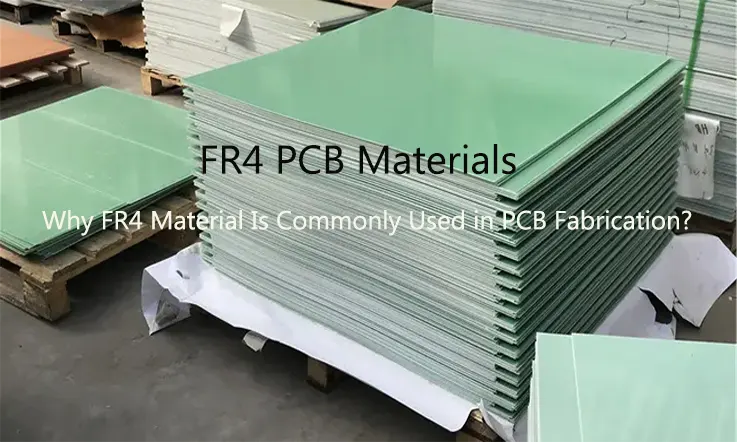
Printed circuit boards (PCBs) are a fundamental component in modern electronic devices, and their material selection is dependent on the specific role they play in the final product. Common PCB materials include aluminum, Rogers, copper, metal, HDI, and FR-4, with FR-4 being the most prevalent choice.
FR-4, a popular choice for PCB construction, is well-known to most electrical engineers and PCB professionals. However, its composition and why it is the preferred choice for these applications may be unfamiliar to many people.
To help clarify the subject, this discussion will explore the features and advantages of FR4 printed circuit boards, including their distinctive properties, widespread use, and how performance specifications of FR4 PCBs compare to alternative materials options in our industry.
Importance of FR4 PCB Materials in Electronics
FR4 PCB materials are important in electronics because they provide a reliable, cost-effective, and widely available substrate for building printed circuit boards (PCBs). FR4 PCB materials offer a high level of performance and durability, making them suitable for a wide range of electronic applications, from consumer electronics to aerospace and defense. They also have good thermal stability, flame resistance, and electrical insulation properties, which allow them to withstand high temperatures and prevent short circuits.
Furthermore, FR4 PCB materials are compatible with a variety of technologies, making them versatile and easy to use for designers and manufacturers. Overall, FR4 PCB materials play a critical role in the design and manufacturing of many electronic devices and systems.
What Is FR4 ?
FR4 is the preeminent material grade for the production of circuit boards, owing to its high usage frequency. The designation “FR” is indicative of the material’s flame-resistant properties, while the digit “4” signifies its woven glass-reinforced epoxy resin composition. An FR4 core and copper layers on both the top and bottom serve as vital components in single or double-sided printed circuit board (PCB) structures.
For multilayer circuit boards, additional prepreg layers separate the center core, top copper layer, and bottom copper layer. The core is typically composed of a substrate that is coated with copper, which is also referred to as a copper-clad laminate. For such applications, copper sheets are placed between the signal and ground layers, with the possibility of using FR4 for the core, laminate, and prepreg.
Although the properties of FR4 can vary slightly by manufacturer, it typically features durable strength and water resistance properties, making it an ideal insulator in various electrical applications. In the case of printed circuit boards, FR4 functions primarily to insulate adjacent copper planes and provide overall bending and flexural strength to the structure. FR4 is a good general-purpose material for PCB fabrication; however, there are other materials available for specific applications or requirements.
FR4 PCB Material
As a PCB manufacturer, it is important to understand that FR4 serves as a fundamental base material for the production of printed circuit boards. This material is comprised of a fiberglass laminate sheet that has been strengthened with epoxy resin, possessing both sturdy physical qualities and the ability to resist flames, making it an optimal substrate choice for laminates.
Given the critical requirement for insulation in circuit board assemblies, FR4 is an indispensable component for ensuring the safe and reliable operation of electronic devices. Although G-10 boards were a popular substrate option in the past, FR4 has largely replaced them due to its superior physical and insulating properties. However, G-10 boards may still be chosen in situations where protection against thermal destruction is paramount, despite the widespread prevalence of FR4 boards as a substitute.
