cadmium.
6. Compatibility with lead-free soldering: The material is suitable for lead-free soldering processes, meeting the requirements of modern electronics manufacturing.
7. Stable electrical properties over a wide frequency range: IT-180A maintains consistent electrical properties across a wide frequency range, enabling reliable performance in various applications, including high-speed digital and RF circuits.
8. Good chemical resistance: The material has good resistance to chemicals, making it suitable for use in environments where exposure to corrosive substances may occur.
9. High reliability: IT-180A is designed to provide high reliability and long-term performance, making it suitable for applications in industries such as telecommunications, automotive, aerospace, and medical.
10.Availability in various thicknesses: IT-180A is available in a range of thicknesses to suit different design requirements and PCB stack-up configurations.
How to Ensure IT-180A PCB Materials Quality?
Manufactured by ITEQ Corporation, a renowned industry leader, Iteq 180A exemplifies their commitment to delivering cutting-edge base materials for PCBs. With its high-Tg composition, phenolic-cured nature, and impressive thermal resilience, Iteq 180A stands as a premier choice for applications that demand exceptional thermal reliability and performance.
To ensure the superior quality and performance of Iteq 180A, the manufacturing process incorporates a UV blocker. This additive serves to enhance the material’s overall properties and characteristics, further solidifying its reliability and durability.
How Many Test Method for IT-180A Laminate?
To test the efficiency of IT-180A laminate, you can perform the following tests:
1.Thermal performance testing:
Measure the thermal conductivity and thermal resistance of IT-180A laminate using a thermal conductivity tester or thermal imaging camera. This will help evaluate how well the material dissipates heat and its ability to withstand high temperatures.
2.Mechanical strength testing:
Conduct mechanical strength tests such as tensile strength, flexural strength, and impact resistance tests to assess the material’s ability to withstand mechanical stress and shocks. This can be done using universal testing machines or impact testers.
3.Electrical performance testing:
Measure the dielectric constant, dissipation factor, and insulation resistance of IT-180A laminate using high-frequency impedance analyzers or LCR meters. This will help evaluate its electrical properties and performance in high-frequency applications.
4.Chemical resistance testing:
Expose IT-180A laminate to various chemicals, such as acids, bases, and solvents, to assess its resistance to chemical corrosion. The material should be inspected for any signs of degradation or discoloration.
5.RoHS compliance testing:
Verify the compliance of IT-180A laminate with RoHS regulations by conducting elemental analysis using X-ray fluorescence (XRF) or other appropriate testing methods.
6.Electrical reliability testing:
Perform accelerated aging tests, such as temperature cycling and humidity testing, to evaluate the material’s electrical reliability. This can be done by subjecting the laminate to controlled temperature and humidity conditions over an extended period while monitoring its electrical performance.
7.Adhesion testing:
Evaluate the adhesion strength between the copper layers and IT-180A laminate by conducting peel strength tests. This can be done using a peel tester to determine the bond strength and reliability of the laminate.
8.Dimensional stability testing:
Measure the coefficient of thermal expansion (CTE) of IT-180A laminate using a thermal dilatometer to assess its dimensional stability over a range of temperatures.
Processing Guidelines of the ITEQ IT-180A
The processing guidelines for IT-180A laminate include the following:
1. Storage and handling: Store IT-180A laminate in a controlled environment, preferably at a temperature of 20-25°C and relative humidity of 55-65%. Handle the laminate with clean gloves to prevent contamination.
2. Cutting and shaping: Use appropriate cutting tools, such as carbide or diamond-tipped blades, to cut IT-180A laminate to the desired size and shape. Ensure clean and precise cuts to avoid delamination or damage to the material.
3. Drilling: Use high-speed steel (HSS) or carbide drills with proper cutting parameters to drill holes in the IT-180A laminate. Maintain proper drill speeds, feed rates, and coolant to prevent overheating and minimize drill bit wear.
4. Lamination: Use a suitable adhesive system compatible with IT-180A laminate to bond the layers together during lamination. Follow the manufacturer’s recommendations for the adhesive material and the lamination process parameters, such as temperature, pressure, and time.
5. Cleaning: Thoroughly clean the IT-180A laminate surface before any subsequent processes, such as solder mask application or component assembly. Use a mild detergent or cleaning agent, followed by rinsing with deionized water, and dry the surface completely.
6. Solder mask application: Apply a suitable solder mask material onto the IT-180A laminate surface using a screen printing or spray coating method. Follow the manufacturer’s instructions for the proper application and curing parameters, including temperature and time.
7. Component assembly: Follow standard PCB assembly processes for mounting components on IT-180A laminate. Ensure appropriate soldering techniques, such as reflow soldering or wave soldering, and use compatible solder materials and fluxes.
