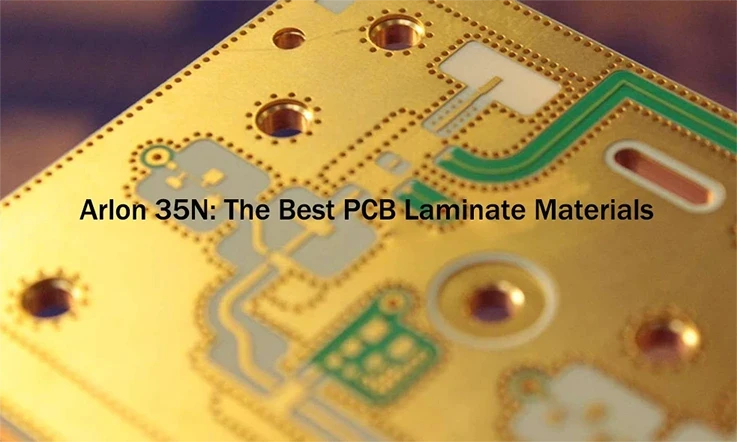
The demands of modern electronics, particularly those used in aerospace, military, and high-frequency applications, are unlike anything the industry has seen before. With components that must withstand extreme conditions—be it temperature fluctuations, intense vibrations, or the pressures of high-frequency signal processing—the materials used to build these systems must be engineered to the highest standards. Enter Arlon 35N PCB laminate: a product that stands at the forefront of these evolving needs, providing solutions for some of the most challenging applications in modern technology.
The Arlon 35N laminate is more than just another PCB material—it’s engineered for extreme conditions, delivering the performance needed in environments where failure isn’t an option. From thermal stability to signal integrity and mechanical durability, it stands out from the crowd. This article will explore why Arlon 35N is quickly becoming the go-to laminate for engineers and manufacturers working on cutting-edge applications.
What Makes Arlon 35N PCB Laminate Superior?
For those designing systems that require both long-lasting performance and consistent reliability, choosing the right PCB material can have a significant impact on the outcome. Here’s an in-depth look at why Arlon 35N PCB Laminate stands out in comparison to other materials.
Why Arlon 35N PCB Laminate Excels in Thermal Stability, Signal Integrity, and Mechanical Durability?
In industries like aerospace and defense, where high-frequency signals are common, the laminate’s ability to withstand heat, maintain signal clarity, and endure mechanical stress makes it suitable. Arlon 35N is engineered to perform effectively in these environments.
It excels in thermal stability—maintaining performance under extreme temperature variations. Whether exposed to high heat or freezing cold, Arlon 35N remains stable, which is particularly useful for applications in aerospace and military systems that face dynamic environmental conditions. Its low dissipation factor (Df) and low dielectric constant (Dk) ensure that signals travel with minimal loss, even at high frequencies, providing clear communication and data transfer without unnecessary interference or degradation.
Overview of Arlon 35N’s Advantages Over Standard PCB Materials Like FR4
While FR4 remains one of the most common PCB materials used in general electronics, its limitations become clear when dealing with high-frequency applications. Unlike FR4, Arlon 35N offers lower signal loss and better thermal management, making it a good choice for industries that demand more from their PCB material.
Here’s a quick comparison:
Property | FR4 | Arlon 35N |
Dielectric Constant (Dk) | 4.4 (higher) | 3.5 (lower) |
Dissipation Factor (Df) | Higher signal loss | Low signal attenuation |
Thermal Stability | Less stable under extreme conditions | Exceptionally stable, handles wide temperature ranges |
Signal Integrity | Suffers at high frequencies | Maintains excellent signal quality at high frequencies |
As shown in the table, Arlon 35N offers better performance in signal integrity and thermal stability, making it a reliable choice for aerospace, military, and high-speed communications.
