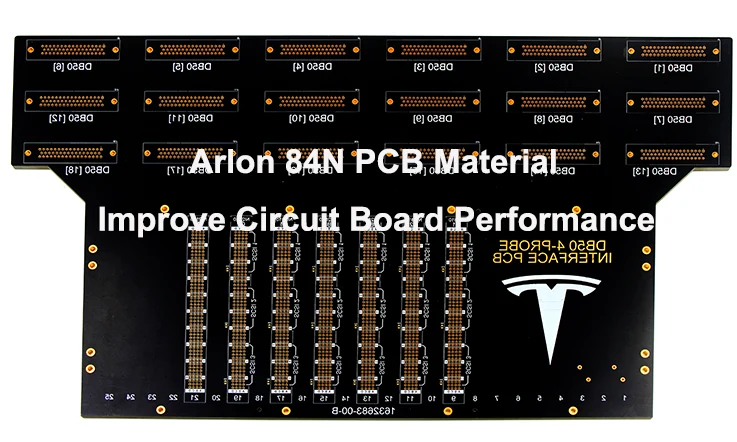
In industries where PCB reliability can’t be left to chance, material selection is a major factor in ensuring performance and longevity. Arlon 84N, a polyimide-based dielectric, offers exceptional thermal stability, mechanical durability, and electrical consistency, making it a strong contender for applications in aerospace, telecommunications, military electronics, RF, microwave, and 5G infrastructure.
Compared to FR4, Arlon 84N withstands extreme temperatures, minimizes signal loss, and resists delamination in multilayer designs. It also stacks up well against other high-performance materials like Arlon 85N, Rogers, and Isola, making it a reliable option for hybrid RF stackups, high-frequency circuits, and demanding environmental conditions.
This article explores the processing and fabrication guidelines for Arlon 84N, best practices for PCB stackup design, and its performance in RF, microwave, and high-speed digital applications. For those seeking a material that withstands thermal stress, preserves signal integrity, and ensures long-term durability in environments, Arlon 84N deserves a closer examination.
What is Arlon 84N?
Exploring the Core Features of This High-Performance PCB Material
Arlon 84N is a polyimide-based PCB laminate designed for use in advanced electronics. This material is recognized for its remarkable performance in environments with extreme temperature variations, low dielectric loss, and high mechanical strength. It’s engineered to meet the demands of high-frequency circuits that operate under challenging conditions. Let’s take a closer look at what Arlon 84N brings to the table for those working with high-reliability applications.
Arlon 84N Material Composition
The Science Behind Its Strength
Arlon 84N is based on a polyimide resin system combined with glass-reinforced fillers to offer enhanced mechanical properties and thermal stability. Polyimide, known for its resistance to high temperatures and chemical durability, forms the backbone of this material’s structure. This resin system provides thermal endurance while keeping performance consistent in environments with rapid temperature shifts.
The glass reinforcement contributes to the laminate’s rigidity, making it more resilient under mechanical stress, especially in environments where high-frequency signals are a priority. The material’s combination of thermal resistance and mechanical strength is a factor in its ability to function effectively in high-demand applications.
How Arlon 84N Improves PCB Reliability in High-Stress Environments?
Electronics used in fields like military, aerospace, and telecommunications often encounter extreme temperature changes, vibrations, and thermal cycling. These stresses can weaken standard PCB materials, leading to performance issues or even failure.
However, Arlon 84N stands up to these challenges by offering better resistance to thermal cycling and mechanical deformation compared to traditional materials like FR4. As its low coefficient of thermal expansion (CTE), it experiences less expansion or contraction when exposed to temperature shifts, reducing the chances of delamination and other physical breakdowns.
In addition, Arlon 84N maintains signal integrity in high-frequency applications, making it a reliable material for advanced communication systems that need to operate consistently under challenging conditions.
Why Arlon 84N Outperforms Standard PCB Laminates Like FR4 & Rogers?
