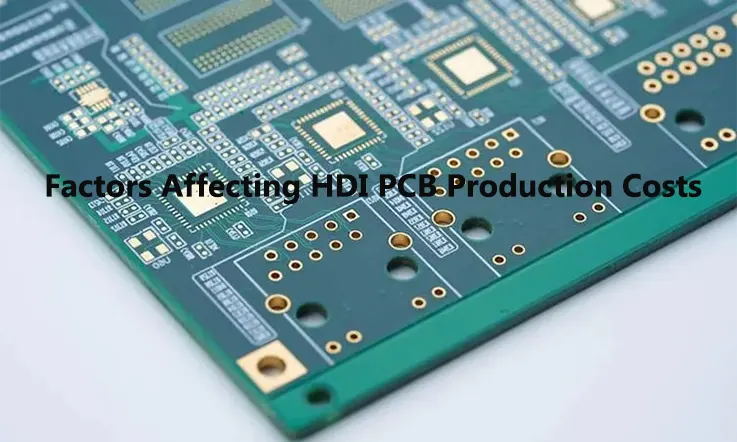
HDI PCBs are a type of printed circuit board characterized by high-density circuits and microvias created through laser drilling techniques. They are widely used for fine-pitch assembly, and leading HDI PCB manufacturers like JarnisTech offer ultra HDI PCB assembly with a minimum pitch as low as 0.05mm. These advanced PCB are essential for various applications such as IC load boards and implanted medical devices, where compactness and thinness are critical requirements.
However, it is worth noting that HDI PCB can be relatively expensive. Many clients often approach us, as an experienced HDI and IC load board PCB manufacturer, seeking guidance on how to reduce the costs associated with HDI PCB production. In response to this common query, we have compiled some valuable suggestions to help address this concern effectively.
Key Factors Impacting HDI PCB Manufacturing Costs
HDI Printed Circuit Boards are crucial in contemporary electronics for supporting complex, high speed and high frequency designs. The cost of HDI PCB production is influenced by several factors:
Board Complexity: The complexity of the board design has a substantial impact on production cost. More intricate designs necessitate more layer, vias and other features, all of which contribute to increased manufacturing time and expense.
Board Size and Shape: Larger boards necessitate more materials and extended production time, which elevates costs. Additionally, irregular shapes may demand specialized tooling or handling, further increasing expenses.
Materials Used: Material selection has a significant impact on costs. For instance, opting for high-frequency materials like Rogers or Teflon can considerably raise expenses compared to standard FR4 materials.
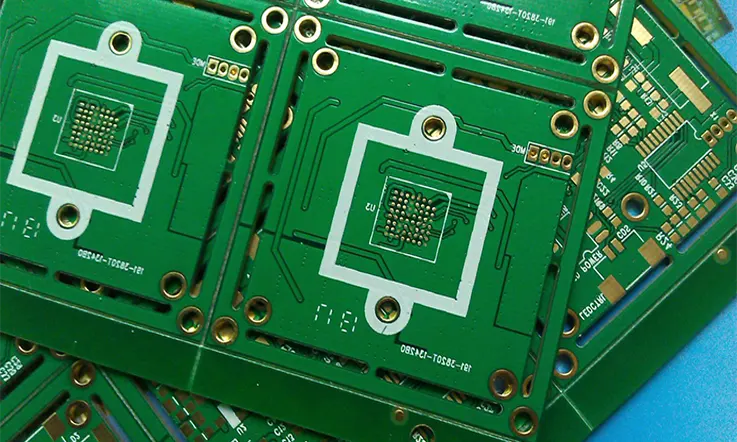
Layer Count: An increased number of layers mean more drilling, etching, and lamination cycles, which can lead to higher costs and longer manufacturing times.
Via Types: HDI PCB can incorporate through vias, blind vias, or buried vias. Implementing buried vias involves additional process steps, resulting in higher costs.
Surface Finish: The choice of surface finish can influence the overall cost. Options such as HASL (Hot Air Solder Leveling), ENIG (Electroless Nickel Immersion Gold), and OSP (Organic Solderability Preservative) each have distinct cost implications.
Quantity: Economies of scale are relevant to PCB production. Manufacturing a larger quantity of boards in a single batch can substantially lower the cost per unit.
Turnaround Time: Expedited production schedules typically incur a premium. If fast turnaround for PCB is required, higher costs should be anticipated.
Testing Requirements: The level of testing required varies based on the application. More stringent testing procedures will consequently elevate the overall cost.
Certification Requirements: Adherence to specific industry standards or certifications, such as UL or RoHS, maybe also elevate production costs for your PCB.