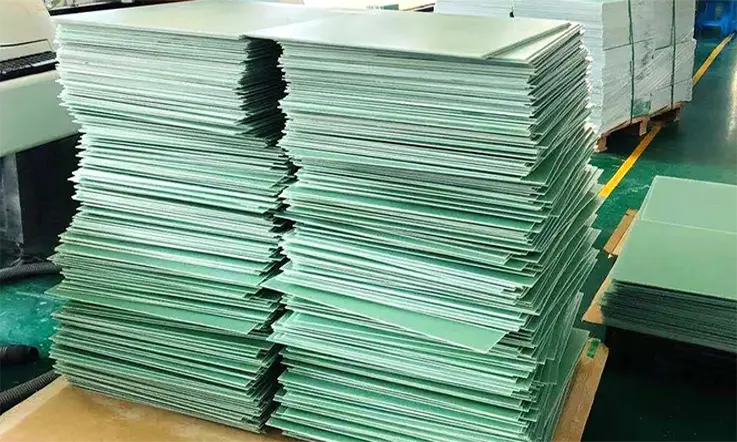
FR4 Properties
● In the domain of plastic flammability, FR4 material meets the standards of the UL94V-0 classification, ensuring that in case of a fire, it does not propagate and extinguishes promptly on the material.
● Bromine plays a crucial role in the production of FR4 materials. As a halogen chemical element resistant to fire, it serves as a valuable medium for imparting fire-retardant properties to FR-4 material.
● Moreover, FR4 material exhibits exceptional insulative capacity, water resistance, and mechanical strength, making it suitable for applications with either dry or wet settings. Its glass transition temperature ranges from 115 to 200 degrees Celsius, based on the utilized resin types and production methodology. Typically, an FR4 PCB comprises an FR4 layer laminated in copper sandwiched between two other copper layer laminates.
● FR4 material is available in multiple varieties, including regular FR4, high TG FR-4, high CTI FR-4, and FR4 without any laminated copper. While a standard FR4 sustains heat resistance between 140 and 150 degrees Celsius, high TG FR4’s glass transition temperature is 180 degrees Celsius. In contrast, high CTI FR4 has an index greater than 600V, and FR4 without laminated copper is optimal for backing boards and functioning as insulation plates.
How FR4 Material Affects PCB Design Considerations
FR4 material can affect PCB design considerations in several ways, including:
● Thickness: FR4 comes in various thicknesses that can affect impedance and capacitance values. Designers need to consider the thickness of the FR4 material when calculating trace widths and spacing.
● Dielectric constant: The dielectric constant of FR4 affects the capacitance value of the traces on the PCB. Designers need to factor in the dielectric constant when determining trace widths and spacing.
● Thermal properties: FR4 has a moderate thermal conductivity, which can affect heat dissipation on the PCB. Designers need to consider the thermal properties of the FR4 material when determining the size and placement of heat sinks and vias.
● Mechanical properties: FR4 is a relatively rigid material, which can affect the mechanical strength and rigidity of the PCB. Designers need to consider the mechanical properties of the FR4 material when designing for shock and vibration resistance.
So, designers need to take into account the properties of FR4 material when making design considerations to ensure that the PCB operates reliably and meets the required specifications.
Common Alternatives to FR4 Material
There are several alternative materials that can be used instead of FR4 for PCB fabrication. Some common alternatives include:
● Rogers 4003C: A high-frequency laminate material with low dielectric loss.
● Polyimide (PI): A flexible material that can withstand high temperatures.
● Aluminum: A metal substrate that provides good heat dissipation.
● Ceramic: A highly durable material that is resistant to corrosion and high temperatures.
● Teflon: A material with low dielectric constant and dissipation factor, suitable for high-frequency applications.
It’s worth noting that each alternative material has its own unique properties and characteristics, which can affect PCB design, fabrication, and cost considerations.
How to Use FR4 in PCB Manufacturing ?
As a PCB designer, it is crucial to understand that FR4 material is an excellent choice for the default substrate material when developing high-quality PCBs. The material’s unique properties can also be leveraged to produce high-quality PCBs at a low cost.
