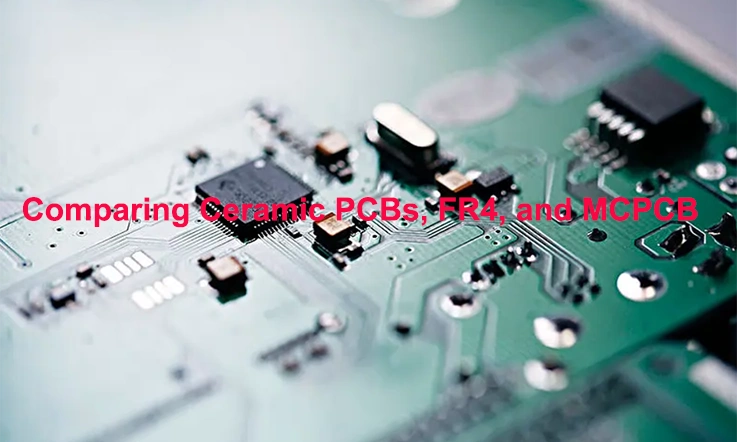
Printed circuit boards (PCBs) are components in various electronic devices. Choosing the type of PCB for a particular use depends on factors, like performance requirements, cost efficiency and ease of manufacturing. This article intends to compare three PCB types. Ceramic PCBs, FR4 PCBs and MCPCBs. By exploring their pros, cons and typical uses we aim to highlight the ways to use each type of PCB.
Ceramic PCBs
Ceramic PCBs, a variant of printed circuit boards (PCBs), utilize ceramic substrates instead of conventional fiberglass or epoxy resin substrates. These specialized PCBs boast several advantages over their traditional counterparts, including:
●Enhanced Thermal Conductivity
●Reduced Coefficient of Thermal Expansion (CTE)
●Superior Electrical Insulation
●Chemical and Solvent Resistance
While ceramic PCBs typically come at a higher cost compared to traditional PCBs, their exceptional performance characteristics make them an excellent choice for applications demanding high power and reliability.
Applications of Ceramic PCBs:
●High-power Electronics
●Aerospace and Defense.
●Medical Devices
●Automotive Electronics.
●In the realm of consumer electronics
Although Ceramic PCBs offer benefits it’s crucial to acknowledge their drawbacks:
●Cost; Ceramic PCBs generally come at a price compared to traditional PCBs due to the specialized materials and manufacturing processes required.
●Complexity in Manufacturing; The production of PCBs can be more complex and demanding than that of PCBs because of the specific needs for ceramic substrates and the necessity, for specialized equipment and expertise.
●Brittle Nature: Ceramic materials can exhibit brittleness, making ceramic PCBs more susceptible to mechanical stress and potential damage. Proper handling and design considerations are essential to mitigate these risks.
FR4 PCBs
FR4 circuit boards are commonly known as the used type of circuit boards, in the electronics field. These boards are made from a combination of epoxy resin and fiberglass creating an long lasting material that shows resistance to heat and chemicals. Moreover FR4 circuit boards are cost efficient which explains their popularity, in applications.
Advantages:
●Cost-effectiveness
●Ease of Manufacturing
●Strength and Durability
●Resistance to Heat and Chemicals
Disadvantages:
●Lower Thermal Conductivity
●Higher Coefficient of Thermal Expansion (CTE)
●Lower Electrical Insulation
Applications:
Consumer Electronics; FR4 PCBs are crucial components, in manufacturing consumer electronic gadgets like smartphones, tablets and household appliances due to their cost efficiency and durability.
Industrial Electronics; In industrial environments FR4 PCBs serve a broad range of functions including controlling systems, monitoring devices and automated machinery.
Automotive Electronics; FR4 PCBs play a role in ensuring the operation of automotive electronic systems such as engine control units, entertainment systems and safety mechanisms.
Medical Devices; The medical sector benefits from the strength and chemical resistance provided by FR4 PCBs. They are utilized in devices spanning from tools to implantable devices.
Aerospace and Defense: FR4 PCBs are essential, in aerospace and defense applications supporting avionics, space technology systems communication devices and military technologies.
When designing an FR4 PCB, several factors should be considered:
1. Board Layout: A planned board layout should aim to reduce problems associated with heat dissipation and CTE guaranteeing functionality, for its intended purpose.
2. Material Selection: The specific requirements of the application should guide the selection of the appropriate FR4 laminate type, considering factors such as operating conditions and performance expectations.
3. Manufacturing Process: Strict control over the manufacturing process is necessary to achieve the desired specifications and ensure the reliability of the resulting FR4 PCB.
When comparing PCBs, to FR4 PCBs FR4 boards have advantages when it comes to cost effectiveness, manufacturing simplicity, durability and resistance to heat and chemicals. On the hand ceramic PCBs shine in terms of their thermal conductivity lower coefficient of thermal expansion (CTE) and superior electrical insulation properties. Even though ceramic PCBs are pricier and present challenges during manufacturing they are the option for applications that require performance. Conversely FR4 PCBs are suitable, for situations where cost and ease of production take precedence while still delivering performance.