When you compare Arlon 84N with other commonly used laminates like FR4 and Rogers, it’s clear that Arlon 84N provides several advantages in high-performance applications. While FR4 is widely used for everyday electronics, it doesn’t perform as well in high-frequency circuits or environments that require thermal stability.
FR4 may be effective for simpler designs, but it’s prone to signal loss in high-frequency environments and can suffer from thermal expansion issues. On the other hand, Rogers laminates offer low dielectric constants, but they do not match the thermal stability and mechanical strength of Arlon 84N. In environments that demand consistent performance despite temperature fluctuations, Arlon 84N provides better resistance to thermal cycling and higher mechanical durability, giving it a distinct edge in main applications.
For those designing high-frequency circuits or systems that need to operate in high-stress conditions, Arlon 84N provides a dependable alternative to FR4 and Rogers, making it a reliable material for us focused on long-term reliability and performance.
Benefits of Arlon 84N for High-Reliability PCB Manufacturing
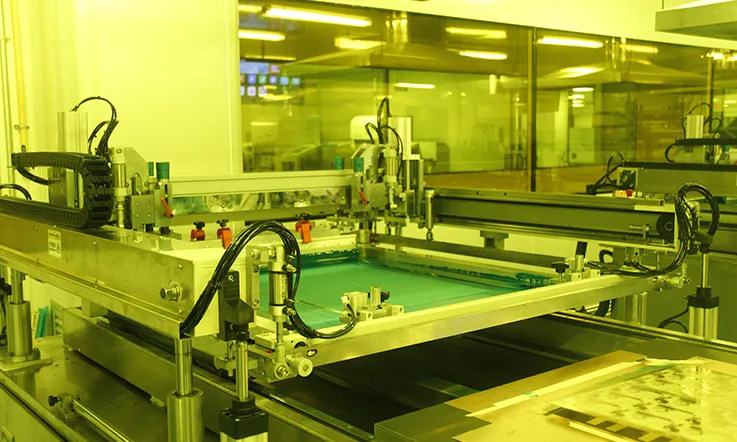
When designing PCBs for industries such as aerospace, telecommunications, and military applications, materials that can withstand demanding conditions are needed. Arlon 84N is made to operate effectively in tough environments. This material is used in sectors where durability and consistent performance are required. Let’s explore how Arlon 84N fits into high-performance PCB manufacturing.
Arlon 84N’s Exceptional Thermal Stability for Extreme Environments
Arlon 84N is designed to offer excellent thermal stability, making it suitable for extreme temperature conditions. It functions within a temperature range of -40°C to 200°C, and its polyimide resin system allows it to endure environments that would affect other materials.
The material continues to perform reliably when exposed to significant temperature shifts, which is particularly useful for high-frequency circuits in telecommunications systems or aerospace electronics. Arlon 84N ensures steady operation even in environments with substantial temperature changes.
Thermal Performance Comparison Table-
Property | Arlon 84N | FR4 Standard PCB | High-Tg FR4 |
Glass Transition (Tg) | 250°C | 130-150°C | 170-180°C |
Decomposition Temp. | 400°C | 260°C | 300°C |
Thermal Conductivity | 0.25 W/m·K | 0.20 W/m·K | 0.23 W/m·K |
Operating Range | -40°C to 200°C | -10°C to 130°C | -20°C to 160°C |
With Arlon 84N, thermal expansion and contraction issues are minimized, ensuring long-term reliability even in high-temperature or high-power electronics.
The Electrical Performance of Arlon 84N for RF and High-Frequency PCBs
For those working with RF and high-frequency circuits, Arlon 84N provides exceptional electrical performance. With a low dielectric constant and low loss tangent, signal integrity is maintained at high frequencies, making it a suitable material for RF PCBs used in telecommunication devices, radar systems, and other high-frequency applications.