FR4 serves as the primary insulating backbone within a PCB, providing the foundation upon which the circuit will be constructed by the PCB manufacturing company. Once produced, the FR4 board undergoes a lamination process where one or more layers of copper foil are heat-bonded to it. Depending on the board’s design, the copper that builds the circuits in the final product may cover one or both sides of the board.
Complicated PCBs may require the use of multiple layers or both sides of the board to construct intricate circuits. Following this stage, the circuits are sketched out, etched, and then covered with a solder mask layer, preparing the board for the final silkscreen layer and subsequent soldering process. This finalization of the board readies it to be a high-quality, functioning component of the final product.
Considerations for Choosing FR4 PCB Materials Thickness
To PCB design engineers, it is crucial to recognize that the thickness of FR4 material is a crucial factor to consider in various PCB applications. Therefore, when selecting the appropriate thickness, the following should be taken into consideration.
● Connections: The type of connectors utilized for a printed circuit impacts the thickness of the FR-4 layer.
● Impedance Control: The thickness of the board corresponds to the thickness of the dielectric environment, influencing impedance control, a crucial factor.
● Space Saving: Preserving space is a crucial consideration in PCB design, particularly for USB ports and Bluetooth accessories. Hence, adopting the thinnest possible boards is the most space-efficient arrangement.
● Compatibility with Components: FR-4 material is utilized in producing a range of printed circuits, and the thickness of the material affects the type of components that can be employed, particularly for THP components that require thin boards.
● Design and Flexibility: Working with thicker boards is usually preferred by producers since they offer more flexibility in cutting V-grooves. Conversely, a substrate that is too thin may break and become vulnerable to heat damage. During the soldering process, thin boards may bow and assume an unfavorable angle.
● Operating Environment: The PCB’s operating environment must be considered. Thin boards are less stressful for electronic control units in the medical industry. However, overly thin and flexible boards are more susceptible to heat damage and may bow during the soldering process, becoming unfavorable.
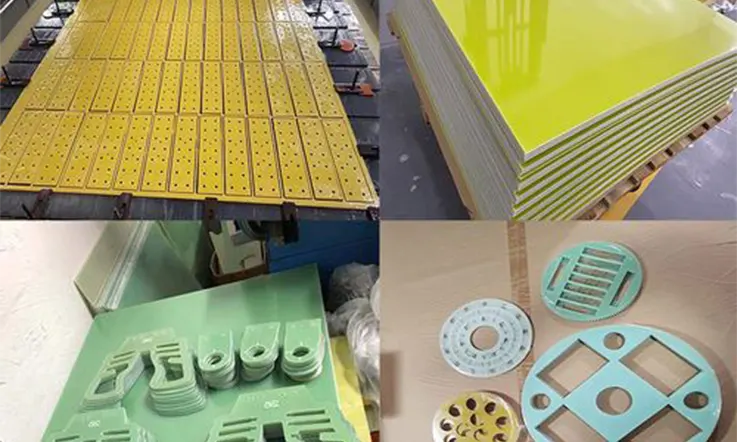
When to Use FR4 in PCBs Fabrication ?
As a PCB manufacturer, it is essential to recognize the popularity of the epoxy-based FR4 board in a range of electrical applications. FR4 epoxy substrates are a cost-effective option for electronic engineers, providing high reliability and robustness. However, when it comes to high-frequency designs, FR4 may not be the best choice of material. High-frequency laminates offer superior electrical characteristics and are commonly used in high-frequency PCB designs.
The decision between these two types of materials can be challenging, and as a manufacturer, we aim to offer additional guidelines to assist in making more informed decisions. When deciding whether to construct a PCB with FR-4 or a high-frequency laminate, it is important to consider the following major characteristics of each material:
● FR4: A popular choice due to its high robustness, reliability, and cost-effectiveness.
● High-frequency Laminates: A preferred substrate material for high-frequency designs due to their superior electrical characteristics.
By taking these factors into account, manufacturers can assist designers in making educated decisions when selecting the appropriate substrate material for their PCB designs.
