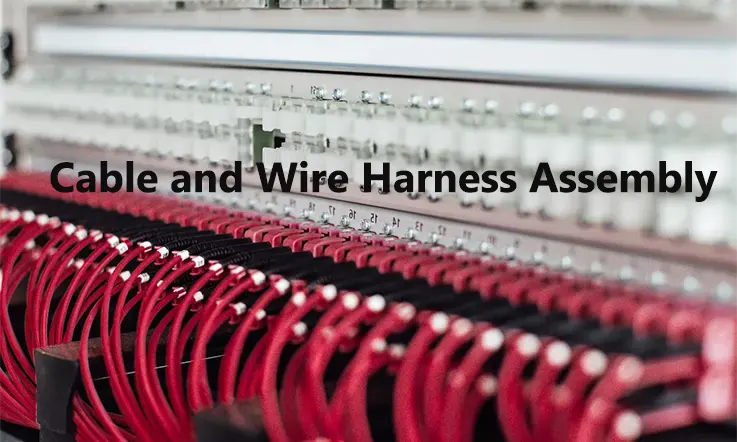
With an extensive track record spanning two decades, JarnisTech stands out as a trusted provider of premium custom cable and harness assemblies to global high-tech clientele. Our repertoire includes a diverse set of processes like manufacturing, ultrasonic welding, and injection molding, enabling us to deliver exceptional products and services across a broad spectrum of complexity, ranging from simple to intricate cable and harness assemblies. Whether clients require prototypes or turnkey solutions, we consistently meet their diverse needs with precision.
At JarnisTech, we understand the value of efficient and real-time communication. That’s why our exceptional team is adept at facilitating seamless collaboration, expediting the assembly process and ensuring speedy time-to-market results.
Our wire harness assemblies can be tailored to possess a versatile range of properties and conform to various industry standards. Beyond ensuring continuity and functionality through comprehensive testing, we also offer specialized services such as box assembly and cleanroom assembly (Class 10,000). Quality is of utmost importance to us, which is why our facilities hold ISO 9001:2008 certification. Through stringent testing and robust quality control measures, we ensure that all our products consistently adhere to the same exceptional standards.
To gain deeper insights into our comprehensive custom cable and harness assembly services, we encourage you to reach out to us directly.
Wire Harness Assembly (Sometimes called a cable) Definition
The primary function of a wire harness assembly is to address challenges related to electrical requirements and spatial limitations within electrical systems. It serves to provide physical support and organization for a collection of cables and wires within a designated space. While wire harnesses are primarily used for organizational purposes in applications with less demanding requirements, they are not typically suitable for outdoor use or in environments with potential environmental hazards.
Referred to as cable or wiring looms, harness assemblies effectively arrange groups of wires and/or cables into a unified unit for protection and organization. They incorporate a variety of terminals and connectors that are strategically positioned and routed to the various connection points of an assembly. Wire harnesses offer an economical electrical solution specifically designed to streamline wiring systems.
Maintaining precise lengths and orientations of wires and cables is paramount to ensure efficient and straightforward installation processes. Assemblies can encompass a diverse range of cable or wire constructions, sizes, colors, and materials, all selected according to the specific application requirements.
A typical harness assembly utilizes sleeved wires and/or multi-conductor cables held together by ty wraps or tubing, which both safeguard and organize the bundled wires and cables. Unique terminations, such as plug or socket arrangements, are often necessary for specific applications, and are appropriately attached to the wires. Given the multitude of potential variables involved, all wire harnesses are customized to suit their intended operating environment.
Wire Harness Fabrication
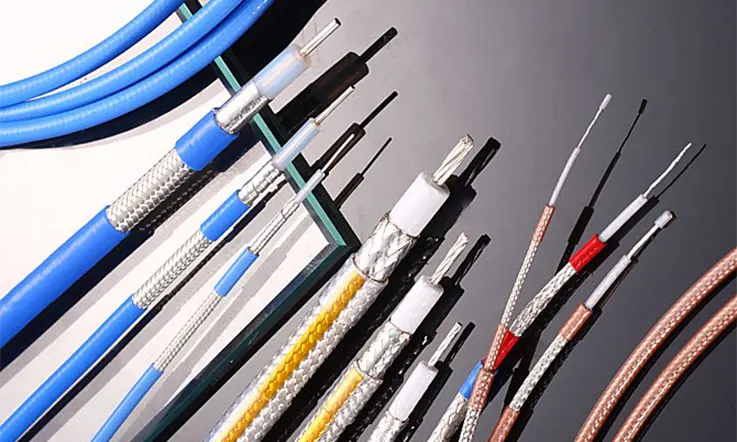
The wires required for the harness are initially trimmed to the desired length and appropriately labeled. Subsequently, the wire ends are stripped to expose the uninsulated conductor and equipped with necessary terminals or connector housings. The wires and components are thereafter assembled on the pin-board according to the desired specifications, and finally secured together.