Compared to traditional laminates like FR4, which often experience signal degradation in high-frequency environments, Arlon 84N minimizes signal loss and maintains clear performance at higher speeds. This makes it suitable for multilayer PCBs and complex RF circuits, where signal clarity remains consistent.
Electrical Properties Comparison Table-
Property | Arlon 84N | FR4 Standard PCB | Rogers 4000 Series |
Dielectric Constant (Dk) @ 10GHz | 3.9 | 4.5-4.7 | 3.6-3.7 |
Dissipation Factor (Df) @ 10GHz | 0.004 | 0.020-0.025 | 0.002-0.004 |
Surface Resistivity (Ω/sq) | 1 × 10⁹ | 10⁶ – 10⁷ | 10⁸ – 10⁹ |
Volume Resistivity (Ω·cm) | 1 × 10¹⁰ | 10⁶ – 10⁸ | 10⁹ – 10¹⁰ |
Mechanical Strength & Low Z-Axis Expansion of Arlon 84N for Multilayer PCBs
In multilayer PCBs, mechanical strength is necessary to ensure the board can withstand physical stress while maintaining its structure. Arlon 84N provides solid mechanical properties, resisting warping, bending, and delamination.
A notable feature of Arlon 84N is its low Z-axis expansion, which ensures that the material remains stable under thermal cycling. Thanks to its low coefficient of thermal expansion (CTE), it does not expand or contract excessively with temperature variations, reducing the risk of delamination in multilayer PCB designs.
In industries like military electronics, space applications, and high-performance communication systems, Arlon 84N maintains durability and reliability in the face of mechanical stress and temperature variations, ensuring the continued stability of multilayer PCBs.
Mechanical Properties Comparison Table-
Property | Arlon 84N | FR4 Standard PCB | Polyimide Competitor |
Tensile Strength (MPa) | 150 | 90-120 | 140 |
Flexural Strength (MPa) | 350 | 300-320 | 340 |
Z-Axis Expansion (50-250°C) | 1.8% | 3.5-4.0% | 2.0% |
CTE (Coefficient of Thermal Expansion) X/Y | 10-12 ppm/°C | 15-17 ppm/°C | 11-13 ppm/°C |
With its low Z-axis expansion, Arlon 84N significantly reduces the risk of thermal stress failures, making it a top choice for multilayer PCBs in high-temperature environments.
Arlon 84N PCB Stackup & Design Considerations for Optimal Performance
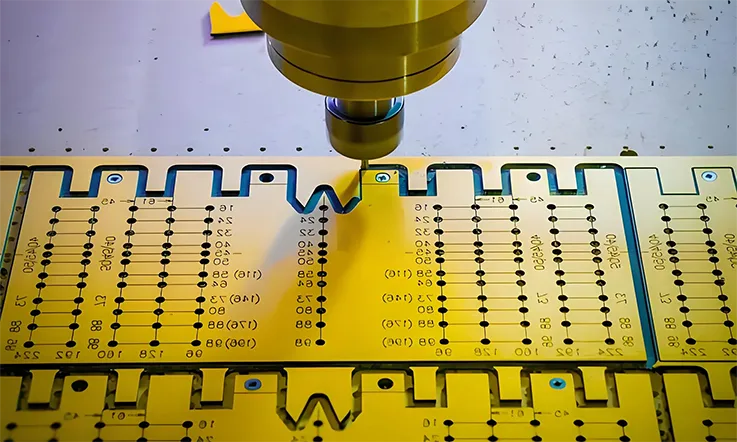
When designing PCBs for applications that need high performance in tough environments, the stackup and layout are essential, especially when using Arlon 84N. This material is chosen for its consistency and long-lasting properties under challenging conditions. Let’s look into the factors that help enhance Arlon 84N designs for reliable performance over time.
Best Practices for Designing PCB Stackups with Arlon 84N
When creating a PCB stackup with Arlon 84N, attention should be given to the thickness of each layer and the material combinations best suited for your application. Arlon 84N is known for its mechanical strength and thermal stability, but a well-designed stackup ensures these characteristics are effectively utilized.
