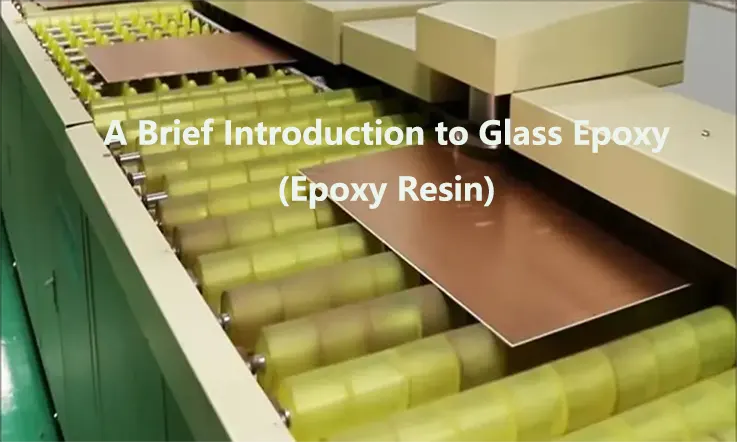
Glass-epoxy composites are an exceptional material solution that provides superior thermal and electrical insulation properties, making them an ideal choice for electronic manufacturing. This material offers exceptional resistance to high temperatures, dimensional stability, and mechanical strength, thereby ensuring that products remain durable and reliable. In addition to its desirable performance characteristics, the combustibility of glass-epoxy composites can be controlled expertly, further bolstering their safety and reliability in electronic devices.
For these reasons, glass-epoxy composites are frequently used in PCB and electronic manufacturing when high-performance and dependable thermal and electrical insulation properties are required.
In this article, we will discuss the properties, manufacturing process, advantages and disadvantages, and applications of glass epoxy.
What Is Glass Epoxy and How Is It Used in PCBs ?
Glass epoxy, also known as FR-4 (flame retardant 4), is a type of composite material made of woven fiberglass cloth and an epoxy resin binder. It’s commonly used as a substrate material for printed circuit boards (PCBs) due to its high tensile strength, low thermal expansion coefficient, electrical insulating properties, and flame-retardant nature.
In PCBs, Glass Epoxy is used as the base material for the board and is laminated with copper foil layers, which are etched to create a circuit pattern. The copper acts as the conductive pathway, and the Glass Epoxy provides the mechanical support and insulation for the circuit. The combination of the two materials results in a stable and reliable PCB, capable of withstanding harsh operating environments.
Types and Properties of Glass Epoxy Materials
There are several types of glass epoxy materials used in PCBs. Some of the most common types include:
FR-4: This is the most widely used type of glass epoxy material in PCBs and is made from woven fiberglass and an epoxy resin. It is known for its high strength, dimensional stability, and resistance to moisture and chemicals.
FR-2: This type of epoxy material is made from paper and resin instead of fiberglass. It is less expensive than FR-4 and is commonly used in low-cost consumer electronics.
FR-3: Also known as CEM-1 (Composite Epoxy Material), this type of epoxy material is made from a blend of woven fiberglass and cellulose paper.
The properties of glass epoxy materials vary depending on the specific formulation and type of reinforcing fibers used. Generally, glass epoxy materials have high strength, low dielectric constant, low dissipation factor, and high thermal stability. They are also resistant to moisture, chemicals, and high temperatures, making them ideal for use in high-reliability electronic applications such as PCBs.
Benefits and Drawbacks of Using Glass Epoxy in PCBs
Benefits of using Glass Epoxy in PCBs include:
● High mechanical strength: Glass Epoxy has a high tensile strength to weight ratio which makes it a robust and durable material for PCB applications.
● Excellent electrical insulation: Glass Epoxy has excellent electrical insulation properties which make it a great choice for PCB substrates, where electrical isolation is critical.
● High thermal resistance: Glass Epoxy has a low thermal expansion coefficient, making it ideal for components that generate heat. It has a high glass transition temperature, enabling it to withstand high temperatures without losing its mechanical integrity.
● Flame retardant: Glass Epoxy is a self-extinguishing material, making it an ideal substrate material for PCBs operating in environments with a high risk of fire.
