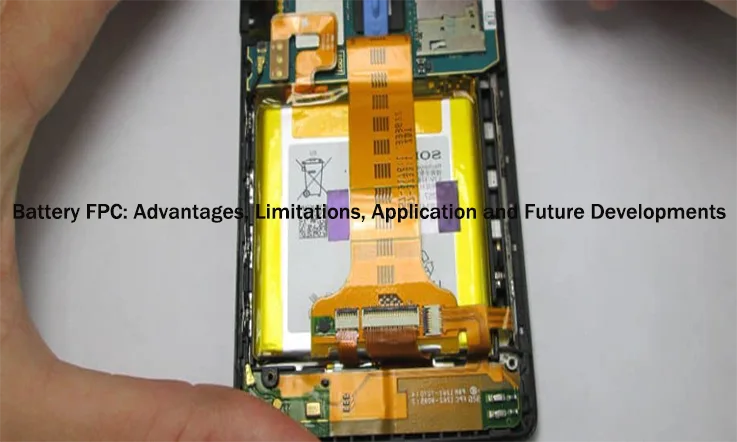
As the popularity and demand for wearable and mobile devices escalate, the necessity for flexible printed circuit (FPC) solutions grows as well – solutions capable of supporting increased current draw operations, such as brighter displays. Yet, this requirement for advanced performance is directly at odds with the progression towards more compact, lightweight devices, which necessitates the use of increasingly smaller, lighter batteries.
To meet the needs of these increasingly complex devices, the connector between the circuit board and battery must be both small in size and able to conduct greater currents. This poses a major difficulty for FPC designers who have to reconcile the competing needs of performance, size, and weight to engineer a solution that addresses market demands. Observing the market’s progression, it’s intriguing to anticipate how FPC technology will adapt to these challenges and persist in spearheading innovation in the wearable and mobile device sector.
In this article we’ll delve into the world of Battery FPC understanding their functionality, benefits, drawbacks and looking ahead to where they might be headed in terms of applications and advancements.
What is a Battery FPC?
Battery FPC, the abbreviation for Battery Flexible Printed Circuit, it is a flexible electronic circuit utilized for linking a battery to the accompanying electronic elements within an apparatus. The design philosophy behind the Battery FPC incorporates thinness, lightness and flexibility, typically making it a perfect fit for devices demanding a compact yet resilient source of power.
Unlike traditional rigid circuit boards, Battery FPC can be bent and curved to fit into tight spaces. This characteristic is vital for devices of unconventional shapes or dimensions. Furthermore, Battery FPC can be specifically tailored to address the explicit requirements of a particular device, allowing for greater design flexibility and improved performance.
What is FPC?
FPC stands for Flexible Printed Circuit. This denotes an electronic circuit constructed from thin, flexible materials, commonly a solitary polymer film or a composite of multiple polymer film layers. FPC are strategically engineered to serve as substitutes for conventional Rigid PCB circuit boards in particular applications, where properties such as lightweight, flexibility and space conservation are requisites.
FPC are composed of conductive pathways and pads meticulously etched onto a malleable substrate’s surface, typically fashioned from polyimide or polyester. These pathways and pads form the indispensable electrical linkages between distinct electronic constituents, encompassing integrated circuits (ICs), resistors, capacitors, and LEDs.
FPC can be manufactured in various shapes and sizes, depending on the requirements of the application. They may manifest as single layer, double layer and multi-layer, brandishing diverse thicknesses and copper weights. Their design can also incorporate a variety of connectors such as Zero Insertion Force (ZIF) and Flat Flexible Cable(FFC), or specific FPC connectors.