FR4 Material Cost Considerations
FR4 material is a cost-effective option for PCB fabrication due to its wide availability and relatively low cost compared to other PCB materials. However, the cost of FR4 material can still vary depending on factors such as:
● Thickness: Thicker FR4 materials tend to be more expensive than thinner ones.
● Grade: Higher-quality FR4 materials may have higher costs due to their improved electrical and mechanical properties.
● Finish: The type of finish on the FR4 material can affect its cost. For example, a copper-clad FR4 sheet may be more expensive than a bare FR4 sheet.
● Quantity: The cost per unit may decrease as the quantity of FR4 material ordered increases.
In a words, FR4 material is a cost-effective option for a wide range of PCB applications, and its availability and cost-effectiveness make it a popular choice among PCB designers and manufacturers.
Standard FR4 Laminate vs High Frequency Laminates
FR4 Will Have a Lower Cost Overall:FR4 material is widely used in the production of PCBs, mainly due to its relatively low cost. However, high-frequency laminates are a more expensive alternative, presenting a major challenge for designers and manufacturers concerned about costs. When deciding between FR4 and high-frequency laminates, cost is a crucial consideration that firms need to take into account.
The Signal Loss Is Better for High-frequency Laminate:In the design of printed circuit boards (PCBs), signal loss is an important consideration across a range of applications, particularly in high-frequency contexts where it presents a greater challenge. FR4, due to its larger dissipation factor (Df), is not the best material to use for these designs. As a result, FR4 circuits experience more signal loss than identical circuits constructed using high-frequency laminates.
FR4 possesses a Df of approximately 0.020, which is higher when compared to high-frequency laminates, which typically have a Df of approximately 0.004, one quarter of FR4’s Df value. The smaller the Df value, the lower the overall signal loss. Additionally, the Df of FR4 increases with increasing signal frequency, resulting in more signal loss as the frequency of the signal rises. In contrast, high-frequency laminates consistently maintain their characteristics and experience less signal loss at higher frequencies due to their superior electrical properties.
Impedance Stability (Dk Stability Matters):For PCB design engineers, stable impedance is an essential characteristic that ensures predictable performance, especially in high-frequency or larger circuit designs. However, when comparing FR4 and high-frequency laminates, they exhibit very different outcomes in this regard. Maintaining stable impedance requires a material to retain consistent dielectric constant (Dk) values across the entirety of the material, even when temperature fluctuations occur.
FR4 is not suitable for maintaining stable impedance as its Dk value varies significantly both within a single board and as the board’s temperature changes. In contrast, high-frequency laminates exhibit considerably less variation in Dk values, resulting in stable impedance across much of the board’s surface area irrespective of temperature changes.
The following chart compares the dielectric constants (DK) of FR-4 and several other commonly used PCB materials, highlighting the variation in DK values across different temperature ranges:
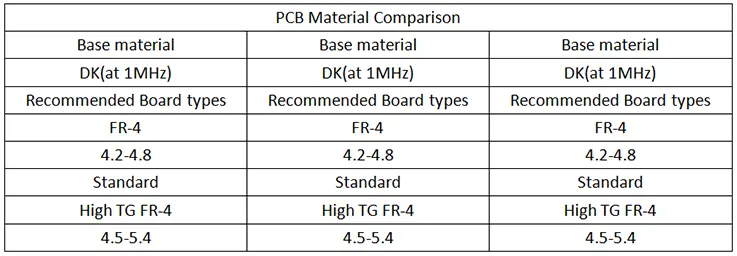
What are the Advantages of Using a PCB Made of FR4 Materials ?
FR4, being a cost-effective material, is commonly preferred by PCB manufacturers for fabricating small PCB batches and for electronic prototyping purposes.
So, What Are the Advantages of FR4 PCB Materials ?