Manufacturer’s Capabilities and Location: The price can also be affected by the expertise, experience and location of the manufacturer. Companies located in areas with labor costs might offer better prices but this could result in compromises, on quality, delivery speed or communication effectiveness.
Remember, the cheapest option isn’t always the best, especially for crucial components like HDI PCB. It’s important to consider factors like quality, reliability, and manufacturer reputation alongside cost when making your decision.
Why Are HDI PCB Important?
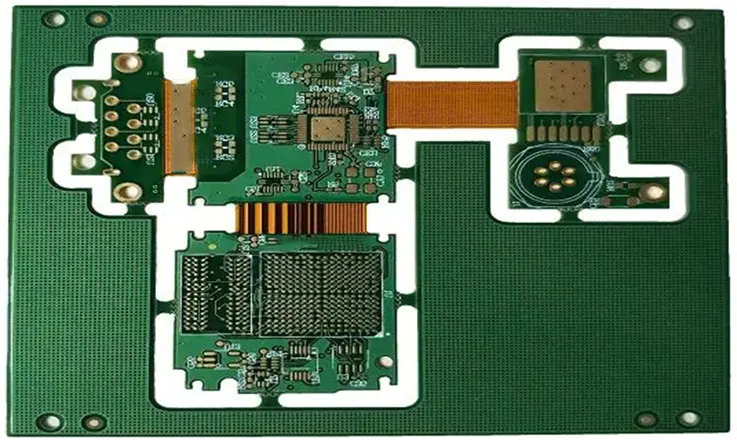
High Density Interconnect PCBs play a role in todays electronics for various reasons:
Miniaturization:
HDI PCB enable higher component density, allowing for the placement of more components on both side of the PCB. This capability has facilitated the design of smaller and more complex electronic devices, ranging from smartphones to medical equipment, without compromising their functionality.
Enhanced Performance:
HDI technology enables shorter interconnection paths, significantly improving signal integrity and overall device performance. Additionally, it can reduce electromagnetic interference (EMI), a common issue in high speed electronic devices.
Greater Design Flexibility:
HDI PCB offer enhanced design freedom. Designers can utilize blind and buried vias, along with microvias, to develop more intricate circuits. This flexibility facilitates innovative designs and results in more powerful devices.
Cost Reduction:
Although the initial design and manufacturing expenses for HDI PCB are higher compared to conventional PCB, they offer long term cost saving. The capacity to integrate more components within a smaller area reduces overall material cost. Additionally, the enhanced performance minimizes the need for rework and repairs, resulting in greater cost efficiencies.
Advanced Technology Technology:
HDI PCB play a role in the development of modern technologies, like IoT devices, wearable tech and high frequency applications. These technologies demand compact, high-performance components, and HDI PCB are well suited to meet these requirements.
Consequently, HDI PCB are crucial due to their capacity to support device miniaturization, enhance performance, offer greater design flexibility, reduce cost and facilitate advanced technologies.
Final Thoughts
To achieve optimal cost efficiency for your HDI PCB, it is essential to consider a range of factors including production processes, PCB material selection, drilling methods and imaging techniques.
Therefore, it is highly recommended to engage in early consultations with your selected PCB manufacturer during the design phase. This collaborative approach will facilitate the optimal balance among cost, manufacturability and performance, tailored to the specific requirements of your design. By seeking their expertise and guidance from the outset, you can make informed decisions that align with your project’s goals.
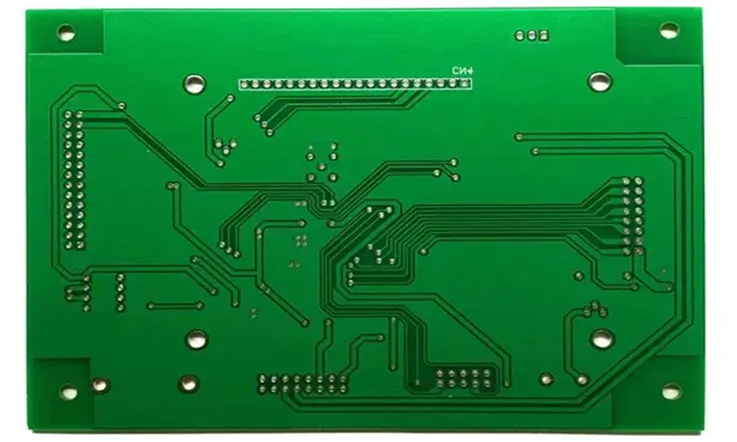
So, It is essential to acknowledge that if building a circuit board is challenging even with a limited number of prototypes, scaling up to high volume production can introduce further complexities. This consideration the importance of thorough planning and assessment to ensure smooth manufacturing processes during production runs.