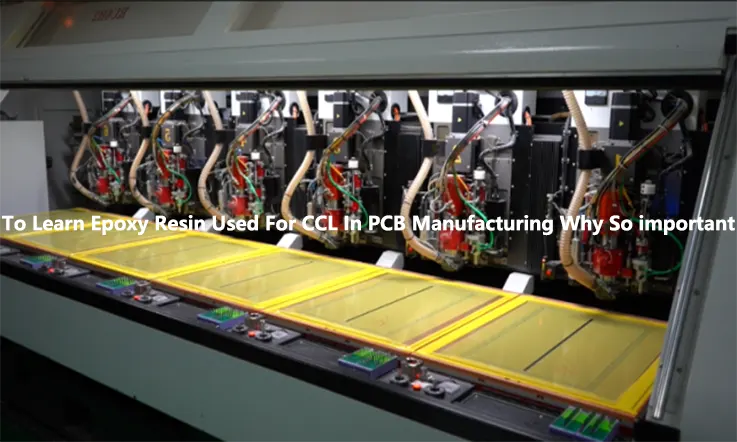
Epoxy resin is a primary constituent of Copper Clad Laminate (CCL), which serves as the substrate material for Printed Circuit Boards (PCBs). The molecular architecture and properties of epoxy resin play a vital role in defining the performance of CCL. Continuous advancements in epoxy resin development have facilitated incremental improvements in the performance of CCL.
As the electronic information industry has undergone rapid growth, PCB fabrication technology has shifted towards microvia, fine trace, high-density tracing, and multiple layers. These trends demand heightened efficacy in thermal dissipation capacity, dimensional stability, and dielectric loss of CCL. Consequently, the progress of epoxy resin material science has embraced new performance requirements.
Definition of Epoxy Resin
Epoxy resin is a synthetic polymer widely utilized across several industries due to its exceptional mechanical, chemical, and electrical properties. This material is composed of two components – the epoxy resin and a hardener. The combination of these components results in a robust and durable material.
The versatility of epoxy resins allows for their use in the manufacture of adhesives, coatings, and composites. They have the ability to bond strongly with a wide range of materials, exhibit resistance to water and chemicals, and possess favorable mechanical properties. In the electronics industry, epoxy resin serves as a substrate material for Printed Circuit Boards (PCBs). This is due to its excellent insulation capabilities, mechanical strength, low water absorption, and chemical resistance.
Property of Epoxy Resin
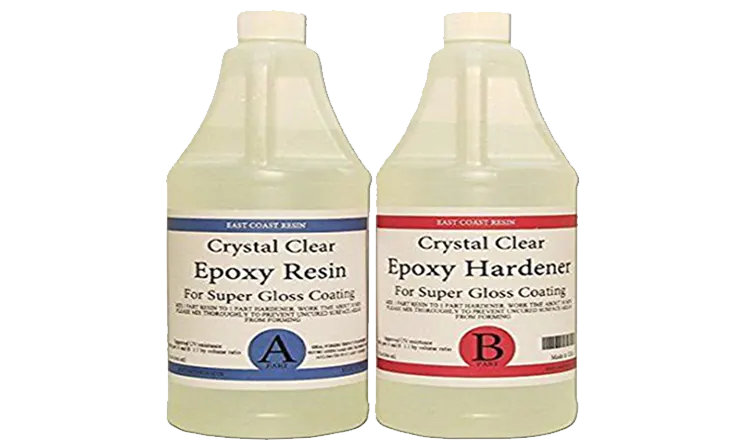
● Low Water Absorption: Epoxy resin boasts an exceptional attribute of minimal water absorption, rendering it highly suitable for deployment in Printed Circuit Boards (PCBs) that may encounter moisture exposure.
● Electrical insulation: Epoxy resin exhibits outstanding electrical insulation characteristics, rendering it a desirable material choice for Printed Circuit Boards (PCBs). Its high dielectric strength, low dielectric constant, and low dissipation factor are instrumental in averting signal loss and interference.
● Chemical resistance: The excellent chemical resistance of epoxy resin positions it as a suitable option for use in Printed Circuit Boards (PCBs) that face exposure to severe environmental conditions.