The Composition of Arlon 35N PCB Laminate
To truly appreciate the performance of Arlon 35N PCB Laminate, it’s important to understand the materials that make it exceptional. Here’s a deeper look at the laminate’s composition and how it helps achieve superior performance in high-stakes environments.
In-depth Breakdown of Fiberglass and Epoxy Resin Composition
The material comprises fiberglass and epoxy resin, two components that are bonded to create a laminate that excels in demanding applications. Fiberglass provides structural strength, while epoxy resin ensures that the laminate performs well under both electrical and thermal stress. This composition allows Arlon 35N to retain its structural integrity and high performance, even in high-frequency, high-temperature environments.
The combination of these materials delivers strength and durability, ensuring the laminate can withstand the mechanical stresses that arise in demanding applications, such as military defense systems and satellite electronics.
Electrical and Thermal Performance of Arlon 35N PCB Laminate and Its Suitability for High-Frequency Applications
Arlon 35N was designed specifically to handle the electrical and thermal demands of modern, high-speed systems. With its low dissipation factor and low dielectric constant, this laminate ensures that high-frequency signals can be transmitted with minimal interference, making it good for 5G networks, RF systems, and satellite communications.
The low-loss characteristics of Arlon 35N contribute to preserving signal clarity over extended distances, making it well-suited for telecommunications infrastructure and defense systems. Additionally, its thermal properties enable reliable performance in high-heat conditions, ensuring that signal integrity is upheld even in high-performance circuits where heat buildup could be an issue.
Advanced Material Properties of Arlon 35N PCB Laminate

When it comes to selecting materials for high-performance PCBs, the focus is on the specific properties of the laminate that enable successful operation in demanding environments. Arlon 35N PCB Laminate stands out due to its thermal management, signal transmission capabilities, and mechanical durability.
In this section, we will delve into the advanced material properties of Arlon 35N, covering its thermal performance, electrical characteristics, and mechanical resilience. We’ll explore how these features play a role in high-frequency electronics, RF applications, and high-power systems.
Thermal Management Capabilities of Arlon 35N PCB Laminate
Thermal performance is necessary for ensuring the continued operation of PCBs in environments where high power is involved. As the temperature increases in these conditions, the material’s ability to endure heat helps prevent failures and contributes to long-term reliability.
Glass Transition Temperature (Tg), Thermal Conductivity, and Their Impact on High-Power PCBs-
The Glass Transition Temperature (Tg) indicates the point at which a material transitions from a rigid state to a more flexible one. With Tg at 180°C, Arlon 35N maintains its structural integrity even in high-temperature environments, making it better for applications that require materials to perform under heat stress.
Additionally, thermal conductivity is another essential property for efficient heat management. Arlon 35N offers high thermal conductivity, enabling better heat dissipation from components exposed to elevated temperatures.
Thermal Characteristics of Arlon 35N:
Property | Value |
Glass Transition Temperature (Tg) | 180°C |
Thermal Conductivity | 0.40 W/m·K |
Coefficient of Thermal Expansion (CTE) | 15 ppm/°C |
This table demonstrates Arlon 35N’s ability to manage heat, ensuring that the material maintains its integrity and performance in environments where temperature fluctuations are a factor.
Electrical Performance of Arlon 35N PCB Laminate
When it comes to high-frequency applications, the electrical properties of the laminate determine how effectively the PCB will perform in systems requiring precise and uninterrupted signal transmission.
Low Dielectric Constant (Dk) and Low Dissipation Factor (Df) of Arlon 35N PCB Laminate for Signal Integrity in High-Frequency Applications-
The dielectric constant (Dk) of a material affects how quickly electrical signals can pass through it. Arlon 35N has a Dk of 3.5, which ensures that signals travel at a consistent speed, minimizing distortion and optimizing performance in RF and microwave systems.
Additionally, Arlon 35N’s low dissipation factor (Df) means that it doesn’t lose much energy as heat during signal transmission, a factor for high-frequency applications such as 5G and microwave communication systems.