Drawbacks of using Glass Epoxy in PCBs include:
● High dielectric constant: The high dielectric constant of Glass Epoxy may reduce the high-frequency performance of PCBs.
● Poor moisture resistance: Glass Epoxy can be sensitive to moisture absorption, which can degrade its electrical properties over time.
● Manufacturing limitations: Glass Epoxy can be challenging to process and manufacture, requiring specialized techniques and equipment.
● Higher cost: Glass Epoxy is typically more expensive than other PCB substrate materials, which can make it less cost-effective for some applications.
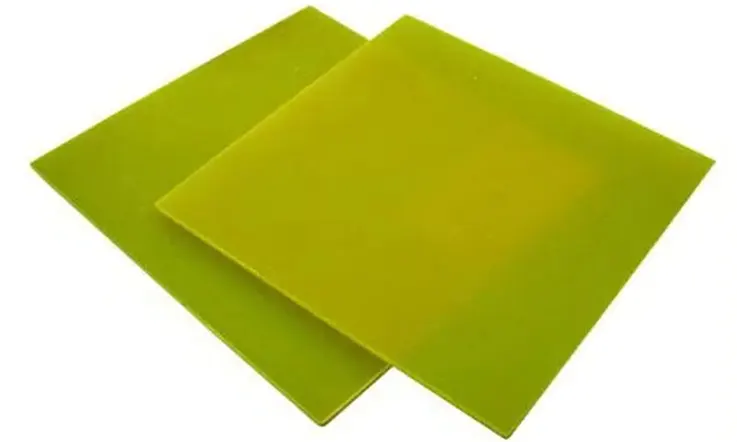
Properties of Glass Epoxy and How to Affect PCB Design
The properties of Glass Epoxy directly affect PCB design as it determines the performance, reliability, and manufacturability of the circuit board. Some important properties of Glass Epoxy in relation to PCB design are:
● Dielectric constant: Glass Epoxy has a relatively high dielectric constant, which can affect the signal integrity and cause undesirable crosstalk between adjacent signal traces. PCB designs must account for this parameter to minimize signal interference.
● Thermal expansion coefficient: Glass Epoxy has a low thermal expansion coefficient, which makes it less prone to thermal stress. This factor must be considered when designing PCBs for applications with significant temperature variation.
● Tensile strength: Glass Epoxy has a high tensile strength, which makes PCBs more robust and durable. PCB designers can take advantage of this trait by designing thinner, lighter PCBs with high mechanical stability.
● Moisture absorption: Glass Epoxy can absorb moisture that can affect the dielectric properties of the PCB material and lead to reliability issues.
● Flame retardancy: Glass Epoxy is flame retardant, making it an ideal material for PCBs used in high-risk environments prone to fire. PCB designs should incorporate additional safety features to further reduce the risk of fire.
PCB Substrate Materials: Why Glass Epoxy is the Preferred Choice
PCB substrate materials must have good insulating properties, high mechanical strength, low thermal expansion coefficient, and be able to withstand high temperatures, humidity, and corrosive environments. Glass Epoxy is the preferred choice as it is a type of reinforced plastic material that offers a high degree of dielectric strength, excellent dimensional stability, and good thermal and chemical resistance.
Additionally, Glass Epoxy has a low dielectric constant and loss factor, making it ideal for high-frequency circuit applications. These properties make Glass Epoxy the preferred substrate material for PCB production in different electronic industries.
Manufacturing Process for Glass Epoxy PCBs
● Panel preparation: The Glass Epoxy substrate material is cut to the required size and shape. The panels are then cleaned and prepared for lamination by removing any contaminants present on the surface.
● Copper foil lamination: Copper foils are laminated onto the Glass Epoxy substrate using a heat and pressure process called hot press lamination. The copper foil circuit patterns are created using photoresist and etching.
● Drilling: Holes are drilled into the PCB panels for component insertion and copper plating. Automated drilling machines are used to drill precise holes at predefined locations.
● Electroless copper plating: The drilled holes are electrolessly plated with copper to provide the required electrical connectivity between layers of the PCB.
● Outer layer etching: The outer layer copper is etched away to define the final circuit pattern using photolithography and etching techniques.