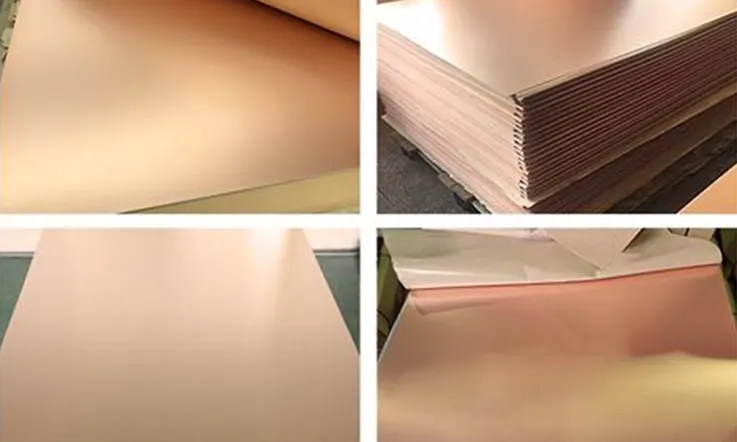
● Moisture Resistant: FR-4 is an excellent material for designing electronic circuits that require moisture resistance. Its resistance to the expansion and contraction effects caused by humidity makes it an ideal choice for Printed Circuit Board designs. Moisture absorption can lead to detrimental effects such as Conductive Anode Filament (CAF) creation, compromising the material’s electrical and thermal properties when devices are powered on. Therefore, FR-4’s superior moisture resistance makes it a highly advantageous material for designing electronic circuits intended for use in humid or marine environments.
● Low-Cost Material: FR-4 is a cost-effective material, readily available for Printed Circuit Board production, while maintaining impressive quality standards. However, materials featuring a high Glass Transition Temperature or Comparative Tracking Index may have a slightly higher cost.
● Higher Decomposition Value: As a PCB manufacturer, it is critical to consider the decomposition temperature (Td) of the laminate, which refers to the temperature at which approximately five percent of its total mass is lost due to breakdown. In this regard, the FR-4 PCB material stands out with its higher Td, exceeding 345 degrees Celsius. A higher decomposition temperature ensures a longer lifespan and increased protection against degradation for Printed Circuit Boards. Hence, assessing Td should be a crucial factor when selecting PCB materials for specific applications.
● High Dielectric Strength: FR-4’s Dielectric strength varies between 4.25 and 4.55, depending on the glass weave type, material thickness, amount of resin present, and copper foil roughness. Dielectric strength refers to the maximum electric field that an insulator can tolerate before it becomes electrically conductive or breaks down. Therefore, selecting a material with a higher dielectric strength is critical in ensuring the insulator’s exceptional quality. PCB designers must carefully consider this quality parameter when examining the suitability of a material for a particular application.
● Load Bearing: FR-4, composed of Fiberglass and epoxy resin, provides the Printed Circuit Board with excellent mechanical strength and a high load-bearing capacity. However, the strength and load-bearing capability of the material relies significantly on its thickness. Standard FR-4 material thickness usually ranges between 0.2 to 3.2 mm, which is a crucial consideration for PCB designers when assessing a material’s suitability for a specific application.
● Higher Glass Transition Temperature: FR-4 boasts a higher Glass Transition Temperature (Tg) of 150Tg or 170Tg, making it exceptionally resistant to high temperatures. The Tg reflects the temperature at which a Printed Circuit Board begins to soften and deform, making it a crucial performance factor. Higher Tg values guarantee better PCB performance, impacting not only its ability to withstand temperature, but also its resistance to moisture and chemicals.
Disadvantages of FR4 PCB Materials
Some potential disadvantages of FR4 PCB materials include:
● Limited frequency response: FR4 PCB materials may not perform well at high frequencies, as they can exhibit signal losses.
● Limited mechanical strength: While FR4 PCB materials are strong, they may not be suitable for high-stress applications where greater mechanical strength is required.
● Environmental concerns: FR4 PCB materials contain fiberglass and epoxy resins that can pose environmental concerns if not properly disposed of.
● Limited thermal dissipation: FR4 PCB materials may not dissipate heat effectively in high-power applications, which can lead to overheating and damage to the circuitry.
● Processing limitations: FR4 PCB materials can be difficult to process using certain manufacturing techniques, such as laser drilling or high-temperature assembly.
It is important to note that some of these disadvantages can be mitigated through proper design and engineering practices, and FR4 PCB materials remain a popular and widely-used substrate for many electronic applications.