Why Are Wire Harnesses Assembled Manually ?
The wire harness assembly process remains predominantly a manual operation, as it encompasses a range of intricate procedures that are more effectively carried out by human hands rather than automation. These manual processes involve:
● Installing terminated wires of varying lengths.
● Routing wires and cables through sleeves and conduits.
● Applying tape to secure wire breakouts.
● Executing multiple crimps.
● Binding components together using tape, clamps, or cable ties.
Due to the complexity of automating these tasks, manual production continues to be the more cost-efficient option, particularly when dealing with small production runs. Consequently, harness production generally requires a longer timeframe compared to other types of cable assemblies, ranging from a few days to several weeks. The level of intricacy in the design directly influences the duration of the production process.
Nevertheless, there are specific pre-production stages that can benefit from automation, such as:
● Employing automated machines to cut and strip wire ends individually.
● Utilizing automated crimping systems to attach terminals on one or both sides of the wire.
● Inserting wires, pre-fitted with terminals, into connector housings.
● Employing automated soldering processes for wire end connections.
● Implementing automated wire twisting techniques.
Production Wire Testing
Following the completion of the wire harness assembly process, the crucial final step involves testing the harness for its electrical functionality. To accomplish this, a specially designed and pre-programmed test board is utilized. The test board is configured with the necessary electrical specifications, and the fully assembled harness is connected to the board for a comprehensive fault-checking procedure.
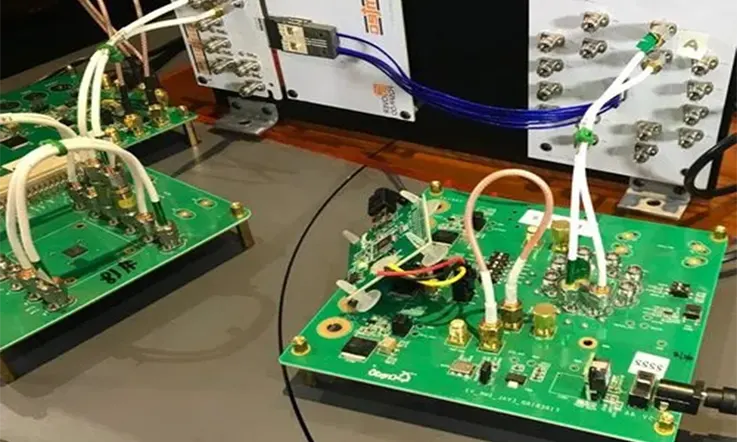
We hope that this article has provided comprehensive insights into wire harness assemblies and addressed most of your inquiries. If you are considering the implementation of a custom wire harness solution and require further clarification, we are here to assist you with the information you require.
Wire Harness vs. Cable Assembly
Cable assembly and wire harness are occasionally mistaken for being identical, owing to their overlapping functionality. This confusion is understandable since professionals often interchangeably use these products, which serve similar basic functions. However, it is important to note that cable assemblies and wire harnesses are distinct from one another.
Though harnesses and assemblies seemingly serve the same purpose (analogous to wires and cables), their differentiation lies in their capabilities.
Wire Harnesses
Wire harnesses consist of a collection of individually sheathed wires that are grouped together to create a cohesive unit. This assemblage of wires serves the purpose of providing electrical connectivity while ensuring the organization of electrical components. Wire harnesses are particularly advantageous in situations where space is limited, although they also find applications in large-scale systems. One key benefit of utilizing wire harnesses is their ease of installation. Instead of individually routing multiple single wires throughout a system, harnesses consolidate the wires, allowing for simultaneous routing to streamline the process and mitigate the occurrence of human errors.
Cable Assemblies
A cable assembly refers to the consolidation of multiple cables or wires that are intricately braided and enveloped within a single safeguarding sheath, resulting in a unified assembly. Similar to wire harnesses, cable assemblies offer electrical connectivity while effectively organizing wires and cables. However, their primary purpose is to afford protection to the internal wires and cables against various mechanical and environmental elements.
The exterior appearance of a cable assembly exhibits a straightforward design, featuring a robust thermoplastic material. This outer layer serves as a shield, guarding the internal components from application-specific demands, such as extreme temperatures, friction, vibrations, weather conditions, chemical exposure, UV radiation, strain, and other environmental and mechanical factors.
To ensure the suitability of a cable assembly for the intended application environment, most manufacturers provide a range of readily available solutions, as well as considerable flexibility for customization and design. While this may entail initial investment costs, the return on investment is swiftly realized through enhanced performance, heightened reliability, and prolonged lifespan of the cable assembly solution.