● Solder mask application: A solder mask is applied to the PCB surface to protect the circuit traces from oxidation and contamination and to facilitate component assembly.
● Surface finish: The PCB surface is finished with a layer of a suitable metal such as gold, silver, or tin to provide a protective coating, improve solderability, and ensure reliable electrical connectivity.
● Testing and inspection: PCBs are inspected using automated optical inspection and electrical testing equipment to identify any manufacturing defects and verify their performance.
Glass Epoxy PCBs require specialized manufacturing techniques due to the material’s unique properties, including high mechanical strength, thermal resistance, and electrical insulation capabilities. PCB manufacturers must use appropriate equipment, such as laminating machines and drillers, and follow stringent quality control measures to ensure that the final product meets the desired specifications and performance requirements.
Tips and Best Practices for Designing and Working with Glass Epoxy PCBs
Some tips and best practices for designing and working with Glass Epoxy PCBs include:
● Proper handling and storage: Glass Epoxy should be stored in a dry environment to prevent moisture absorption, which can affect its properties. When handling, avoid bending or dropping the material to prevent cracking or damage.
● Design for manufacturability: During the design stage, consider the manufacturing process and the limitations of Glass Epoxy. Ensure the board layout is optimized for efficient trace routing and allow adequate spacing between components to avoid unintended shorts.
● Thermal management: When designing with Glass Epoxy, consider the thermal conductivity properties of the material to help dissipate heat. Thermal vias can be incorporated to improve heat dissipation.
● Avoid crevices and sharp corners: Sharp corners, creases or uneven surfaces on Glass Epoxy can trap air and moisture, a potential cause of delamination, or poor soldering quality. Avoid them when designing and fabricating a PCB.
● Choose appropriate surface finish: The choice of surface finish on the copper and component leads can impact the soldering process’s reliability. Select a suitable finish that can provide good solderability, protect the copper, and withstand the environment.
● Test and inspect: Thoroughly test and inspect PCBs during and after the manufacturing process to detect any defects or issues that may affect their functionality or reliability.
By following these tips and best practices, designers and manufacturers can maximize Glass Epoxy PCBs’ performance, reliability, and longevity.
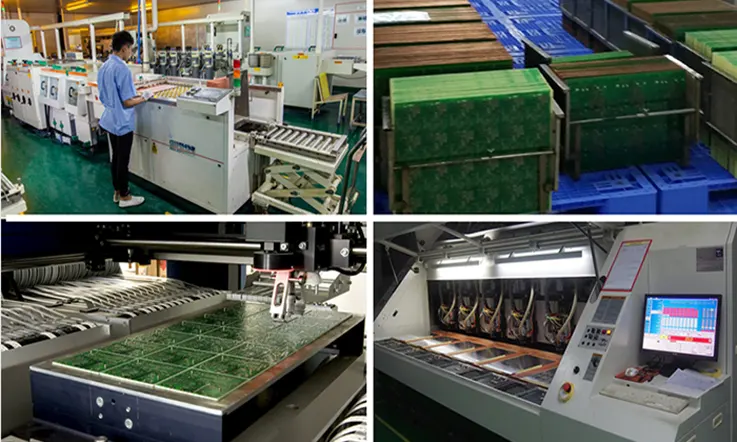
Examples and Case Studies of Glass Epoxy PCB Applications
Glass Epoxy PCBs are widely used in various electronic applications, including but not limited to:
● Computing and data processing equipment: High-performance computing and data processing systems require reliable and durable PCBs made from Glass Epoxy materials to withstand the rigors of continuous operation.
● Automotive electronics: Glass Epoxy PCBs are used in automotive electronics, where high-temperature stability, mechanical strength, and durability are vital for harsh automotive environments.
● Aerospace and defense applications: Glass Epoxy PCBs are used in aerospace and defense applications due to their high thermal resistance, mechanical strength, and flame-retardant properties.
● Industrial equipment: High-voltage power supplies, motor controllers, and other industrial equipment require PCBs made from Glass Epoxy materials to provide adequate insulation, reliability, and durability.