Metal Core PCBs (MCPCBs)
Metal core PCBs, also known as MCPCBs are a kind of printed circuit board that uses a metal core of the typical fiberglass or epoxy resin core. By incorporating a metal core these boards offer benefits compared to PCBs greatly improving their effectiveness, in different scenarios.
Advantages of MCPCBs:
1. Higher Thermal Conductivity: Metal has a ability to conduct heat, than fiberglass or epoxy resin. This unique feature allows MCPCBs to effectively release heat making them ideal, for high power uses where managing heat’s essential.
2. Lower Coefficient of Thermal Expansion (CTE): Metal possesses a lower CTE than fiberglass or epoxy resin. As a result, MCPCBs experience minimal expansion or contraction with changes in temperature, ensuring their stability and reliability in harsh operating environments.
3. Higher Mechanical Strength: Metal provides strength, than fiberglass or epoxy resin making MCPCBs more resistant, to bending, vibrations and mechanical stress. This quality improves their durability and lifespan.
Manufacturing MCPCBs tends to be pricier compared to PCBs because of the materials and techniques used. Despite the cost their outstanding performance qualities make them a top pick, for tasks demanding power and dependability.
Types of MCPCBs:
1. Single-Sided MCPCBs: Single layered MCPCBs include a metal core, on one side and a dielectric material layer on the side. This setup provides conductivity benefits while keeping costs lower, than double sided MCPCBs.
2. Double-Sided MCPCBs: 2 layer Metal Core Printed Circuit Boards (MCPCBs) feature a metal core, on each side sandwiched between layers of material. This configuration boosts conductivity. Enhances heat dissipation efficiency, across both surfaces of the PCB.
Applications of MCPCBs:
MCPCBs find widespread utilization in various industries and applications:
●High-Power Electronics
●Aerospace and Defense
●Medical Devices
●Automotive Electronics
●Consumer Electronics
MCPCBs have benefits such, as heat conductivity, lower CTE and stronger mechanical properties, which make them ideal for challenging tasks. Nonetheless it’s crucial to factor in the production expenses added manufacturing intricacies and possible weight implications linked to MCPCBs when assessing their suitability for projects. In general MCPCBs provide advantages, for power and highly reliable applications validating their use despite the obstacles they present.
Comparison of MCPCB, FR4 PCB, and Ceramic PCB
The comparison table below outlines the key characteristics of MCPCBs, FR4 PCBs, and ceramic PCBs:
Characteristic | MCPCB | FR4 PCB | Ceramic PCB |
Thermal conductivity | High | Medium | High |
CTE | Low | Medium | Low |
Mechanical strength | High | Medium | Low |
Cost | High | Low | Medium |
Ease of manufacturing | Medium | Easy | Difficult |
MCPCBs show efficiency and mechanical durability compared to the other two types. Despite their advantages they come with a price tag. Pose manufacturing challenges. On the hand FR4 PCBs provide a mix of performance and affordability making them a versatile option, for various uses. Ceramic PCBs boast notch conductivity and low CTE levels; however they are also expensive to produce and present manufacturing complexities.
In short choosing the type of PCB depends on what the application calls for. MCPCBs work well for high power uses that need heat dissipation and strong mechanical capabilities even though they are more expensive and complex to manufacture. On the hand FR4 PCBs offer a budget option, with decent thermal performance and mechanical strength, for a range of applications. Ceramic PCBs stand out for their conductivity and low CTE. Their higher cost and manufacturing complexities mean they are better suited for specialized applications that require top notch performance.
Get in Touch with JarnisTech for Your PCB Requirements Today
Looking for all your printed circuit board needs? Look no further, than JarnisTech. We offer a selection of PCB options, including ceramic, copper and aluminum boards in multi layer configurations.
If you’re unsure about the type of boards you require or have questions about our PCB offerings. Whether its pricing, delivery options or specific board details. Feel free to get in touch with us. Reach out to our team at 755 230 34656. Submit an online request, for a quick and complimentary quote tailored to your PCB requirements.
Conclusion
When deciding between Ceramic PCBs, FR4 PCB and MCPCBs the choice ultimately comes down to the requirements of the application. Ceramic PCBs are ideal, for high performance situations that require conductivity and low CTE despite being more expensive and complex to manufacture. FR4 PCBs provide a cost option with decent performance features making them suitable for a variety of uses. Meanwhile MCPCBs stand out for their conductivity low CTE and strong mechanical durability making them perfect, for applications needing high power and reliability even though they come at a higher price and are more challenging to produce.
In the end engineers and designers need to assess the projects needs taking into account aspects like managing heat ensuring strength, budget limitations and feasibility of production. By utilizing Ceramic PCBs, FR4 PCBs and MCPCBs effectively they can create cutting edge and dependable systems that cater to the requirements of modern industries that are constantly evolving.
Our services
Metal Core PCB Manufacturing & Assembly