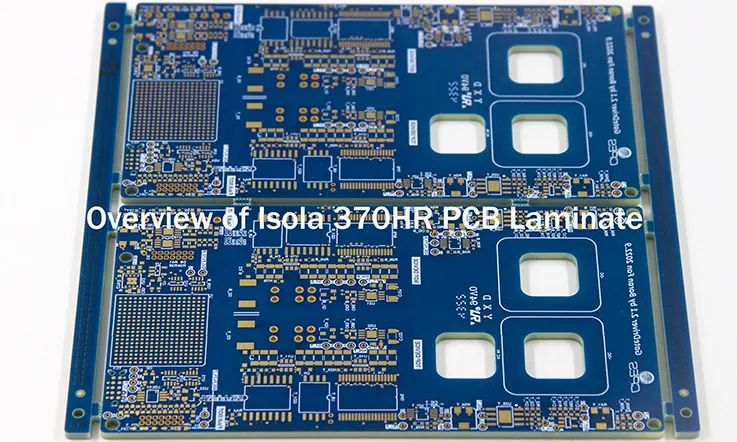
Isola 370HR is a high-Tg, low-loss PCB laminate engineered for demanding multilayer circuit designs. Widely used in aerospace, medical, and high-speed data applications, it offers excellent thermal stability, CAF resistance, and dielectric performance. This material excels in HDI fabrication, rigid-flex integration, and embedded component technology, making it a go-to choice for high-reliability PCBs. From signal integrity optimization to thermal cycling durability, Isola 370HR supports cutting-edge manufacturing needs. Explore how this advanced laminate enhances PCB performance, ensuring superior reliability and efficiency in modern electronic designs.
What is Isola 370HR PCB Laminate?
When designing multilayer circuit boards, the material you choose for the laminate has a direct impact on the performance and longevity of your PCBs. Isola 370HR PCB laminate has been engineered to deliver exceptional thermal stability, electrical performance, and mechanical reliability. It is a main choice for applications where consistent performance under stress is needed.
This laminate material is engineered with the needs of modern electronics in mind. So, if you’re working on 5G networks, automotive electronics, or high-speed communication systems, Isola 370HR offers a robust foundation that ensures the PCB design will hold up under the rigorous demands of modern applications.
Let’s break down the core features of Isola 370HR PCB laminate and understand why it’s a reliable choice for advanced electronics.
Understanding the Composition of Isola 370HR PCB Laminate
The composition of Isola 370HR makes it stand out from other PCB laminates. It’s crafted from a specialized blend of epoxy resins and reinforcing fibers that provide superior thermal stability and mechanical strength. These materials are combined in a way that ensures the laminate remains stable under high-stress conditions.
Material Breakdown-
●Epoxy Resin System: The epoxy resin system used in Isola 370HR is designed to withstand high temperatures and ensure the board maintains its integrity during prolonged use. This resin system helps manage heat dissipation, preventing performance degradation.
●Reinforcing Fibers: Isola 370HR incorporates glass fibers that enhance the mechanical strength of the laminate. This structure ensures the laminate resists deformation and warping during manufacturing and under extreme conditions.
●Additives for Improved Dielectric Properties: Specific additives are included to enhance the dielectric properties of the laminate, ensuring minimal signal loss and excellent signal integrity.
This combination of materials ensures that Isola 370HR excels in applications where high performance and durability are needed over long periods.
Why Isola 370HR PCB Laminate is Ideal for High-Tg PCB Applications?
High glass transition temperature (Tg) materials like Isola 370HR are engineered to handle elevated temperatures without compromising performance. The Tg of Isola 370HR is rated at 180°C, making it ideal for use in high-temperature environments where other materials might fail.
Why High-Tg Matters-
●Thermal Cycling Resistance: Isola 370HR is able to withstand multiple heating and cooling cycles, maintaining its mechanical and electrical properties even when subjected to these temperature shifts. This capability is particularly valuable in applications where frequent temperature fluctuations are common.
●High-Performance Systems: For systems where high-speed signal transmission is needed, Isola 370HR ensures that the integrity of the signals remains intact under stress, maintaining low levels of signal loss.
By offering high thermal stability, Isola 370HR reduces the risk of board failure during demanding operating conditions. This material performs exceptionally well in environments where reliable heat management is required.
Advantages of Isola 370HR PCB Laminate in Multilayer Circuit Boards
In multilayer circuit boards (MLBs), Isola 370HR proves to be a dependable material that keeps signal integrity in check and ensures dimensional stability across stacked layers. As electronic designs get tighter and more compact, having materials that can handle dense, multi-layered setups without missing a beat becomes increasingly necessary.