Here are some guidelines for designing stackups with Arlon 84N:
1.Layer Selection: Pair Arlon 84N with materials that match your specific needs, such as PTFE for high-frequency layers and standard laminates for general layers.
2.Thickness Considerations: Pay close attention to the layer thickness in relation to the thermal expansion and electrical performance of each material. This ensures the stackup can handle thermal fluctuations without distortion.
3.High-Frequency Designs: For high-speed signals, focus on creating an arrangement that minimizes interference and maintains signal integrity.
A well-thought-out stackup will prevent potential issues like thermal stress or mechanical failure, ensuring the PCB remains stable under tough conditions.
How to Optimize Arlon 84N PCB Layout for Signal Integrity & EMI Control?
The layout of a PCB using Arlon 84N directly influences performance, especially in high-frequency applications where signal clarity and EMI control need attention. Here’s how to design Arlon 84N-based PCBs for optimal results.
1.Minimize Trace Impedance Variations: Wide and smooth traces help in maintaining signal clarity. Avoid sharp angles to reduce the likelihood of impedance mismatches.
2.Solid Ground Planes: Integrating continuous ground planes reduces the risk of electromagnetic interference (EMI) and provides a stable return path for signals, improving signal fidelity.
3.Impedance Control: For high-speed signals, ensure controlled impedance routing to avoid unwanted reflections and signal loss.
By following these steps, you can prevent signal distortion and minimize the risk of EMI, ensuring that Arlon 84N PCBs perform optimally in complex, high-speed designs.
Hybrid PCB Stackups: Combining Arlon 84N with PTFE & Other Materials
In certain designs, using a hybrid stackup can be beneficial, especially when integrating Arlon 84N with other materials like PTFE. Combining Arlon 84N with PTFE or other high-performance materials allows our designers to tailor the PCB stackup for specific needs, such as RF applications, aerospace, or advanced electronics.
For example, combining Arlon 84N with PTFE offers:
●Enhanced high-frequency performance: PTFE provides low dielectric loss, which is suitable for RF circuits.
●Better thermal management: PTFE’s ability to dissipate heat combined with Arlon 84N’s thermal stability makes this a great option for managing temperature changes.
●Mechanical strength: Arlon 84N contributes strength to the stackup, ensuring the overall PCB stays intact under mechanical stress and temperature fluctuations.
This hybrid approach helps meet complex performance demands, balancing both thermal and electrical needs in high-performance PCB designs.
Arlon 84N vs. Other High-Performance PCB Materials
Choosing the right PCB base material isn’t just about picking a name-brand laminate—it’s about understanding the performance trade-offs for your specific application. Arlon 84N is widely used in aerospace, defense, and RF electronics, but how does it compare to other widely used laminates like FR4, Arlon 85N, and materials from Rogers and Isola?
Arlon 84N vs. FR4 – Why Polyimide Stands Out in High-Reliability Applications?
For engineers familiar with standard FR4, the jump to polyimide-based materials like Arlon 84N can feel like night and day. While FR4 is a economical choice for general-purpose PCBs, it has limitations when exposed to extreme heat, mechanical stress, and high-frequency signals.
Where Arlon 84N Stands Out Against FR4-
●Thermal endurance: Unlike FR4, which begins to struggle beyond 130–150°C, Arlon 84N remains stable even at temperatures exceeding 250°C.
●Mechanical durability: FR4 is prone to delamination during thermal cycling, while Arlon 84N maintains its integrity even through significant temperature fluctuations.
●Signal integrity: For high-frequency circuits, FR4’s dielectric properties can introduce losses, while Arlon 84N maintains a more stable dielectric constant.
Arlon 84N vs. Arlon 85N – Understanding the Differences & Picking the Right Fit
Arlon 84N and Arlon 85N share many similarities, but small differences can have a noticeable impact on PCB performance. Both are polyimide-based, yet Arlon 85N is designed for situations that demand lower moisture absorption and refined electrical characteristics.