● Consumer electronics: Mobile devices, audio equipment, and other consumer electronics require PCBs made from Glass Epoxy materials to meet the design requirements such as thin profile, high-density circuitry, and durability.
One case study of Glass Epoxy PCB application is its use in LED lighting technology. Glass Epoxy PCBs provide the high thermal conductivity needed to dissipate heat efficiently, enabling LEDs to operate at a higher power density more effectively. This results in brighter, more energy-efficient LED lighting fixtures.
Another example is in the Medical device industry. Glass Epoxy PCBs are useful in implantable and wearable medical devices that must be able to withstand environmental and temperature changes, have high mechanical strength, build tolerance to radiation, and be biocompatible with human tissues.
Overall, Glass Epoxy PCBs can be used in various applications where high-temperature, high mechanical strength, and high reliability are required, and these properties make it ideal for use in mission-critical environments.
Trends in Glass Epoxy PCB Technology
● Increased use of Glass Epoxy PCBs in high-frequency applications: As demand grows for high-speed data transmission, Glass Epoxy PCBs will be capable of meeting the frequency requirements, and digital systems will benefit from utilizing the material.
● Improved thermal conductivity: Research is underway to improve the thermal conductivity of Glass Epoxy PCBs, which would enable more effective cooling solutions for electronic devices.
● Development of new laminates: Manufacturers are exploring new methods of creating Glass Epoxy laminates, such as using advanced resins, fibers, and adhesives, to improve mechanical strength and reduce costs.
● Advancements in the manufacturing process: Continued advances in PCB manufacturing technology will make it easier and more cost-effective to produce PCBs in intricate designs and configurations with high levels of reliability and performance.
● Adoption of environmentally friendly materials: The industry is focusing on the development of halogen-free, environmentally friendly Glass Epoxy substrates to meet regulatory requirements and market demand.
Future Outlook of Glass Epoxy
As technology advances and electronic devices become more complex and sophisticated, the demand for high-performance PCBs made from glass epoxy is likely to continue to increase. However, PCB designers will need to keep up with the changing trends in the industry and continued adoption of new technologies such as IoT, edge computing, and 5G.
In addition, the rise of environmental sustainability is likely to drive innovation in eco-friendly PCB materials, which could potentially pose a challenge to the dominance of glass epoxy. Despite this, glass epoxy remains a popular and reliable choice for high-reliability electronic applications, and its versatility makes it a key player in the manufacturing of cutting-edge electronic products.
Final Words
Choose JarnisTech as Your PCB Provider
Glass epoxy is a critical material in the manufacturing of printed circuit boards (PCBs). Its high mechanical strength, resistance to heat and chemicals, and electrical insulation properties make it an ideal choice for PCB substrates. Glass epoxy PCBs are widely used in various electronic devices, from smartphones to high-performance computing equipment. As technology advances and demand for high-speed and high-density PCBs increases, glass epoxy materials play an even more significant role in meeting those demands.
However, it is crucial to adhere to proper handling and disposal procedures to avoid any environmental or health hazards associated with the production and use of glass epoxy materials. Overall, glass epoxy is an essential component in the world of PCB manufacturing, and its importance will continue to grow as technology progresses.
JarnisTech has been a leader in the printed circuit board (PCB) industry since 2000, thanks to our unwavering commitment to utilizing unparalleled epoxy conformal coating in both PCB fabrication and assembly (SMT & DIP). We are ideally positioned to assist you in meeting your coating requirements. Our operations take place in facilities that have been certified to meet the rigorous requirements of both the International Organization for Standardization (ISO) 9001:2015 and the Aerospace Standard (AS) 9100D. This certification assures you that our PCB and PCBA products will be of the highest possible quality. As a PCB manufacturer, we are confident that our expertise and superior coatings will deliver a PCB and PCBA product that exceeds your expectations.
Related Posts:
1. Selecting PCB Laminate Materials: A Comprehensive Overview
2. PCB Copper Trace Width and Space: Everything You Need to Know About Them
3. Which Types are Most Commonly Used in PCB Substrates?
4. What Is Fiberglass PCB and Why Fiberglass Used in PCB Manufacturing?
5. Standard PCB Thickness-Choosing the Correct Thickness for PCB