● Mechanical properties: Epoxy resin is characterized by elevated mechanical strength and rigidity, thus rendering it an appropriate choice in the manufacturing of Printed Circuit Boards (PCBs). This material is capable of withstanding high temperatures and possesses commendable dimensional stability; this allows the PCBs to retain their shape and size throughout the production process.
● Thermal properties: Epoxy resin possesses favorable thermal stability that averts degradation of the Printed Circuit Board (PCB) due to heat impact. The material exhibits the capability to endure high temperatures, and its low coefficient of thermal expansion makes it an appropriate option for use in PCBs.
In a words, the combination of excellent electrical, mechanical, and thermal properties, along with chemical resistance, makes epoxy resin a popular choice for CCL in PCB manufacturing.
Common Epoxy Resin in PCB Manufacturing
Epoxy resins are commonly used in the manufacturing of Printed Circuit Boards (PCBs). They are used as the primary material for Copper Clad Laminates (CCL), which are the base material for most PCBs. Within epoxy resins, the following types are commonly used:
● PTFE Resin.
● High Tg Epoxy Resin.
● Low Dk Epoxy Resin.
● Low CTE Epoxy Resin.
● Hight CTI Epoxy Resin.
● Low Flow Epoxy Resin.
● Lead-free Epoxy Resin.
● Thermoset Epoxy Resin.
● BT Modified Epoxy Resin.
● Halogen-free Epoxy Resin.
● Ceramic Filled Epoxy Resin.
● Polyimide Modified Epoxy Resin.
● High Thermal Conductive Epoxy Resin.
The choice of epoxy resin in PCB manufacturing is determined by the specific requirements of the application, including factors such as cost, thermal stability, dielectric constant, and glass transition temperature.
Quick Overview of Epoxy Resin CCL
Copper Clad Laminate (CCL) is the primary material component of a Printed Circuit Board (PCB). The PCB substrate acts as a base for the fabrication of traces, pads, and vias. CCL is essentially a substrate material that has been pre-impregnated with an epoxy resin adhesive. Copper foil is then applied to the top and bottom of the pre-impregnated sheet, followed by processing through a high-temperature, high-pressure, and high-vacuum pressing machine to form a “lamination.”
The lamination formed from the sandwich of the PCB base substrate, copper foil, and epoxy resin adhesive is referred to as CCL. This pre-manufactured CCL is a necessary and essential material used to produce PCBs through subsequent fabrication processes.
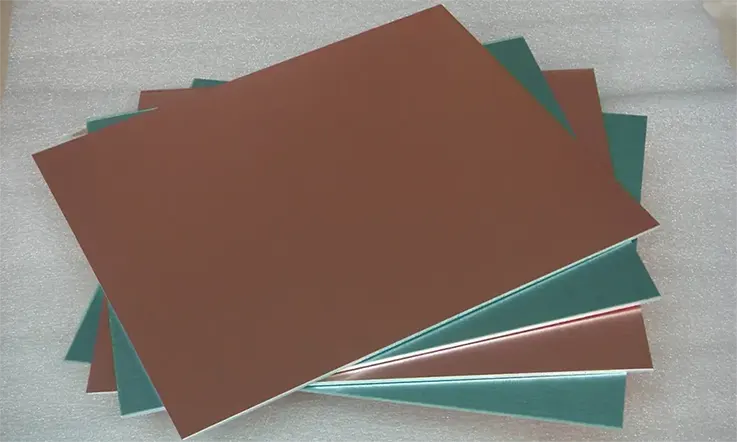
Epoxy Resin Based CCL Types
● Copper Clad Laminates (CCLs) exist in diverse forms, with more than 70 percent of all CCLs being epoxy resin-based. The primary types of epoxy resin composite CCLs comprise CEM-1 and CEM-3 while the leading categories of epoxy resin paper-based CCLs consist of FR-1 and FR-3. In comparison, the most commonly used epoxy resin glass fiber CCLs include FR-4, G-10, G-11, and FR-5.
● High-performance, multifunctional, epoxy resin glass fiber CCLs comprise various types as follows: those featuring a high glass transition temperature (Tg: 175°C), lead-free compatibility, high Comparative Tracking Index (CTI), Conductive Anodic Filament (CAF) resistance, high thermal conductivity, FR-4 suited for the manufacture of High Density Interconnect (HDI) substrates, polyimide modified epoxy, BT modified epoxy, PPO modified epoxy, CE modified epoxy glass fiber CCL, and epoxy glass fiber prepreg and Resin Coated Copper (RCC) employed in the production of multilayer PCBs and Build-Up Multilayer (BUM) PCBs.