How to Decide Between Arlon 84N & Arlon 85N-
●Moisture resistance: If your board will be operating in humid environments or requires tightly controlled electrical performance, Arlon 85N has the edge.
●Processing considerations: Arlon 84N tends to be easier to work with in standard polyimide fabrication processes, while Arlon 85N may require tighter controls.
●Target applications: Arlon 85N is commonly used in RF applications since minor shifts in Dk/Df can influence overall performance.
So, if high-frequency signal integrity is on your priority list, Arlon 85N might be worth considering. But if you need a more general-purpose high-performance polyimide, Arlon 84N is a rock-solid option.
Arlon 84N vs. Rogers & Isola – Finding the Right Material for Your Design Needs?
When working with RF circuits, microwave applications, or high-speed digital PCBs, Rogers and Isola are names that frequently come up alongside Arlon 84N. But which one fits your needs better?
How Arlon 84N Stacks Up Against Rogers & Isola Laminates-
●High-frequency performance: Rogers materials (like RO4350B) are often used in RF and microwave applications due to their low-loss properties, but Arlon 84N holds up well in hybrid stackups where polyimide layers are needed.
●Thermal resilience: Isola laminates, like IS620, offer high Tg values, but Arlon 84N still delivers superior thermal endurance in multi-layer applications.
●Fabrication compatibility: Arlon 84N can integrate smoothly into existing polyimide-based PCB manufacturing processes, making it an easier choice for many PCB manufacturers.
Feature | Arlon 84N | Rogers (e.g., RO4350B) | Isola (e.g., IS620) |
High-Frequency Performance | Reliable for RF applications | Best for low-loss RF & microwave | Optimized for high-speed digital |
Thermal Resilience | Handles extreme heat | Good thermal stability | High-Tg for multi-layer designs |
Fabrication Compatibility | Easily integrated into polyimide-based PCB manufacturing | Requires specialized processing | Varies depending on grade |
If your design involves mixed dielectric layers, hybrid PCB stackups, or a balance between mechanical durability and RF performance, Arlon 84N is a strong contender that shouldn’t be overlooked.
Manufacturing PCBs with Arlon 84N
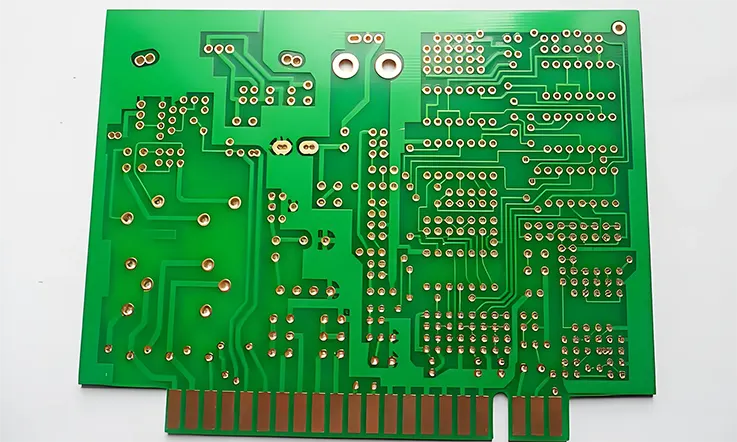
Best Practices for Processing & Fabrication
Bringing Arlon 84N-based circuit boards to life takes more than just slapping some layers together and calling it a day. Polyimide laminates require careful attention at every step, from lamination and curing to drilling and plating. To ensure reliable performance in aerospace, defense, and high-reliability industrial applications, let’s break down how to process Arlon 84N the right way.
Lamination & Curing Guidelines for Arlon 84N-Based PCBs
Polyimide materials like Arlon 84N don’t behave like standard FR4 laminates—they demand a specific approach to achieve proper bonding, void-free lamination, and thermal stability.