Why Choose Isola 370HR for Multilayer Circuit Boards-
●Stable Interconnectivity Between Layers: As multilayer designs require reliable connections between layers, Isola 370HR’s low Dk and Df values minimize signal loss. These properties ensure the signal integrity remains intact, which is especially beneficial for high-frequency applications.
●Support for Advanced Designs: Isola 370HR is a trusted material when designing High-Density Interconnects (HDI). It supports intricate, compact circuit designs where minimal signal degradation is required between the layers of the board.
Thanks to its mechanical properties, Isola 370HR guarantees that the PCB remains stable across multiple layers, maintaining the integrity of the design throughout its operational life. This makes it an excellent choice for applications requiring tight tolerances and precise layer-to-layer connections.
Thermal, Electrical & Mechanical Performance of Isola 370HR PCB Laminate
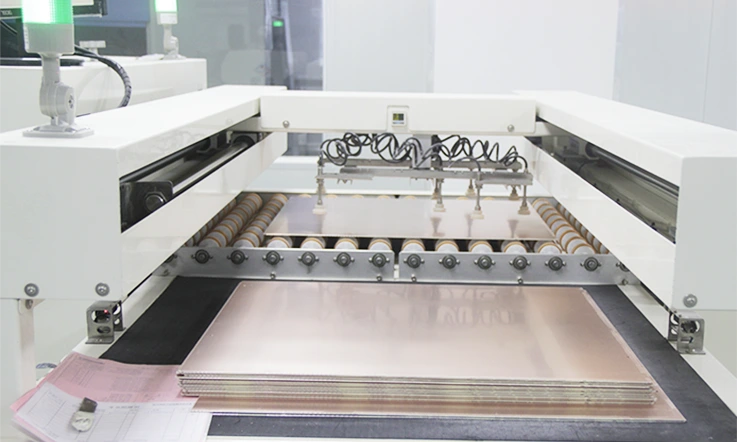
When working with Isola 370HR PCB laminate, getting a handle on its thermal, electrical, and mechanical properties is core to picking the right material for advanced multilayer circuit boards. Isola 370HR holds its own in high-frequency applications, stands up to thermal cycling, and packs solid mechanical strength, making it a solid pick for high-performance electronics.
In this section, we’ll dive into how this laminate handles temperature extremes, ensures signal integrity even in challenging conditions, and maintains structural stability throughout its use.
High-Tg and Thermal Stability in Isola 370HR PCB Laminate
The glass transition temperature (Tg) of Isola 370HR is rated at 180°C, making it a solid performer in applications where high heat exposure is a concern. Tg refers to the temperature at which the material changes from a rigid, glassy state to a more flexible, rubbery state. Materials with higher Tg values are better suited to withstand thermal stress without suffering from performance degradation.
Why Does Thermal Stability Matter?
●High-Temperature Applications: For 5G networks, automotive electronics, and power electronics, components often operate in environments where temperature fluctuation is frequent. A laminate like Isola 370HR that stands firm against softening or warping in these conditions helps keep your PCBs in top shape for the long haul.
●Thermal Cycling Resistance: Isola 370HR can power through countless thermal cycles without bending out of shape or losing its strength. This toughness cuts down the chances of PCB failure caused by thermal expansion or contraction, making it a solid choice for automotive systems and high-end telecom applications.
Dielectric Constant (Dk) and Signal Integrity in High-Frequency Applications
In high-frequency applications, keeping signal integrity on point is a must. Isola 370HR boasts a low dielectric constant (Dk), helping to keep signal loss in check as it moves across the PCB. Dk measures how well a material stores electrical energy in an electric field, and a lower Dk means your signal stays crisp and steady.
How Does Low Dk Affect Signal Integrity?
●Reduced Signal Degradation: As signal frequencies rise, signal attenuation becomes more pronounced. Isola 370HR’s low Dk allows for better signal transmission without distortion, ensuring that your high-speed signals arrive at their destination without unnecessary degradation.
●Ideal for RF and Microwave Circuits: For designs like RF and microwave circuits, where keeping signals clean is a top priority, Isola 370HR minimizes loss, making sure transmissions stay sharp and intact across long distances and multiple layers.
●Maintaining Performance at High Frequencies: Whether you’re working with 5G technologies, automotive radar systems, or high-speed digital applications, Isola 370HR’s low Dk ensures your circuits function at peak performance. This means faster, more efficient systems that don’t suffer from unexpected drops in performance due to poor signal quality.