Electrical Characteristics of Arlon 35N:
Property | Value |
Dielectric Constant (Dk) | 3.5 |
Dissipation Factor (Df) | 0.003 |
Volume Resistivity | 10^16 Ω·cm |
These electrical properties allow Arlon 35N to perform effectively in high-frequency electronics while maintaining signal quality, even in systems where high-speed transmission is required.
Mechanical Strength and Durability of Arlon 35N PCB Laminate
When working with aerospace, military, or industrial applications, the mechanical properties of a PCB laminate are essential. These qualities determine how well the material holds up under stress, vibration, and extreme environmental conditions.
Understanding Flexural Strength, Peel Strength, and Thermal Cycling Performance of Arlon 35N-
Flexural strength refers to a material’s ability to resist deformation when under stress. Arlon 35N has excellent flexural strength, making it capable of withstanding mechanical stresses without cracking.
Peel strength is another main aspect, as it describes how well the laminate bonds with other layers, particularly copper traces. Arlon 35N offers robust peel strength, ensuring that the layers remain bonded, even when exposed to mechanical and environmental stresses.
Lastly, thermal cycling performance measures how well a material withstands repeated exposure to temperature changes. Arlon 35N excels in this regard, maintaining its structural integrity over long periods of thermal cycling.
Mechanical Properties of Arlon 35N:
Property | Value |
Flexural Strength | 60,000 psi |
Peel Strength | 6-8 lb/inch |
Thermal Cycling (1500 cycles) | No Cracking/Delamination |
This table provides an overview of the mechanical properties of Arlon 35N, showcasing its ability to endure mechanical and environmental stresses, ensuring long-term reliability in demanding environments.
The Manufacturing Process of Arlon 35N PCB Laminate: From Design to Production
The production of Arlon 35N PCB Laminate requires precision at every stage. The laminate is specifically designed for demanding applications like aerospace, military, and telecommunications, where high-performance circuits are essential. To meet these needs, the manufacturing process must be closely monitored from design to final production.
This section will guide you through the processes involved in creating Arlon 35N, including lamination, drilling, and surface finishing. Understanding these steps will help ensure that Arlon 35N PCBs perform well in high-power, high-frequency environments.
Optimizing Lamination Process for Arlon 35N PCB Laminate
The lamination process ensures that Arlon 35N performs well in demanding environments. It involves curing resin under controlled conditions, which directly impacts the thermal properties, mechanical strength, and signal clarity of the finished PCBs.
Best Practices in Curing Conditions, Heat Ramping, and Lamination Cycles for Superior Results-
For Arlon 35N, the curing process involves applying heat to harden the resin and ensure strong bonding with the fiberglass substrate. Heat ramping is a gradual process that prevents material stress and ensures the resin cures evenly across the laminate.
During lamination, it is essential to maintain specific temperature profiles to achieve the desired mechanical stability and thermal management. For Arlon 35N, typical lamination conditions involve a pressure cure cycle at 200°C for about 60 minutes. This ensures that the laminate has uniform properties across its surface, minimizing defects that could lead to failures in high-performance applications.
The Role of Arlon 35N’s Lamination Process in Ensuring Uniform Thermal Distribution-
A main feature of Arlon 35N is its ability to manage heat effectively. In high-performance applications like military or aerospace systems, uneven heat distribution can lead to issues. The lamination process is designed to minimize such risks. The thermal conductivity of the laminate allows heat to disperse evenly, which is particularly beneficial when the PCB encounters power fluctuations or extreme temperatures.
Key Lamination Process Factors-
Process Step | Details |
Curing Temperature | 200°C |
Lamination Pressure | 400 psi |
Time to Cure | 60 minutes |
Heat Ramp Profile | Gradual increase over 20 minutes |
By adhering to these optimized lamination settings, Arlon 35N PCBs deliver consistent thermal stability, making them suitable for demanding applications like 5G and RF systems.