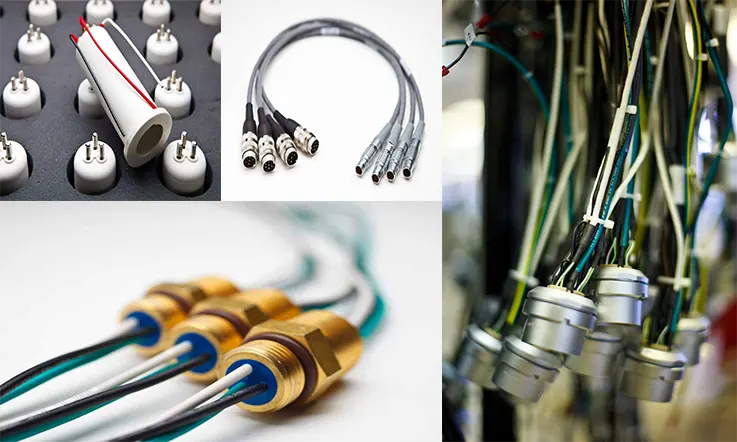
Cable & Wire Harness Assembly Benefits
In various industries, the organization of wires and cables connected to electrical devices is of utmost importance, and wire harnesses and cable assemblies play a critical role in achieving this organization effectively.
Many Prominent wire harness manufacturers can offer custom-made wire and cable harness assemblies based on customer specifications, resulting in saved time and improved organization.
Wire and cable harness assemblies deliver numerous benefits, including:
Reduced installation time: Vehicles, for example, often require extensive wiring. Wire harness assemblies simplify the manufacturing process by integrating all the necessary wires and cables into a single unit. Installation then becomes a straightforward task of incorporating the harness, eliminating the need for individual wire routing.
Enhanced security and safety: Binding wires and cables within a harness increases the overall stability and protection against vibrations, abrasions, and moisture. Optimal space utilization and the absence of flexing in a bundled configuration reduce the risk of electrical shorts. Moreover, using flame-retardant sleeves further diminishes the likelihood of electrical fires.
Lower cable installation costs: The use of cable harnesses and assemblies can improve cable installation efficiency, resulting in cost savings.
Improved system performance & reliability: Implementing cable assemblies and wire harnesses enhances system performance and reliability. They offer superior protection to wires against harsh external factors commonly encountered in various environments.
Weight and space savings: Cable harnesses and assemblies contribute to reduced weight and space requirements by facilitating cable organization and consolidation.
Enhanced safety: Wire and cable harness assemblies eliminate the risk of tangled and exposed wires, thereby improving overall safety. Inspection procedures are also simplified through the utilization of organized harness configurations.
By leveraging wire harnesses and cable assemblies, industries can benefit from improved productivity, cost-efficiency, system performance, and safety in their electrical installations.
Wire Harness assembly & Cable Harness Assembly Services
With over two decades of experience serving global high-tech customers, JarnisTech is a trusted provider of premium custom cable and harness assemblies. Our commitment to delivering the highest quality products sets us apart.
At JarnisTech, we offer discrete cable and harness assemblies for various cable types, including flat ribbon cables, RF cables, fiber optic cables, and multi-conductor cables. Our extensive range of processes, such as manufacturing, ultrasonic welding, and injection molding, ensures that we deliver exceptional products and services.
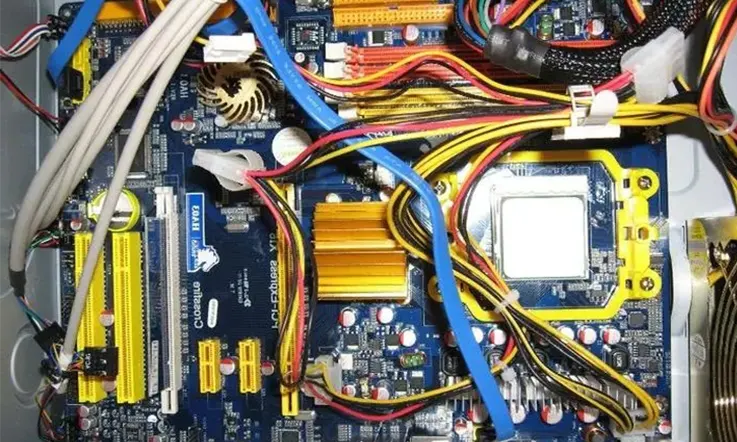
As a turnkey solution provider, JarnisTech caters to mid-scale prototypes, offering a comprehensive cable and harness assembly service. Our focus on fast delivery, efficient component sourcing, precise assembly, and 100% continuity testing ensures that our customers receive top-notch solutions.
Our dedicated team is equipped to provide real-time and efficient communication, ensuring smooth execution and handling of any engineering change orders (ECOs) that may arise during the cable assembly process. We prioritize effective collaboration and clear communication channels to guarantee customer satisfaction.