Mechanical Strength & CAF Resistance in Isola 370HR PCB Laminate
When it comes to multilayer circuit boards, ensuring that your PCB stays intact under mechanical stress is a must. Isola 370HR provides exceptional mechanical strength and resistance to conductive anodic filament (CAF) formation, which can lead to PCB failure. This is achieved through its unique formulation that enhances the laminate’s resistance to both thermal and mechanical stress.
What Makes Isola 370HR Strong?
●High Mechanical Strength: With glass-reinforced layers, Isola 370HR offers excellent rigidity, making it less prone to warping or deformation during manufacturing or under long-term use. This durability comes in handy when building complex circuit boards packed with multiple layers and components.
●CAF Resistance: CAF is a common failure mode in PCBs, where current leakage occurs through anodic filaments that form between traces. Isola 370HR’s formulation has been specifically designed to resist this phenomenon, ensuring the reliability of the PCB even under conditions that would normally cause failure with other materials.
●Longevity and Reliability: With Isola 370HR, you get a material that holds its own over time. Whether it’s thermal cycling, mechanical impact, or electrical stress, Isola 370HR maintains its structural integrity and electrical performance, making it a suitable choice for automotive, aerospace, and medical electronics that demand long-lasting performance.
Isola 370HR PCB Laminate vs Other High-Performance Materials
When choosing the right PCB laminate, we often weigh multiple factors—thermal reliability, signal integrity, mechanical strength, and processing compatibility. Among the widely used options, Isola 370HR, FR406, IT180A, and PCL-FRP 370HR all offer different advantages depending on the application. But which one best fits high-frequency circuits, high-layer count designs, and rugged environments?
To help PCB manufacturers and designers make an informed decision, let’s take a detailed look at how Isola 370HR PCB laminate stacks up against FR406, IT180A, and PCL-FRP 370HR, focusing on their dielectric properties, thermal stability, and manufacturability.
Isola 370HR PCB Laminate vs FR406 – Which is Better for High-Reliability Applications?
Both Isola 370HR and FR406 are well-known materials in the high-performance PCB industry. While both are widely used for multilayer boards, Isola 370HR stands out with its higher Tg (180°C) and superior thermal performance, making it better suited for applications requiring long-term reliability under extreme conditions.
Key Differences Between Isola 370HR and FR406-
Property | Isola 370HR | FR406 |
Tg (Glass Transition Temperature, °C) | 180 | 170 |
Dielectric Constant (Dk) @ 1GHz | 3.15 | 4.25 |
Thermal Conductivity (W/mK) | 0.60 | 0.45 |
CTE (Z-Axis, ppm/°C) | 45 | 55 |
CAF Resistance | High | Medium |
What This Means for Manufacturers-
If you’re designing PCBs for high-temperature environments or boards that go through multiple reflow cycles, Isola 370HR is the safer bet. It reduces delamination risks and ensures a longer operational lifespan compared to FR406.
Isola 370HR PCB Laminate vs IT180A – Best Choice for High-Frequency PCBs?
For high-speed digital and RF applications, a low dielectric constant (Dk) and low dissipation factor (Df) make all the difference. Both Isola 370HR and IT180A are solid options, each bringing its own strengths to the table depending on the project’s needs.
Comparing Electrical & Thermal Properties-
Property | Isola 370HR | IT180A |
Tg (°C) | 180 | 175 |
Dk @ 1GHz | 3.15 | 3.66 |
Df @ 1GHz | 0.009 | 0.012 |
CTE (Z-Axis, ppm/°C) | 45 | 50 |
Moisture Absorption (%) | 0.1 | 0.15 |
Best Use Cases-
●Isola 370HR: Ideal for high-frequency, high-speed data transmission, thanks to its lower Dk and Df, which help minimize signal loss.
●IT180A: Suitable for cost-sensitive applications that require good thermal stability, but may not be the best for RF and microwave circuits due to higher Dk/Df values.
Isola 370HR PCB Laminate vs PCL-FRP 370HR – Which Offers Superior Performance?
For main applications such as aerospace, defense, and high-density interconnect (HDI) PCBs, materials must handle extreme stress. Isola 370HR and PCL-FRP 370HR are two laminates often considered for these demanding designs. While both have high Tg and great mechanical strength, they differ in terms of manufacturing flexibility and durability.
Mechanical & Thermal Performance Comparison-
Property | Isola 370HR | PCL-FRP 370HR |
Tg (°C) | 180 | 185 |
Flexural Strength (MPa) | 580 | 560 |
Thermal Conductivity (W/mK) | 0.60 | 0.58 |
CTE (Z-Axis, ppm/°C) | 45 | 48 |
Peel Strength (N/mm) | 1.10 | 1.05 |
What This Means for Your Application-
●Isola 370HR provides better flexibility for complex multilayer designs.