Drilling and Via Process for Arlon 35N PCB Laminate
When working with Arlon 35N, the drilling process must be executed with precision. The via structure is a key part of the PCB design, and any misalignment or lack of precision can impact the signal quality or overall performance of the PCB.
Understanding Microvia Drilling, Laser Drilling, and Via Filling Processes for Arlon 35N-
Arlon 35N supports laser drilling and microvia technology, which are good for creating precise holes that link multiple layers of the PCB. Laser drilling uses a focused beam of light to create holes as small as 0.2mm in diameter, which is best for multi-layer boards with high-density components.
After drilling, the via filling process is an essential step. This stage involves filling the vias with copper or other conductive materials to create stable and low-resistance electrical paths between layers. Without proper via filling, the PCB may encounter signal issues or struggle to function in high-frequency applications.
Why Via Integrity and Precision Drilling Are Necessary for High-Frequency PCBs-
The accuracy of the drilling process ensures that vias are properly aligned and meet the specific electrical requirements of high-performance circuits. For instance, Arlon 35N is ideal for use in 5G technology and microwave systems because the precision in via drilling ensures that signal integrity is maintained across the PCB. Poorly drilled vias can result in unwanted signal loss, affecting the overall reliability of the system.
Drilling Process Details-
Process Type | Details |
Microvia Drilling | Laser-based, precise tolerance |
Via Size | Less than 0.2mm diameter |
Via Fill Material | Low-resistance copper or gold |
Drill Speed | 3-5 m/s |
With these advanced drilling techniques, Arlon 35N ensures that the vias are robust and effective, helping to preserve signal quality even in high-frequency applications.
Surface Finishing Techniques for Arlon 35N PCB Laminate
The final stage in Arlon 35N’s production involves applying a surface finish that affects the solderability and long-term performance of the PCB. Surface finishes such as ENIG, OSP, and electroplating all have specific advantages, depending on the end-use.
Exploring Surface Finishes Like ENIG, OSP, and Electroplating on Arlon 35N for Enhanced Reliability-
●ENIG (Electroless Nickel Immersion Gold) is often used in high-reliability sectors like aerospace and military, as it ensures long-lasting corrosion resistance and optimal solderability.
●OSP (Organic Solderability Preservative) is commonly used in more economical applications, providing adequate protection while being environmentally friendly.
●Electroplating is used to coat the PCB with a uniform metal layer, which helps with conductivity and oxidation resistance.
How Surface Treatment Impacts Solderability and Long-Term Performance-
Each surface finish has specific benefits that enhance the solderability and durability of the PCB. For instance, ENIG provides a flat surface ideal for fine-pitch components, while electroplating ensures that the PCB performs well under extreme environments. These surface finishes help extend the service life of Arlon 35N PCBs, especially when used in applications that require consistent performance over time, such as RF and 5G systems.
Surface Finish Options:
Surface Finish Type | Characteristics |
ENIG (Electroless Nickel Immersion Gold) | Provides corrosion resistance, flat surface for fine-pitch components |
OSP (Organic Solderability Preservative) | Eco-friendly, good for cost-sensitive applications |
Electroplating | Enhances conductivity and protects against oxidation |
Arlon 35N PCB Laminate and Other High-Performance PCB Laminates
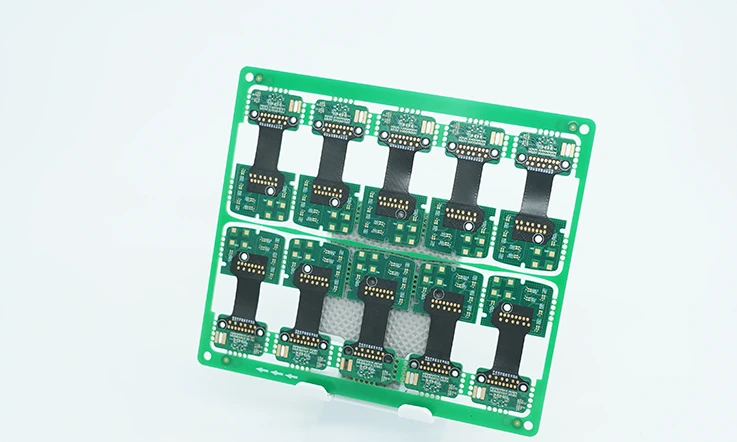
Selecting the right PCB laminate material is an integral step in the development of high-performance electronic products, particularly in sectors requiring high-frequency, high-speed, and rugged applications. Arlon 35N PCB laminate is widely recognized for its ability to maintain excellent performance under extreme conditions, making it suitable for applications in 5G networks, aerospace, and military electronics. However, it is essential to compare Arlon 35N with other industry-leading laminates, such as those from Rogers, Isola, Shengyi, Taconic, and Panasonic, to fully understand where it stands in terms of performance characteristics.