Lamination Process-
●Controlled heat-up rate – Rushing the heat-up process can cause resin flow issues and trapped air bubbles, leading to delamination or weak interlayer bonding. A slow ramp-up, typically 2.5–4.5°C per minute, helps maintain uniform resin flow.
●High-pressure requirements – Unlike standard laminates, Arlon 84N benefits from higher lamination pressures, often ranging from 300–500 psi, ensuring strong adhesion between layers.
●Curing protocol – A multi-stage curing profile, typically including a high-temperature post-bake, enhances polyimide cross-linking, which boosts mechanical stability and reduces moisture absorption.
Drilling & Plating Considerations for Arlon 84N Circuit Boards
Drilling polyimide-based PCBs comes with its challenges. The dense fiber structure of Arlon 84N wears down drill bits quickly, and without the right techniques, issues like burrs, resin smear, or inconsistent hole quality can arise.
Optimized Drilling Approach-
●Carbide drill bits with diamond-like coatings – Polyimide materials wear down standard drill bits faster than a road trip on bald tires. Using diamond-coated or premium carbide tools extends tool life and ensures cleaner via formation.
●Controlled drill speeds & entry materials – Excessive RPM can overheat the material, while a slow feed rate helps manage heat buildup.Using entry materials like aluminum helps reduce drill deflection and prevents frayed edges around the holes.
●Desmear & plasma treatment – Polyimide resin smears easily, affecting plated via reliability. A combination of plasma etching and alkaline permanganate treatment ensures clean barrel walls, improving copper adhesion in the plating process.
Managing Thermal Expansion & Stress in Arlon 84N PCB Manufacturing
One thing polyimide laminates don’t forgive easily? Poor thermal management. Arlon 84N’s low Z-axis expansion makes it suited for multilayer PCBs, but it’s still vulnerable to stress buildup if not handled correctly.
Techniques for Reducing Thermal Stress-
●Balanced stackup design – Uneven material distribution can turn a PCB into a banana when exposed to heat cycles. Keeping symmetrical layer construction prevents warpage and stress fractures over time.
●Gradual thermal cycling – Instead of throwing the PCB straight into high-temperature reflow, a controlled pre-bake process helps release trapped moisture and reduces outgassing risks.
●Proper copper-to-substrate ratio – Excessive copper weight variation across the board can lead to localized expansion mismatches. Keeping a uniform copper distribution minimizes stress during operation.
Arlon 84N for RF, Microwave, and 5G Applications
Maximizing Signal Performance at High Frequencies
As RF, microwave, and 5G technologies push the limits of wireless communication, the demand for low-loss, high-reliability PCB materials is stronger than ever. Arlon 84N, a polyimide-based dielectric, offers exceptional stability in high-frequency applications, making it a solid choice for base stations, radar systems, and satellite communications.
Arlon 84N’s Low-Loss Dielectric Properties for High-Speed Digital Circuits
High-speed RF and microwave circuits demand a material that keeps signal loss in check while maintaining consistent impedance across a wide frequency range. Arlon 84N delivers exactly that, thanks to its low dissipation factor (Df) and stable dielectric constant (Dk).
What Makes Arlon 84N a Strong Contender for RF Boards-
Feature | Arlon 84N | Standard FR4 |
Dissipation Factor (Df) | 0.004 – 0.006 @ 10 GHz | 0.02+ @ 10 GHz |
Dielectric Constant (Dk) | 4.2 (stable across temperatures) | Varies with heat |
Moisture Absorption | ≤ 0.5% | 1% – 2% |
●Minimal signal attenuation – With a low-loss dielectric, Arlon 84N reduces energy dissipation, keeping RF signals crisp and interference-free.
●Consistent Dk across temperature swings –Some PCB materials experience dielectric shifts under heat, causing impedance mismatches. Arlon 84N maintains stability, ensuring consistent signal performance.
●Less moisture absorption – High humidity can throw RF performance out of whack. Arlon 84N’s low moisture uptake ensures stable electrical properties, even in challenging environments.