Applications of FR4 PCB Materials
FR4 PCB materials have a wide range of applications in various industries, including:
● Consumer electronics: FR4 PCB materials are commonly used in smartphones, laptops, tablets, and other consumer electronics devices.
● Telecommunications: FR4 PCB materials are used in telecommunications equipment such as modems, routers, and switches.
● Aerospace and Defense: FR4 PCB materials are used in aerospace and defense applications because of their high resistance to shock, vibration, and temperature changes.
● Automotive: FR4 PCB materials are used in automotive electronics, such as engine control units, navigation systems, and multimedia systems.
Overall, FR4 PCB materials are used in many industries where high reliability and performance are required, making them a critical component of modern technology.
How to Choose Right PCB Base Material for Your PCB Project ?
For electronics manufacturers, deciding between FR4 and high-frequency laminates requires careful consideration of all electrical and mechanical requirements that a final PCB must meet. The designer should compile a comprehensive list of these requirements and assess them against each other. Moreover, they should evaluate how well FR4 can meet these specifications compared to high-frequency laminates, which are intended for use in high-frequency transmissions. Accessing industry data sheets can provide manufacturers with accurate statistics and information on key characteristics such as dielectric strength, decomposition temperature, thermal conductivity, and mechanical strength.
FR4 is a widely applicable material and has been favored by many electronics manufacturers due to its low cost, mechanical stability, and electrical properties. Despite offering a broad range of sizes and thicknesses and a long list of advantages, it may not be the optimal solution for every application. In particular, it may not be suitable for high-frequency applications such as RF and microwave design, where high-frequency laminates are a better option. Nonetheless, electronics manufacturers must assess the pros and cons of each material and make informed decisions based on the specific requirements of each application.
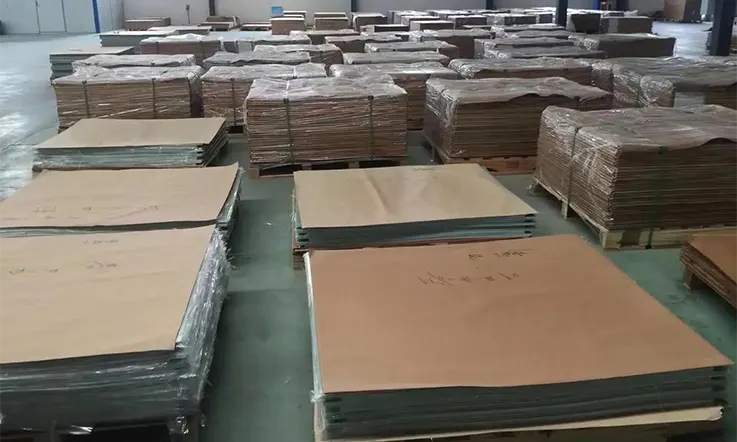
Summary
It is widely known that the thermal reliability of FR4 improves with the material’s temperature gradient (TG), especially in lead-free manufacturing processes. At JarnisTech, we offer TG 150 Laminate as our standard FR-4 board option without any additional fees. We conduct rigorous warehouse inspections and tests on our materials, providing comprehensive reports on the substrate materials to ensure superior quality.
If you are seeking a reliable PCB provider, JarnisTech is your solution. We have been in business for over 20 years, specializing in PCB prototype and PCB assembly services. We understand the importance of providing cost-effective solutions while maintaining high-quality standards for our clients.
Our team is experienced and equipped to fulfill your specific requirements regarding your next PCB project. We welcome you to contact us for more information and discuss your project details in-depth with one of our representatives.
We are dedicated to providing exceptional service and support to ensure the success of each project. Contact JarnisTech for all your PCB prototype and assembly needs.
Related Posts:
1. Selecting PCB Laminate Materials: A Comprehensive Overview
2. PCB Copper Trace Width and Space: Everything You Need to Know About Them
3. Which Types are Most Commonly Used in PCB Substrates?
4. What Is Fiberglass PCB and Why Fiberglass Used in PCB Manufacturing?
5. Standard PCB Thickness-Choosing the Correct Thickness for PCB