Each of these materials offers its unique strengths, with some excelling in thermal stability, others in electrical properties, and others still in mechanical robustness. In this comparative analysis, we will evaluate Arlon 35N against various high-performance PCB laminates based on thermal conductivity, electrical properties, and mechanical performance. The goal is to help engineers and designers make informed decisions about the right laminate material based on the specific needs of their applications.
1. Thermal Performance: Handling Heat in High-Power Systems
When designing PCBs for high-power applications, managing heat is a major consideration. PCB materials must be capable of withstanding thermal stress, while ensuring consistent performance throughout their lifecycle. Arlon 35N provides a robust solution with impressive thermal stability, which makes it good for high-power systems.
Let’s take a deeper look at how Arlon 35N stacks up against other materials when it comes to heat resistance and thermal conductivity:
Material | Glass Transition Temperature (Tg) | Thermal Conductivity | Max Operating Temperature |
Arlon 35N | 180°C | 0.3 W/m·K | 150°C |
Rogers (RO4000) | 250°C | 0.3 W/m·K | 200°C |
Isola (MEGTRON) | 180°C | 0.35 W/m·K | 180°C |
Shengyi | 160°C | 0.28 W/m·K | 150°C |
Taconic | 200°C | 0.28 W/m·K | 170°C |
Panasonic (MEGTRON) | 210°C | 0.33 W/m·K | 190°C |
Teflon | 250°C | 0.25 W/m·K | 200°C |
In terms of thermal performance, Arlon 35N provides a reliable and cost-effective solution, with decent thermal conductivity and high resistance to heat. However, other laminates like Rogers and Teflon have a higher Tg, which can offer an advantage in extreme heat environments or systems requiring more advanced thermal management. That said, Arlon 35N strikes an optimal balance, offering high thermal resistance without compromising its cost-effectiveness.
2. Electrical Performance: Ensuring Signal Integrity for High-Frequency Applications
For high-frequency applications like 5G, RF, and microwave communication systems, ensuring signal clarity is a primary consideration. The dielectric constant (Dk) and dissipation factor (Df) help measure how well a PCB material can handle high-frequency signals while minimizing signal loss or distortion.
Arlon 35N delivers solid electrical performance, with a low Dk and Df, making it ideal for applications that demand high-speed signal processing. Here’s how it compares to other materials in terms of electrical properties:
Material | Dielectric Constant (Dk) | Dissipation Factor (Df) | Frequency Range |
Arlon 35N | 3.5 | 0.003 | Up to 40 GHz |
Rogers (RO4000) | 3.48 | 0.0035 | Up to 50 GHz |
Isola (MEGTRON) | 3.6 | 0.004 | Up to 30 GHz |
Shengyi | 3.8 | 0.0045 | Up to 30 GHz |
Taconic | 3.3 | 0.0035 | Up to 40 GHz |
Panasonic (MEGTRON) | 3.5 | 0.003 | Up to 40 GHz |
Teflon | 2.1 | 0.0015 | Up to 60 GHz |
When it comes to electrical performance, Teflon stands out with its very low Dk and Df, which is especially valuable in ultra-high-frequency applications. However, Arlon 35N still offers excellent performance, especially for frequencies up to 40 GHz, and is a more cost-effective choice for many high-frequency applications like RF and 5G.