Currently, there is a broad range of Copper Clad Laminates (CCLs) available and utilized in the fabrication of Printed Circuit Boards (PCBs). These CCLs vary considerably in terms of material types, compositions, and properties. Generally, the thickness of CCLs used to manufacture PCBs ranges between 0.05 and 3.2 mm, depending on the specific application requirements and design considerations.
Progress and Direction of Epoxy Resin CCL
Copper Clad Laminate (CCL) technology has seen continual progress for close to a century, with PCB sector advancements driving such progress. Cutting-edge research and development in electronic machine goods, semiconductor fabrication, electronic assembly, and PCB fabrication have been instrumental in the advancement of CCLs.
Electronic packaging engineering and technology are the primary drivers behind the development of CCLs. As such, the rapid advancements in light weight, thinness, miniaturization, high performance, multiple functions, high reliability, and IC chip performance contribute significantly to the high-speed development of electronic packaging technology.
The rapid progression of electronic packaging technology led CCLs to pursue characteristics such as miniaturization, light weight, high speed, thermal dissipation, high-temperature resistance, eco-friendliness, CAF and CTI tolerance, high intensity, high modulus, multi-functionality, and high reliability. This continuous technological development calls for even higher and more stringent demands.
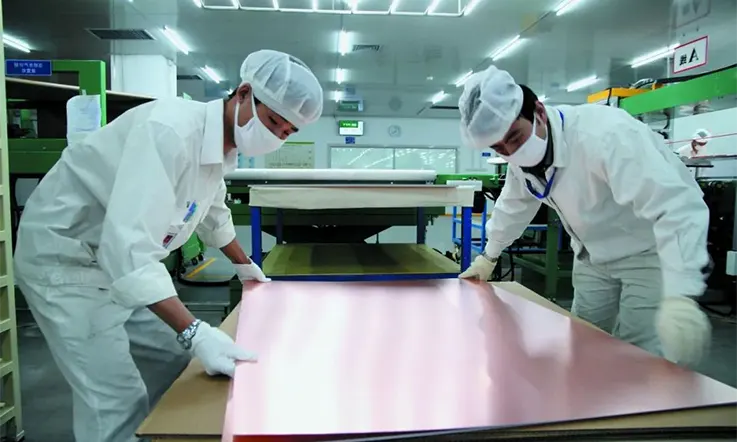
CCL’s Requirement on Epoxy Resin
● As one of the most essential substrate materials for electronic devices, the primary function of Copper Clad Laminates (CCLs) is to provide efficient insulation for traces and electronic products. For this reason, high purity, low humidity, and robust mechanical properties are crucial requirements for epoxy resin in CCLs. Moreover, the ongoing progress of technology demands that the performance of epoxy resin continues to improve.
● High purity is a fundamental requirement for epoxy resin, especially concerning the concentration of alkali metals (Na+) and chlorine content, with stringent regulation to ensure specific levels. Although the majority of electronic-grade epoxy resin available in the market meets the required standards regarding alkali metal and chlorine content, hydrolysable chlorine ions can still affect device performance.
● The presence of hydrolysable chlorine ions in epoxy resin accelerates erosion in electronic devices when exposed to water, thereby reducing their lifespan significantly. Thus, it is crucial to keep the overall amount of chlorine in epoxy resin below 500 ppm and the amount of hydrolysable chlorine ions below 300 ppm.
● In addition to low humidity and high purity, robust mechanical properties enable CCLs to perform a supporting function in electronic goods, making them highly dependable.
CCL’s New Requirement on Epoxy Resin
With the upsurge of microvia, fine trace, high-density tracings, and high and multiple layer trends in Printed Circuit Board (PCB) fabrication technology, new requirements are emerging in Copper Clad Laminates (CCLs) regarding their thermal withstanding, low Coefficient of Thermal Expansion (CTE), high dimensional stability, and low dielectric loss. These requirements are critical to maintain pace with the rapid growth of the electronic information industry.
As a result, epoxy resin, which is the primary raw material in CCLs, faces increasing challenges from modern technology requirements. However, it remains a critical component of CCLs due to its excellent insulation and adhesive properties. Therefore, researchers and manufacturers are continually seeking ways to enhance the performance of epoxy resin-based CCLs to meet the latest technological demands.