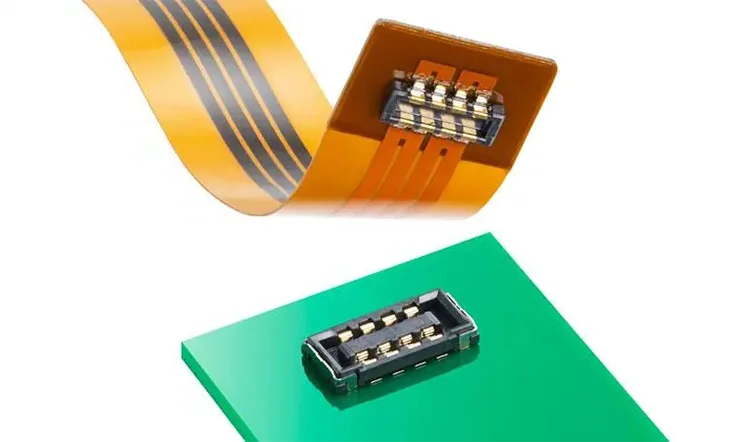
FPC are widely used in electronic devices that require flexibility, durability, and miniaturization, such as a broad spectrum of devices like smartphones, laptops, tablets, digital cameras, medical appliances, and car electronic systems. Versus standard rigid circuit boards, FPC present a comprehensive array of benefits such as notable weight diminution, superior resilience to shock and vibration, streamlined assembling and upkeep procedures, along with a heightened degree of design flexibility.
How Does Battery FPC Work?
Battery FPC works by connecting a battery to other electronic components in a device using a flexible printed circuit. Engineered for thinness, lightweight, and flexibility, the Battery FPC caters ideally to apparatuses necessitating compact and robust power solutions.
The Battery FPC consists of a thin layer of flexible substrate, such as polyimide or polyester, with conductive traces and pads etched onto its surface. These conductive routes are made from copper or comparable conductive resources, facilitating the inception of electrical connections amid the battery and ensuing electronic components integrated in the gadget.
The Battery FPC is linked to the battery via a specific connector type, commonly a JST connector or an FFC/FPC connector. Possessing customizable features, the Battery FPC can be tailored to accommodate the unique requirements of the device, offering varied shapes, sizes, and thicknesses to support diverse battery dimensions and arrangements.
Upon connection of the Battery FPC to the battery, it can be unified with additional electronic constituents within the device, including microcontrollers, sensors, displays, and actuators. Category-defining characteristics of the Battery FPC, such as its ability to be contorted and curved to slot into compact zones, render it a superb choice for appliances characterized by non-standard shapes or magnitudes.
In essence, the Battery FPC functions by establishing a flexible and dependable linkage between a battery and various electronic entities within a device, allowing for greater design flexibility and improved performance.
Advantages of Battery FPC
Flexibility: Among the paramount benefits of Battery FPC is its Flexibility. It can be bent, twisted, and shaped to fit into tight spaces and conform to the shape of the device, it stands as an optimal solution for apparatuses necessitating a compact and flexible power source.
Lightweight: Battery FPC is much lighter than traditional rigid circuit boards and other types of battery connections, making it an excellent option for devices that require lightweight components, such as portable electronics and wearable devices.
Reliability: The Battery FPC is skillfully designed to deliver high reliability. It has limited connective junctures and eliminates the existence of movable components, effectively diminishing the probability of malfunction while enhancing the device’s comprehensive performance.
Enhanced Resilience to Shock and Oscillation: The Battery FPC exhibits a greater resistance to shock and vibration compared to the conventional rigid circuit boards, which are susceptible to fissures or fractures under strain. Consequently, This makes it an excellent option for devices that are subject to frequent movement or impact, such as automotive electronics and industrial equipment.
Simplified Assembly and Maintenance: The implementation of Battery FPC during the assembly process can be effortlessly achieved, curtailing both time and production costs. In addition, it can be conveniently substituted or mended if required, thus enhancing the device’s comprehensive maintenance.
Increased Design Flexibility: The Battery FPC offers customization to cater to the distinct requirements of the device, with a variety of shapes, sizes, and thicknesses available to accommodate diverse battery sizes and configurations. This yields greater design flexibility and uplifts the performance.
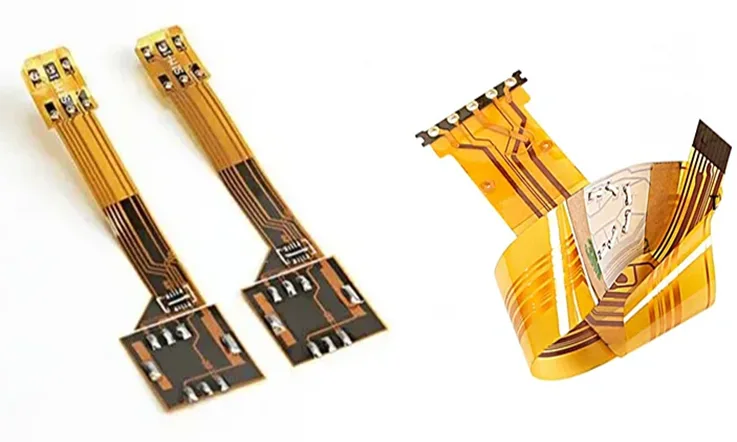
Limitations of Battery FPC
Production Expense: Manufacturing Battery FPC may be costlier compared to conventional rigid circuit boards, consequently raising the overall device expenditure.