Why Choose Us ?
Design and Engineering: At JarnisTech, we leverage AutoCAD to develop product concepts and create assembly layouts, allowing us to envision and refine designs effectively. Additionally, we offer prototype development services to address any unforeseen challenges that may arise during the design phase, ensuring optimal solutions.
Component Sourcing: With an extensive supplier network, JarnisTech excels in sourcing high-quality components at competitive prices. Our streamlined procurement process and strong relationships with trusted suppliers enable us to obtain the best components for your project.
Cable & Wire Harness Assembly: Equipped with advanced technology and a team of highly skilled engineers and production staff, we specialize in the assembly of diverse cable and wire harness configurations. From straightforward to intricate designs, we have the expertise and capabilities to deliver exceptional results.
Testing and Inspection: Quality is paramount at JarnisTech, which is why we provide reliable testing services to ensure the functionality and reliability of our cable and wire harness assemblies. Our testing capabilities include comprehensive assessments such as 100% continuity testing, break testing, custom harness fixtures for production testing, resistance testing for multiple harness combinations, and withstand voltage testing.
Future Trends and Innovations in Cable and Wire Harness Assembly
Future trends and innovations in cable and wire harness assembly are driven by advancements in technology and evolving industry demands. Here are some notable trends to keep an eye on:
High-Speed and Fiber Optic Wiring: With the increasing need for high-speed data transmission, there is a shift towards using fiber optic cables and high-frequency wiring in cable and wire harnesses. These technologies offer greater bandwidth, signal integrity, and immunity to electromagnetic interference.
Smart Harnesses and Integrated Electronics: The integration of electronics directly into cable and wire harnesses enables additional functionalities and intelligence. Smart harnesses may include sensors, microcontrollers, and communication interfaces to monitor and control various parameters, enhancing efficiency and diagnostics.
Industry 4.0 and Automation: The adoption of Industry 4.0 principles, such as digitalization, automation, and connectivity, is revolutionizing cable and wire harness assembly. Automation technologies like robotic assembly, computer-aided design, and augmented reality-based instructions are improving production efficiency and quality control.
Advanced Testing and Quality Assurance: Quality control and testing of cable and wire harnesses are becoming more sophisticated. Advanced testing methods, such as automated testing systems, in-line inspection, and functional testing, ensure the reliability and performance of the assembled products.
Wirelessly Powered and Connected Harnesses: Wireless power transfer and wireless communication technologies are being explored to eliminate physical wires in certain applications. These wireless harnesses can transmit power and data without the need for conventional cables, reducing weight and complexity.
Predictive Maintenance and Condition Monitoring: The integration of sensors and data analytics in cable and wire harnesses allows for predictive maintenance and condition monitoring. Real-time monitoring of parameters like temperature, vibration, and current draw can help identify potential failures before they occur, enhancing reliability and reducing downtime.
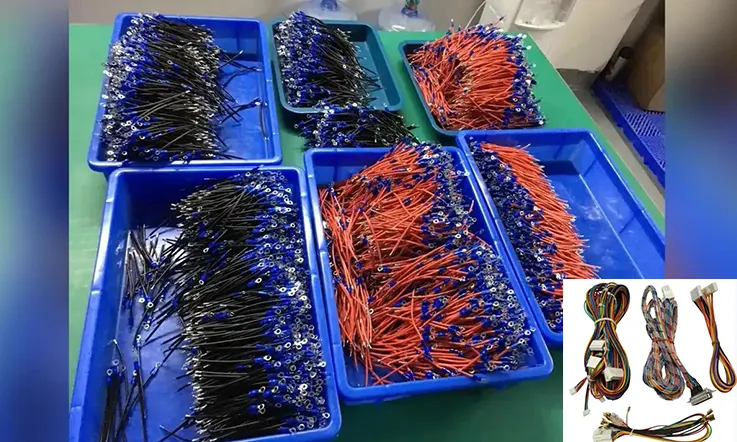
These are just a few trends shaping the future of cable and wire harness assembly. As technology continues to advance, we can expect further innovation and advancements in this field.
Summary
The future of cable and wire harness assembly is driven by technological advancements, evolving industry needs, and the pursuit of enhanced performance, reliability, and efficiency. As these trends continue to develop, we can expect further innovations in the field, enabling the creation of more advanced and sophisticated electrical systems in various applications.
Related Posts:
- Mixed PCB Assembly Technology Services For Your Next New Project
- Why Electronic Potting is So Important in PCB Assembly?
- A Full Guide to Electro mechanical Assemblies
- What Is Printed Circuit Boards Assembly?
- Electronics Components PCB Assembly
- China:The Best PCB Consignment Assembly Services At JarnisTech
- PCB Box Build Assembly
- Nine Method of Save Cost PCB Assembly Production
- How Many Types of Turnkey PCB Assembly?