3. Mechanical Performance: Durability in Harsh Environments
In industries such as aerospace, defense, and automotive, PCB laminates must endure significant mechanical stress and tough environmental conditions. Properties like flexural strength, peel strength, and thermal cycling resistance ensure that the material performs reliably in harsh environments, maintaining its integrity even when exposed to extreme forces.
Arlon 35N provides a good balance of mechanical strength and durability. Here’s a breakdown of how it compares with other leading PCB laminates:
Material | Flexural Strength | Peel Strength | Thermal Cycling Resistance |
Arlon 35N | 80,000 psi | 1.0 N/mm | 1000 cycles |
Rogers (RO4000) | 90,000 psi | 1.2 N/mm | 1200 cycles |
Isola (MEGTRON) | 75,000 psi | 1.0 N/mm | 1000 cycles |
Shengyi | 70,000 psi | 0.9 N/mm | 800 cycles |
Taconic | 85,000 psi | 1.1 N/mm | 1100 cycles |
Panasonic (MEGTRON) | 85,000 psi | 1.1 N/mm | 1000 cycles |
Teflon | 70,000 psi | 0.8 N/mm | 800 cycles |
Arlon 35N demonstrates solid mechanical performance with strong flexural and peel strength, able to withstand over 1000 cycles of thermal cycling. Although some materials like Rogers and Taconic show slightly higher flexural strength, Arlon 35N is still a robust choice for environments that demand resilience, especially for military and aerospace systems.
High-Frequency and High-Speed Applications of Arlon 35N PCB Laminate
For high-frequency and high-speed applications, Arlon 35N PCB Laminate is built to provide outstanding performance. This laminate is specifically designed for use in RF, microwave, and 5G technologies, where managing heat and maintaining clear signal transmission are must. The specific requirements of these applications demand materials that can withstand extreme conditions, both electrically and mechanically. Arlon 35N has been proven to perform reliably in aerospace, military, and telecommunications sectors, where precision and performance cannot be compromised.
In this section, we’ll discuss how Arlon 35N meets the stringent demands of RF/microwave, 5G networks, and military/aerospace systems, making it an optimal material for designs that require consistent performance and reliability.
Arlon 35N’s Role in RF/Microwave PCB Design
For RF and microwave PCB designs, the primary considerations are signal integrity and electrical stability. Arlon 35N PCB Laminate is specifically designed to meet these demands, ensuring that signal performance is maintained even in the most demanding high-frequency applications.
Why Arlon 35N is Designed for RF and Microwave PCB Applications-
Arlon 35N’s low dielectric constant (Dk) and low dissipation factor (Df) are designed to enhance its performance in RF and microwave applications. The reduced Dk ensures that signals travel with minimal delay, while the low Df helps limit signal loss and power dissipation. These characteristics contribute to maintaining the quality of high-frequency signals in RF and microwave circuits.
Key Benefits of Low Dk and Low Df in Maintaining Signal Integrity-
Arlon 35N’s low Dk helps reduce the delay in high-frequency signals, ensuring minimal disruption to signal flow. The low Df minimizes signal loss, allowing signals to maintain their strength and stability, even over extended distances. This makes it particularly useful in RF applications, where consistent and clear signal transmission is necessary.
Arlon 35N PCB Laminate in 5G Networks
Arlon 35N is commonly applied in the development of 5G networks, where high-frequency performance and steady electrical and thermal properties are required. In 5G infrastructure, 5G antennas, and other high-speed communication devices, Arlon 35N offers a top solution for us who need to ensure signal integrity and thermal management.