Restrained Current Capacity: Battery FPC exhibits a limited current capacity, thereby implying that it might not be apt for devices demanding high power output or swift charging.
Constrained Temperature Tolerance: Battery FPC may feature a restricted temperature range that could potentially influence its performance under severe temperatures or in harsh conditions.
Finite Durability: Despite Battery FPC being sturdier than traditional rigid circuit boards, it could still succumb to wear and tear over duration, particularly in high-stress situations.
Design Intricacy: Crafting the Battery FPC is likely to be more intricate as compared to traditional rigid circuit boards, necessitating particular expertise and specific equipment for manufacturing and assembly.
Limited Compatibility: Battery FPC may not be fully compatible with all battery types or connectors, thus impeding its application in certain scenarios.
Applications of Battery FPC
Battery FPC is leveraged across an extensive array of electronic apparatuses, wherein attributes such as flexibility, light-weightedness, and economization of space are requisites. Following are some prevalent use-cases of Battery FPC:
● Portable Electronic Devices
● Healthcare Equipment
● Automobile Electronics
● Industrial equipment
● Home Electronic Products
● Defense and Space Equipment
What are the Differences Between FFC and Battery FPC?
Both FFC (Flexible Flat Cable) and Battery FPC (Flexible Printed Circuit) are types of flexible circuits implemented to create connections amongst electronic components inside a device. Nevertheless, significant distinctions exist between these two types.
Structure: FFC is characterized by a series of conductive wires that are encapsulated between two layers of pliable insulating material, forming a flat-type cable. In contrast, Battery FPC constitutes a flex PCB circuit board comprising a thin substrate layer onto which conductive paths and pads are meticulously etched.
Functionality: FFC primary role is to establish connections between electronic components within an apparatus, such as flat panel displays or touchscreens. Conversely, Battery FPC has a more specific purpose, which is to facilitate a connection between a battery and other constituent electronic components within an instrument.
Flexibility: While both FFC and Battery FPC possess flexibility, Battery FPC generally showcases greater pliability and robustness, attributed to its thin substrate material and carefully etched conductive traces.
Thickness: Conventionally, FFC exhibits a greater thickness compared to Battery FPC because of its composite layers of insulating material and conductive wires. Owing to its slimmer profile, Battery FPC becomes a preferred choice for devices with space constraints.
Connector Type: The FFC generally employs a ZIF (Zero Insertion Force) connector, whereas Battery FPC tends to utilize JST connector or standard FFC/FPC connector.
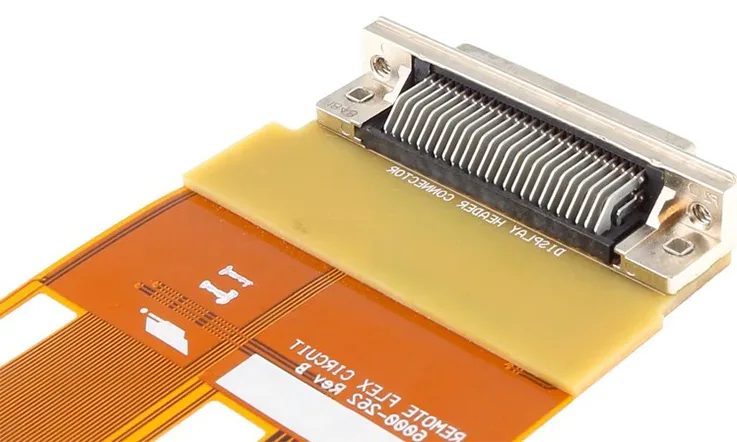
Therefore, despite the fact that both FFC and Battery FPC are types of flexible circuits utilized for the integration of electronic components within an apparatus, distinctions are evident in their fabrication, functionality, flexibility, thickness and connector style. FFC is chiefly employed for electronic component linkage, whereas Battery FPC is designed expressly for establishing a connection between a battery and other electronic components. Typically, Battery FPC exhibits superior flexibility, is thinner and features a unique connector in comparison to FFC.