●PCL-FRP 370HR offers slightly higher thermal resistance, but may not be as easy to process during drilling and etching.
Making the Right Choice-
If you’re building high-density, high-layer count PCBs, Isola 370HR will give you a smoother fabrication experience with fewer complications in layer bonding and processing.
Isola 370HR PCB Laminate in Advanced Manufacturing & Fabrication
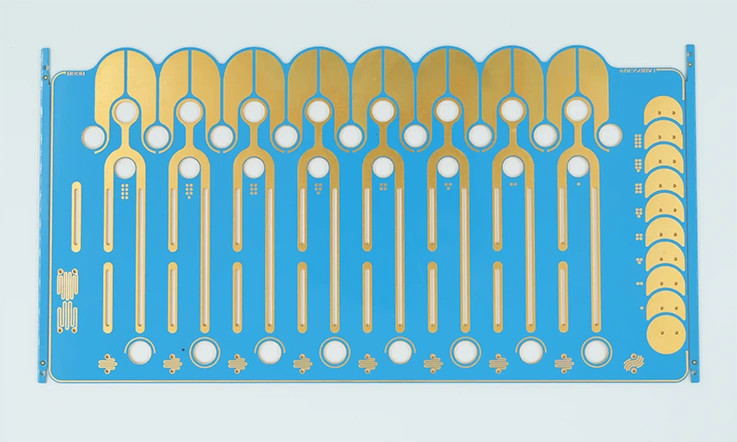
In the world of advanced PCB manufacturing and fabrication, Isola 370HR PCB laminate is quickly becoming a top choice for human. Its high-performance properties make it a standout material for multilayer PCB stack-ups, surface finishes, and other fabrication processes. Therefore, if you’re designing a high-speed communications device or a military-grade application, Isola 370HR provides the mechanical, electrical, and thermal reliability needed for high-density interconnects.
When moving through the PCB fabrication process, understanding the compatibility of Isola 370HR with various manufacturing steps will ensure efficient production. Let’s take a closer look at the specific steps involved in fabricating PCBs using Isola 370HR, and how its unique properties support each phase.
Multilayer PCB Stack-Up Design with Isola 370HR PCB Laminate
Isola 370HR PCB laminate is particularly well-suited for multilayer PCB stack-ups, a core feature in high-performance circuits. Designing these stack-ups requires careful consideration of thermal expansion, layer bonding, and signal integrity, all of which are influenced by the materials used in the construction. Isola 370HR, with its high Tg of 180°C, offers superb dimensional stability during the stack-up process, ensuring that the layers remain intact even in extreme conditions.
Key Design Considerations-
When creating a multilayer stack-up using Isola 370HR, it’s important to:
●Maintain uniformity in the layer buildup: This ensures consistent performance across the layers, especially for high-frequency applications.
●Optimize thermal conductivity: The high thermal stability of Isola 370HR minimizes the risk of thermal stress between layers, maintaining long-term reliability.
●Minimize electrical noise: The low Dk of Isola 370HR helps cut down on interference, making it a strong contender for signal-sensitive designs like 5G communication systems.
Layer | Material | Tg (°C) | Dk (Dielectric Constant) | Thermal Conductivity |
Layer 1 | Isola 370HR | 180 | 3.15 | 0.60 W/mK |
Layer 2 | Copper | N/A | N/A | 400 W/mK |
Layer 3 | Isola 370HR | 180 | 3.15 | 0.60 W/mK |
This table shows how Isola 370HR stacks up when used in a multilayer PCB, and how the thermal conductivity, Tg, and Dk influence the final performance of your design.
Surface Finishes Compatible with Isola 370HR PCB Laminate
The surface finish you choose has a big impact on the performance of Isola 370HR PCB laminate, especially in multilayer PCBs for high-speed electronics. Whether it’s gold, ENIG (Electroless Nickel Immersion Gold), or immersion silver, pairing the right finish with the laminate is main factors to ensuring both longevity and top-notch performance. Isola 370HR is designed to bond seamlessly with various finishes, offering flexibility in PCB fabrication.
Common Surface Finishes for Isola 370HR-
●ENIG (Electroless Nickel Immersion Gold): Popular for its reliable electrical performance and excellent corrosion resistance, ENIG pairs well with Isola 370HR for high-frequency applications.