8. Finishing: Apply appropriate surface finishes, such as immersion gold, HASL (Hot Air Solder Leveling), or ENIG (Electroless Nickel Immersion Gold), to protect the exposed copper traces and pads. Follow the recommended processes and parameters for the chosen surface finish.
It is important to consult the manufacturer’s datasheet and processing guidelines specific to IT-180A laminate for detailed instructions and recommendations.
Factors that Affect the Cost of ITEQ IT-180A
Several factors can influence the cost of Iteq 180A laminate. These factors include:
1.Material Specifications:
The specific features and properties of the Iteq 180A laminate can impact its cost. For example, if the laminate is manufactured with additional additives or enhancements to meet specific performance requirements, it may result in a higher cost compared to standard versions.
2.Laminate Thickness:
The thickness of the Iteq 180A laminate can affect its cost. Thicker laminates generally require more material and manufacturing processes, which can contribute to higher costs. Thinner laminates, on the other hand, may be more cost-effective but could have limitations in terms of certain performance characteristics.
3.Quantity:
The quantity of Iteq 180A laminate being purchased can influence the cost. Bulk orders or larger quantities typically offer economies of scale, resulting in lower unit costs. Conversely, smaller orders or prototype quantities may have a higher per-unit cost.
4.Customization and Special Requirements:
Any customization or special requirements for the Iteq 180A laminate can impact the cost. For instance, if specific surface finishes, copper weights, or other variations are needed, it may result in additional manufacturing steps or materials, leading to increased costs.
5.Market Conditions:
Market factors such as supply and demand dynamics, raw material availability, and fluctuations in manufacturing costs can influence the overall cost of Iteq 180A laminate. These factors can vary over time and may affect the pricing of the material.
6.Supplier and Location:
The choice of supplier and their location can affect the cost of Iteq 180A laminate. Different suppliers may have varying pricing structures and overhead costs, which can impact the final cost. Additionally, shipping and logistics costs may vary based on the supplier’s location and proximity to the manufacturing facility.
Applications of ITEQ IT-180A
Iteq 180A finds diverse applications across the electronics industry where thermal reliability and exceptional performance are vital. Some prominent applications of Iteq 180A include:
1. High-Temperature Electronics: Iteq 180A’s high glass transition temperature and excellent thermal stability make it an ideal choice for electronic devices that operate in elevated temperature environments. It provides reliable performance in applications such as automotive electronics, aerospace systems, and industrial equipment.
2. Power Electronics: Iteq 180A’s low coefficient of thermal expansion (CTE) and outstanding thermal conductivity make it well-suited for power electronic modules and devices. It efficiently dissipates heat, ensuring the longevity and reliability of power components, such as inverters, motor drives, and power supplies.
3. Communication Systems: The high thermal reliability and CAF resistance of Iteq 180A make it highly suitable for communication systems, including base stations, routers, and network switches. These systems often experience temperature variations and require materials that can withstand thermal stress and provide stable electrical performance.
4. Automotive Electronics: With its ability to withstand high temperatures and resist thermal cycling, Iteq 180A is widely used in automotive electronics. It is employed in applications such as engine control units, lighting systems, infotainment systems, and advanced driver-assistance systems (ADAS), ensuring reliable operation in demanding automotive environments.
5. Industrial Controls: Iteq 180A is well-regarded in industrial control applications due to its thermal reliability, stability, and resistance to CAF. It is commonly used in programmable logic controllers (PLCs), motor control systems, and other industrial automation devices.
6. LED Lighting: LED lighting systems often require materials with superior thermal management capabilities. Iteq 180A’s high glass transition temperature and CAF resistance make it an excellent choice for LED modules and drivers, ensuring reliable and efficient operation of LED lighting products.
These are just a few examples of the wide range of applications where Iteq 180A serves as a reliable and high-performance base material for PCBs. Its exceptional thermal reliability, low CTE, CAF resistance, and high glass transition temperature make it a preferred choice for demanding electronic applications across various industries.
In Conclusion
ITEQ IT-180A is an advanced PCB material that meets the stringent requirements of thermally demanding applications. With its high Tg, low CTE, and resistance to CAF, it ensures reliable performance and long-term reliability. Manufactured with a phenolic-hardened epoxy resin system, IT-180A offers exceptional thermal stability and can withstand high temperatures without significant degradation. Its compatibility with sequential lamination processes and 260°C lead-free assembly makes it a versatile choice for various PCB designs. ITEQ IT-180A is an excellent solution for engineers and designers seeking a reliable and high-performance PCB material.