Future of Battery FPC
The outlook for Battery FPC appears to be vibrant, with ongoing evolvement and advancements in the sphere of pliable electronics. Allow me to present some prospective progressions for Battery FPC:
1. Increased Power Capacity: One crucial arena of consideration for Battery FPC is augmenting its power holding capability, fulfilling the rising requirement for devices with robust power. This could involve using new materials or developing new manufacturing processes to improve the conductivity and current-carrying capacity of Battery FPC.
2. Improved Durability: Another area of focus for Battery FPC is improving its durability and resistance to wear and tear. This could involve the generation of new materials or coverings that provide superior shielding from environmental elements like moisture, heat, and UV radiation.
3. Integration with Other Flexible Electronics: Battery FPC could feasibly amalgamate with diverse types of flexible electronics, including sensors, displays, and memory equipment, giving rise to entirely flexible systems. This could pave the way to unparalleled possibilities in wearable technology, medical implants, and an expanse of other applications.
4. Development of New Applications: Pursuant to the ongoing evolution of Battery FPC technology, the emergence of new applications and markets is quite probable. To illustrate, Battery FPC could find usage in the formulation of robotics, intelligent fabrics, or flexible solar cells.
5. Increased Manufacturing Efficiency: The development of new manufacturing processes and materials could improve the efficiency and cost-effectiveness of producing Battery FPC. This could make it more accessible to a wider range of industries and applications.
In summary, the future of Battery FPC looks bright, with potential for increased power capacity, improved durability, integration with other flexible electronics, development of new applications, and increased manufacturing efficiency. Such advancements could serve as catalysts for innovation and expansion across various sectors, thereby reinforcing the position of Battery FPC as a crucial element in the future landscape of flexible electronics.
Conclusion
Battery FPC is a type of flexible printed circuit, is specifically engineered to establish a connection between a battery and other electronic elements within a device. Compared to conventional rigid circuit boards, Battery FPC offer many benefits. These include its flexibility, capability for space optimization, elevated reliability, customizability, decreased assembly duration and costs and enhanced performance. Battery FPC finds a spectrum of uses in numerous electronic devices, spanning everything from handheld electronics and medical equipment to automotive and industrial applications.
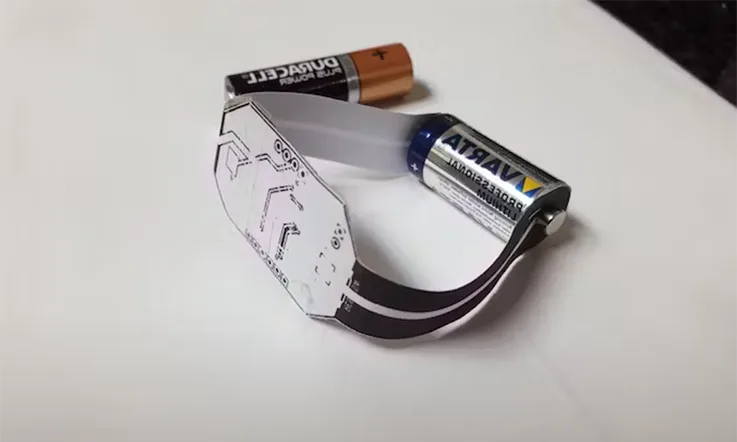
While Battery FPC has some limitations, including cost and limited current capacity, its potential for increased power capacity, improved durability, integration with other flexible electronics, development of new applications, and increased manufacturing efficiency make it an essential component in the future of flexible electronics.
With the relentless progression of technology and the advent of novel applications for flexible electronics, Battery FPC is poised to assume a progressively significant function in energizing future devices and systems. Its inherent flexibility, durability and customization capabilities render it a supremely fitting solution for a multitude of applications. Furthermore, its capacity for innovation and growth puts it in the spotlight as a fascinating field to monitor closely.
Related Posts:
1. Oshpark PCBs for Optimal Solutions
2. Flex PCB
3. FPC Circuit Board Materials and Application
4. What Is the Main Differences Between FFC and FPC?
5. Understanding Kapton PCB: Advantages, Challenges, and Applications