Common New Requiremnet:
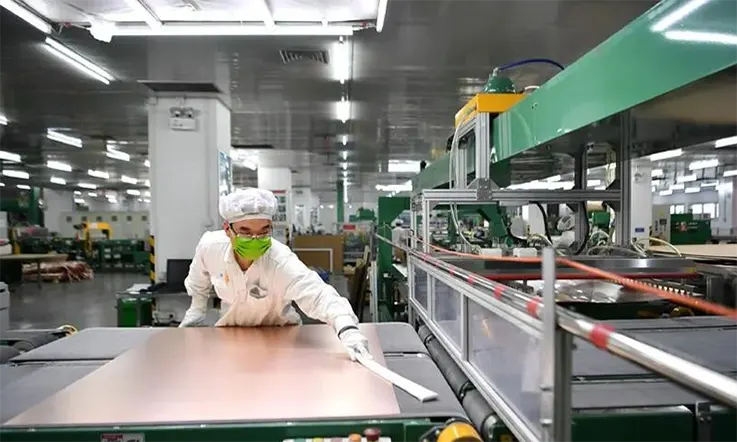
● High comparative tracking index (CTI) epoxy resin CCL: The CTI measures the breakdown voltage of an insulating material when a potential difference is present. The conventional FR-4 based epoxy resin CCL has a typical CTI index of around 200V, while it should be in the region of 600V. The high leakage rate is usually due to carbon routes that have formed within the material. Therefore, choosing an epoxy resin that exhibits low leakage and excellent electrical insulation is highly desirable.
● Low dielectric constant (Dk) and Low dissipation factor (Df) epoxy resin: To enhance signal integrity, engineers and scientists are focusing their efforts on reducing the dielectric constant and the dissipation factor, also known as Dk and Df, respectively. This research is beneficial in minimizing signal losses, decreasing inductance in the signal path, and minimizing the impact of cross-talk and electro-magnetic interference (EMI) in high-speed, high-frequency, and high-density printed circuit boards (PCBs) and circuits.
Important of Epoxy Resin Used For CCL in PCB Manufacturing
Epoxy resin is an essential component in the manufacturing of Copper Clad Laminates (CCLs) for Printed Circuit Boards (PCBs). CCLs provide insulation for electronic products and traces in electronic devices. The increasing trend towards microvia, fine trace, high-density tracings, and high and multiple layer PCB designs demands higher performance from CCLs. This trend necessitates continuous improvements in the quality of epoxy resin used in CCLs to meet the latest technological demands of the electronic information industry.
Thermal withstanding, low CTE, high dimensional stability, low dielectric loss, and environmental protection are critical performance parameters in CCLs. Epoxy resin is the primary raw material that determines the quality of these parameters. CCL manufacturers require epoxy resin that has high purity and mechanical strength, low humidity absorption, low dielectric constant, low dielectric loss, and high thermal resistance. Additionally, epoxy resin used in CCL manufacturing must have excellent adhesion to copper and other materials used in PCBs while maintaining good chemical resistance.
As engineers and scientists push the limits of PCB technology with high-speed, high-frequency, high-density, low-loss, and low-cost PCBs, the demands on CCLs are increasing. This increase in demand is driving the development of better-performing epoxy resin for use in CCLs. As such, epoxy resin plays a pivotal role in the manufacturing of CCLs and ultimately contributes to the overall performance of electronic products.
Sum Up
In line with the development of high-speed, high-frequency, high-integration, high-reliability, high-density, low-loss, and low-cost Copper Clad Laminates (CCLs), the performance demands placed on epoxy resin are continuously increasing. This is driven by developments in electronic assembly technology, High-Density Interconnect (HDI) engineering, and cost performance advancements.
As CCLs continue to evolve at a rapid pace, manufacturers are demanding higher performance attributes from epoxy resin. These requirements include excellent thermal resistance, low humidity absorption, low dielectric constant, and eco-friendliness. Moreover, the manufacturability and cost-effectiveness of epoxy resin have to comply with the demands of CCL manufacturing. Hence, it is imperative to continually improve the quality and performance of epoxy resins to keep up with the evolving needs of CCL technology.