●Immersion Silver: For low-cost applications, immersion silver offers good solderability and excellent thermal properties when used with Isola 370HR.
Surface Finish | Corrosion Resistance | Solderability | Compatibility with Isola 370HR |
ENIG | Excellent | High | Excellent |
Immersion Silver | Good | Very High | Very Good |
HASL | Good | Moderate | Good |
This table helps visualize the performance relationship between Isola 370HR and common surface finishes, guiding the selection process for your PCB fabrication needs.
Drilling, Etching & Assembly Considerations for Isola 370HR PCB Laminate
When working with Isola 370HR PCB laminate, drilling, etching, and assembly are main processes that require specific considerations. Due to its high Tg and mechanical properties, Isola 370HR maintains its structural integrity during these processes, which can sometimes be challenging with other materials. Ensuring compatibility with drilling tools and etching solutions will streamline the PCB fabrication process, leading to a smoother assembly phase.
Drilling Considerations-
●Tool Wear: Isola 370HR is designed to withstand the stress of high-speed drilling, but using the right tools will extend tool life and ensure precision. Diamond-coated drills are typically recommended to maintain sharpness and efficiency.
Etching Considerations-
●Chemical Compatibility: During etching, Isola 370HR interacts well with acidic etching solutions, providing precise copper traces without damaging the laminate. The etching process must be carefully controlled to avoid undercutting, especially around tight-pitch components.
Assembly Considerations-
●Soldering Compatibility: Isola 370HR works seamlessly with both wave soldering and hand soldering techniques. However, it is recommended to monitor the soldering temperature to ensure the integrity of the laminate is maintained.
Process | Considerations | Recommendation |
Drilling | Requires high-speed tools and precise drills | Use diamond-coated drills |
Etching | Compatible with acidic etching solutions | Control etching time |
Soldering | Works with wave and hand soldering techniques | Maintain proper soldering temps |
This table outlines the most important assembly and fabrication considerations when working with Isola 370HR, ensuring that you can take full advantage of its mechanical stability and high thermal performance.
Advanced Processing Techniques for Isola 370HR PCB Laminate
Manufacturers working with Isola 370HR PCB laminate often look for ways to enhance yield, improve layer bonding, and streamline fabrication processes. Given its high-Tg properties, low Z-axis expansion, and outstanding CAF resistance, this material is widely used in high-layer count PCBs, RF applications, and mixed-material designs.
But to get the most out of Isola 370HR, processing techniques must be fine-tuned. From sequential lamination to hybrid fabrication strategies and resin flow control, each step plays a part in ensuring flawless production. Let’s break it all down and explore how we can optimize fabrication techniques for Isola 370HR.
Sequential Lamination Strategies for Isola 370HR PCB Laminate
As PCB designs push towards higher layer counts and finer features, sequential lamination has become a go-to method. With Isola 370HR, managing the lamination sequence correctly prevents defects, minimizes resin starvation, and ensures even copper distribution.
Best Practices for Sequential Lamination with Isola 370HR-
Factor | Best Practice |
Prepreg Thickness | Use a controlled prepreg stack-up to ensure even resin distribution. |
Press Cycle Optimization | Multi-stage press cycles help prevent voids and delamination. |
Pressure Application | Gradual pressure ramp-up minimizes stress on inner layers. |
Heat Control | Uniform heating prevents resin flow inconsistencies. |
Defoiling Techniques | Proper defoiling ensures good copper adhesion in sequential builds. |
Why It Matters-
Applying optimized lamination cycles keeps thermal stress under control and prevents layer misalignment, which is especially useful for HDI boards and high-speed designs.
Hybrid PCB Fabrication Using Isola 370HR PCB Laminate
With multifunctional PCBs becoming more common, mixing different laminate types within a single stack-up is a frequent challenge. Isola 370HR integrates well with various RF, high-speed, and high-temperature laminates, but we must address material compatibility issues like CTE mismatches and press cycle differences.
Material Pairing Considerations in Hybrid Stack-Ups-
Material Type | Compatibility with Isola 370HR | Challenges |
PTFE-based RF laminates | Compatible with proper bonding films. | Different CTEs require stress compensation. |
Polyimide substrates | Works well for high-temp applications. | Press cycle tuning needed to match cure profiles. |
Metal Core PCBs (MCPCB) | Usable with proper thermal interface layers. | Resin adhesion may require surface treatments. |
What Fabricators Need to Watch For:
●Layer expansion mismatches can cause delamination—always validate CTE differences.
●Copper roughness effects impact signal integrity—surface prep methods must be fine-tuned.
●Hybrid pressing cycles may require multiple heating stages to balance resin flow.