Hybrid RF PCB Stackups
Blending Arlon 84N with PTFE & Ceramic-Based Materials
RF PCB design requires a tailored approach. Many high-frequency systems require hybrid stackups, where Arlon 84N is combined with PTFE, ceramic-filled laminates, or other specialized dielectrics to balance thermal performance, mechanical strength, and signal integrity.
How Hybrid Stackups Improve RF PCB Performance-
Feature | PTFE-Based Laminates | Arlon 84N | Ceramic-Filled Substrates |
Loss Tangent | 0.001 – 0.003 @ 10 GHz | 0.004 – 0.006 | 0.002 – 0.005 |
Thermal Conductivity | Moderate | Good | Excellent |
Mechanical Strength | Low | High | Very High |
●PTFE layers for ultra-low-loss performance – PTFE-based laminates (like Rogers or Taconic materials) help cut down signal loss, while Arlon 84N adds structural strength and thermal stability.
●Ceramic-filled substrates for better thermal dissipation – Some RF power amplifiers and phased-array radar systems generate serious heat. Blending Arlon 84N with ceramic materials helps dissipate heat efficiently without compromising mechanical strength.
●Layer bonding challenges – Not all laminates play nicely together. Choosing compatible prepregs is necessary to prevent delamination and ensure long-term durability.
Why Arlon 84N Stands Out in 5G Base Stations & Antenna Modules?
The 5G rollout demands high-frequency performance with minimal signal degradation, especially in antenna arrays, power amplifiers, and mmWave modules. Arlon 84N’s thermal resilience and electrical consistency make it a strong candidate for these demanding applications.
What Makes Arlon 84N a Good Fit for 5G Infrastructure-
Feature | Arlon 84N | Standard PCB Materials |
Max Operating Temp | 250°C+ | 130–150°C |
Phase Stability | Excellent | Moderate |
Resistance to Moisture | High | Low to Moderate |
●Handles higher temperatures – 5G base stations and RF power circuits get hot, especially in dense urban deployments. Arlon 84N keeps its shape and electrical properties intact, even in high-power RF conditions.
●Minimizes phase distortion – In mmWave applications, even slight changes in material properties can skew signal phase alignment, reducing network efficiency. Arlon 84N offers consistent phase response, a must for beamforming antenna arrays.
●Reliable in outdoor deployments – Rain, humidity, and temperature swings can throw off RF board performance. Arlon 84N’s moisture-resistant formulation ensures long-term reliability, even in demanding outdoor conditions.
How Sourcing High-Quality Arlon 84N for Reliable PCB Manufacturing?
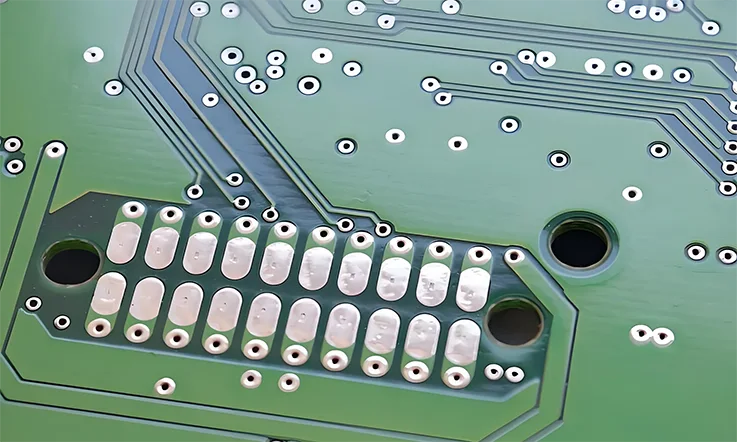
Getting the right polyimide laminate is just as fundamental as dialing in the perfect PCB design. If the material doesn’t meet expectations, your high-layer-count boards might face issues before they even reach full production. Arlon 84N’s polyimide composition requires sourcing from experienced suppliers who are well-versed in high-dependability applications. Below, we outline core factors for selecting a supplier, ensuring compliance with industry standards, and managing costs while maintaining quality.