Optimizing Resin Flow & Adhesion in Isola 370HR PCB Laminate
Proper resin flow management ensures consistent mechanical properties, strong interlayer bonds, and uniform dielectric performance. Since Isola 370HR has a higher resin content than standard FR-4 materials, controlling flow during lamination prevents voids, dry areas, and excessive squeeze-out.
Resin Flow Optimization Tips-
Process Parameter | Optimization Strategy |
Prepreg Selection | Use appropriate resin content based on the board’s copper density. |
Press Pressure & Timing | Gradual pressure application prevents excessive squeeze-out. |
Heat Ramp-Up Rate | Controlled heating ensures uniform resin softening. |
Vacuum Lamination | Removes air pockets and reduces void formation. |
Bonding Enhancements | Use plasma or chemical treatments to enhance adhesion. |
Common Pitfalls & Fixes:
●Too much resin flow? → Reduce press pressure or adjust prepreg thickness.
●Insufficient adhesion? → Try plasma etching or double-pass oxide treatment.
●Void formation? → Switch to vacuum-assisted lamination for better air removal.
When done right, resin control leads to stronger, more durable PCBs with fewer manufacturing headaches.
Signal Integrity & High-Speed Design Optimization with Isola 370HR PCB Laminate
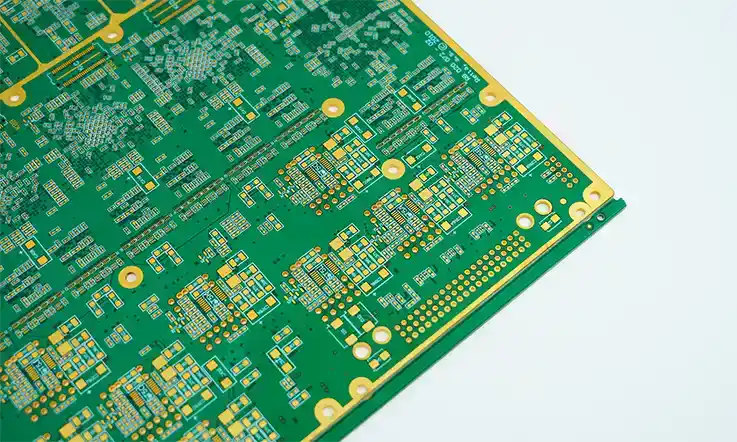
In high-speed PCB design, maintaining signal integrity is a fundamental requirement to ensure stable and efficient data transmission. Isola 370HR PCB laminate, known for its low-loss characteristics and high thermal reliability, provides a solid foundation for RF, microwave, and high-frequency applications. Proper circuit layout, impedance control, and crosstalk management can significantly enhance overall system performance.
Dielectric Properties of Isola 370HR PCB Laminate for RF Designs
The dielectric properties of Isola 370HR PCB laminate make it well-suited for RF applications. Its stable dielectric constant (Dk) ensures consistent signal transmission, while its low dissipation factor (Df) helps minimize signal loss. When compared to other high-performance PCB materials such as Rogers PCB, Taconic PCB, and Arlon PCB, Isola 370HR stands out in terms of manufacturing compatibility and cost efficiency.
PCB Material | Dielectric Constant (Dk) | Dissipation Factor (Df) | Frequency Range |
Isola 370HR | 4.04 @ 1GHz | 0.022 | Up to 10GHz |
Rogers 4350B | 3.48 @ 10GHz | 0.0037 | Up to 40GHz |
Taconic TLY-5 | 2.20 @ 10GHz | 0.0019 | Up to 20GHz |
Arlon 85N | 4.10 @ 1GHz | 0.015 | Up to 12GHz |
Compared to Teflon-based laminates with extremely low Dk values, Isola 370HR provides a balance of signal performance and manufacturing compatibility. It is a better choice for multilayer RF designs requiring high stability without excessive processing challenges.
PCB Layout Considerations to Reduce Signal Loss in Isola 370HR PCB Laminate
To achieve optimal performance in high-speed designs, proper PCB layout techniques must be implemented. Isola 370HR allows us to optimize signal integrity through careful stack-up design and controlled trace routing. Key strategies include:
●Minimizing Trace Lengths: Shorter signal paths reduce parasitic inductance and capacitance, improving signal quality.
●Optimizing Reference Planes: Continuous ground planes should be placed beneath critical signal traces to maintain impedance consistency.
●Selecting Appropriate Dielectric Thickness: Controlling layer spacing ensures impedance matching and reduces crosstalk.