What to Look for in an Arlon 84N PCB Supplier?
Not all PCB material vendors operate at the same level. When sourcing Arlon 84N laminates and prepregs, asking the right questions up front can help avoid roadblocks down the line.
Core Factors When Evaluating a Supplier-
●Direct sourcing from authorized distributors – Materials should come from reliable sources with full traceability, not third-party resellers with uncertain storage conditions.
●Proper handling and storage – Arlon 84N requires controlled conditions to preserve its performance characteristics. Suppliers should have clear inventory management to prevent selling aged stock.
●Proven expertise in polyimide laminates – Some vendors mainly deal with commodity materials like FR4 and might not fully grasp the processing demands of high-end laminates.
●Certification and documentation – Always request material compliance reports to verify that your laminates meet manufacturer specifications.
Ensuring IPC & MIL Standard Compliance in Arlon 84N Manufacturing
For industries like aerospace, defense, and high-performance electronics, PCB reliability standards aren’t just guidelines—they’re requirements. If your Arlon 84N-based board needs to comply with IPC-6012, IPC-4101, MIL-PRF-31032, or MIL-PRF-50884, it’s worth making sure your fabrication process is in line before production kicks off.
Best Practices for Meeting Compliance Without Unnecessary Delays-
●Partner with a certified PCB manufacturer – Some PCB Laminate factory focus on commercial-grade production and may not have the equipment or experience to process polyimide-based laminates like Arlon 84N to standard.
●Validate materials before manufacturing begins – Assuming all polyimides behave the same is a fast track to unexpected fabrication issues. Arlon 84N has specific lamination, drilling, and plating needs that must be factored in upfront.
●Perform stress and thermal cycle testing – Delamination, copper cracking, and material expansion can be a problem if processing isn’t handled correctly. Thermal stress testing helps catch potential weak points before deployment.
Cost-Effective Strategies for Arlon 84N PCB Production
Building with high-end polyimide laminates doesn’t mean costs have to spiral out of control. The trick is optimizing material usage while maintaining fabrication quality.
Ways to Keep Costs Manageable While Maintaining Performance-
●Strategic layer stackups – Arlon 84N doesn’t have to be used throughout the entire PCB. If only certain layers require its high-temperature resilience, a hybrid stackup with lower-cost core materials can help manage expenses.
●Plan batch production ahead of time – Ordering small quantities on a one-off basis typically costs more than bulk purchasing for multiple production runs.
●Optimize design for manufacturability – Overly complex via structures and extremely tight trace geometries can increase fabrication costs. Keeping manufacturing constraints in mind during design can help avoid unnecessary process steps.
●Reduce yield loss – Polyimide laminates demand specific drilling speeds, controlled plating cycles, and proper press cycles. A poorly optimized process leads to higher scrap rates, which increases overall costs.
Arlon 84N – Frequently Asked Questions (FAQ)
1.Does Arlon 84N require special drilling or deburring techniques?
Yes, due to its hardness, carbide or diamond-coated drills and controlled feed rates are recommended.
2.Is Arlon 84N suitable for HDI (High-Density Interconnect) PCB designs?
Yes, but fine-line etching and laser drilling must be carefully managed due to its material properties.
3.How to evaluate interlayer adhesion in Arlon 84N PCBs?
Peel strength tests and microsection analysis verify bonding integrity.
4.What IPC and MIL specifications does Arlon 84N comply with?
It meets IPC-4101/40/41 and MIL-PRF-31032 standards for high-performance PCBs.
5.How to ensure high-quality plated-through holes (PTH) with Arlon 84N?
Use a desmear process with plasma or permanganate treatment to enhance hole-wall adhesion.
Our services
Arlon PCB Laminate & Materials Series