●Reducing Via Count: Minimizing unnecessary vias prevents signal reflections and discontinuities.
By carefully selecting dielectric thickness and copper weights, Isola 370HR enables high-density interconnect (HDI) designs without compromising electrical performance.
Impedance Matching & Crosstalk Prevention in High-Speed Circuits
In high-frequency circuits, impedance matching directly affects signal stability, while crosstalk can degrade performance. Isola 370HR PCB laminate supports precise impedance control, helping us maintain signal integrity in complex designs.
Parameter | Effect on Signal Integrity | Best Practices |
Impedance Mismatch | Causes reflections & ringing | Use controlled impedance traces |
High Crosstalk | Leads to noise & distortion | Increase trace spacing & add shielding |
Uneven Dielectric Constant | Results in inconsistent propagation | Use stable laminates like Isola 370HR |
For precise impedance matching, we should optimize trace width and spacing according to the stack-up structure. For instance, a 50Ω signal trace must be carefully designed considering dielectric thickness and copper weight. Similarly, differential pair routing (e.g., 90Ω or 100Ω differential pairs) should be implemented to minimize reflections and improve overall signal transmission.
Reliability Testing & Failure Analysis for Isola 370HR PCB Laminate
Ensuring long-term performance and durability is a top priority in PCB manufacturing, especially for applications requiring high reliability. Isola 370HR PCB laminate undergoes rigorous testing to assess its resistance to electrical and mechanical stress, ensuring it meets the stringent demands of aerospace, telecommunications, and high-performance computing. This section explores key reliability tests, failure modes, and best practices for optimizing PCB lifespan.
Conductive Anodic Filament (CAF) Resistance Testing for Isola 370HR PCB Laminate
CAF formation is a failure mechanism that can lead to electrical shorts between PCB conductors, particularly in high-density designs. To evaluate CAF resistance, Isola 370HR undergoes accelerated stress testing under high humidity and voltage bias conditions.
Test Parameter | Isola 370HR Performance | Industry Standard |
Humidity Level | 85% RH @ 85°C | 85% RH @ 85°C |
Voltage Bias | 100V | 50V – 100V |
Time to Failure (TTF) | >1000 hours | 500 – 1000 hours |
The combination of a highly engineered resin system and enhanced glass weave structure reduces the risk of ion migration, preventing CAF-related failures even in harsh environments. To further improve reliability, we should optimize via spacing and use high-Tg materials in multilayer PCBs.
Thermal Cycling & Solder Joint Durability in Isola 370HR PCB Laminate
Thermal cycling subjects PCBs to repeated heating and cooling, mimicking real-world operating conditions. Solder joints and laminate materials must withstand expansion and contraction to prevent cracking, delamination, or pad lifting.
Test Cycle | Temperature Range | Number of Cycles | Pass/Fail Criteria |
IPC-TM-650 | -40°C to 125°C | 1000 cycles | No cracks, no delamination |
JEDEC JESD22-A104 | -55°C to 150°C | 2000 cycles | Less than 5% failure rate |
Isola 370HR demonstrates outstanding thermal stability, minimizing stress on solder joints and vias. For improved durability, we can use optimized pad geometries and select lead-free solder alloys with compatible expansion coefficients.
PCB Warpage Control & Dimensional Stability of Isola 370HR PCB Laminate
Warpage and dimensional shifts can affect PCB assembly accuracy, leading to misalignment and solder defects. Isola 370HR features a low coefficient of thermal expansion (CTE) and robust glass transition properties, ensuring stable performance across temperature fluctuations.
Property | Isola 370HR | Standard FR-4 |
Tg (Glass Transition Temp) | 180°C | 130°C |
CTE (Z-Axis) | 50 ppm/°C | 70 ppm/°C |
Dimensional Stability | <0.05% | 0.1% – 0.2% |
By implementing symmetrical stack-up designs and pre-baking laminates before assembly, we can further mitigate warpage, ensuring precision in high-layer-count PCBs.
Integrating Isola 370HR PCB Laminate with Next-Gen PCB Technologies
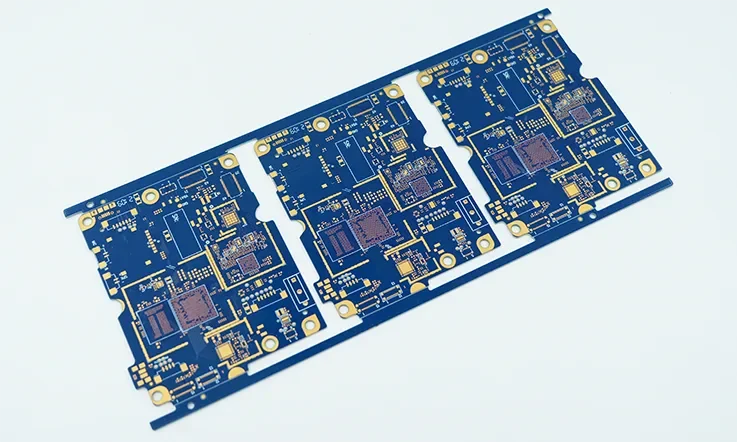
As electronic devices become more complex, PCB technology must keep pace with evolving demands in miniaturization, signal integrity, and durability. Isola 370HR PCB laminate stands out in advanced fabrication methods, enabling us to push the boundaries of high-density interconnect (HDI) design, rigid-flex applications, and embedded component integration. This section explores how this laminate enhances next-generation PCB technologies, ensuring top-tier performance across various industries.
HDI (High-Density Interconnect) PCB Manufacturing Using Isola 370HR PCB Laminate
HDI PCBs require materials that can handle multiple lamination cycles, fine-pitch microvias, and precise impedance control. Isola 370HR meets these demands with its high glass transition temperature (Tg), low Z-axis expansion, and excellent laser-drilling compatibility.
Property | Isola 370HR | Standard FR-4 | Benefit for HDI |
Tg (Glass Transition) | 180°C | 130°C | Reduces warpage in multilayers |
Z-Axis CTE (50-260°C) | 50 ppm/°C | 70 ppm/°C | Prevents via cracking |
Dielectric Constant (Dk) @ 10GHz | 4.04 | 4.5-4.8 | Enhances signal integrity |
We leveraging Isola 370HR for HDI fabrication can expect enhanced drill reliability, lower signal loss, and improved registration accuracy for multi-layer boards. As electronics continue to shrink in size, this laminate supports advanced features like stacked microvias and finer line spacing without compromising durability.
Rigid-Flex PCB Applications in Aerospace & Medical Using Isola 370HR PCB Laminate
Aerospace and medical electronics require lightweight, compact, and high-reliability PCBs. Rigid-flex technology enables flexible circuit sections to connect rigid boards, reducing connectors and improving shock resistance. Isola 370HR integrates seamlessly with polyimide flex layers, offering a robust hybrid PCB solution.
Application | Challenges | Isola 370HR Advantage |
Aerospace Avionics | Vibration & temperature extremes | Thermal stability & low moisture absorption |
Medical Wearables | Miniaturization & durability | HDI compatibility & flex-rigid bonding |
Defense Systems | Electromagnetic interference (EMI) | Stable Dk/Df & high-frequency performance |
By incorporating Isola 370HR into rigid-flex designs, we can develop PCBs with enhanced reliability, lighter weight, and greater mechanical resilience—an excellent choice for core applications.
Embedded Component Technologies & Isola 370HR PCB Laminate
Embedding passive and active components within a PCB substrate improves electrical performance while saving board space. Isola 370HR is well-suited for this advanced technique due to its uniform dielectric properties and excellent thermal stability.
Embedded Technology | Advantage with Isola 370HR |
Buried Resistors | Low-loss dielectric ensures accuracy |
Embedded Capacitors | Stable capacitance for noise reduction |
Integrated Power Modules | Improved heat dissipation & reliability |
We looking to boost PCB efficiency can utilize Isola 370HR for embedded component technology, streamlining circuit design and reducing the need for surface-mount components. This method enhances signal integrity, improves thermal performance, and simplifies assembly.
FAQ & Isola 370HR PCB Laminate
1.What thickness options are available for Isola 370HR?
Ranges from 0.002” (0.05mm) to 0.125” (3.18mm), depending on copper foil type and PCB design.
2.Is Isola 370HR suitable for high-voltage PCBs?
Yes, with dielectric strength over 40 kV/mm, ideal for power electronics.
3.Can Isola 370HR handle automotive temperature fluctuations?
Yes, it maintains stability under extreme conditions, making it suitable for ECUs and ADAS.
4.What prepregs work with Isola 370HR?
Compatible with Isola 370HR prepreg and similar high-Tg FR-4 materials.
5.Does it need special surface treatment before plating?
No, but proper cleaning and desmearing ensure strong copper adhesion.
6.Can Isola 370HR be used in flexible PCBs?
No, but it works in rigid-flex designs for the rigid sections.
7.How does Isola 370HR compare to ceramic laminates for RF?
More cost-effective, but ceramic materials offer lower dielectric loss for ultra-high frequencies.