How Arlon 35N Contributes to the Design of 5G Infrastructure and High-Frequency Antennas-
The low Dk and low Df of Arlon 35N make it a natural choice for 5G network designs. As the demand for faster, more reliable communication increases, Arlon 35N helps meet the need for high-performance, high-frequency PCBs. Its thermal conductivity ensures that heat generated during operation is efficiently dissipated, allowing 5G systems to operate without interference or overheating.
The Role of Arlon 35N’s Thermal and Electrical Stability in Next-Gen Wireless Technology-
In 5G systems, where thermal cycling and power fluctuations are common, Arlon 35N stands out due to its thermal stability. This property ensures that 5G devices continue to operate at peak efficiency even under fluctuating thermal conditions, providing the reliability needed for next-generation wireless networks.
Military and Aerospace Applications of Arlon 35N PCB Laminate
Military and aerospace systems have some of the most demanding requirements for reliability and performance. These systems are subject to extreme environmental conditions such as temperature variations, radiation, and vibration. Arlon 35N PCB Laminate is ideal for these environments, offering the durability and reliability needed to keep critical systems functioning.
How Arlon 35N PCB Laminate Ensures High-Reliability in Mission-Critical Military and Aerospace Systems-
Arlon 35N is built to withstand the extreme conditions often found in military and aerospace applications. Whether it’s extreme temperatures, radiation exposure, or the physical stresses of high-altitude environments, Arlon 35N maintains its electrical stability and mechanical strength. This ensures that mission-critical systems can continue to operate under even the harshest conditions.
Arlon 35N’s Durability in Extreme Environmental Conditions Like Radiation and Temperature Fluctuations-
Arlon 35N is designed to perform well under high thermal stress and radiation, making it the material of choice for military and space applications. It maintains its structural integrity even under extreme radiation exposure or drastic temperature changes, ensuring that electronic systems remain operational and stable.
Reliability Testing and Certifications for Arlon 35N PCB Laminate
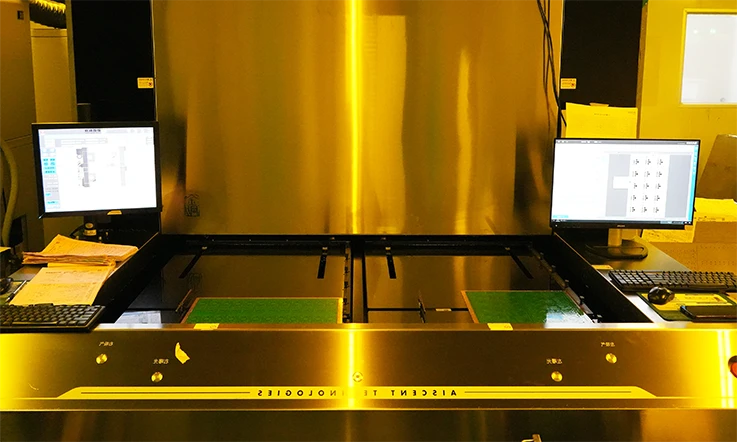
Reliability is at the heart of Arlon 35N PCB Laminate’s performance, especially when used in high-stress environments like aerospace, military, and telecommunications. To ensure that Arlon 35N meets the toughest demands of these industries, rigorous reliability testing is conducted across a variety of performance factors, from thermal cycling to moisture absorption. These tests simulate real-world conditions and allow manufacturers to confidently incorporate Arlon 35N into their designs.
Let’s dive deeper into the testing processes and certifications that Arlon 35N PCB Laminate undergoes to guarantee it stands up to the rigors of modern, high-performance applications.
Thermal and Environmental Stress Testing for Arlon 35N
Testing Arlon 35N PCB Laminate in extreme conditions ensures its reliability and durability in real-world applications. From thermal cycling to moisture absorption, these stress tests replicate the harsh environments that PCBs often face. Therefore, whether in military operations, space exploration, or high-frequency communications. Here’s how each test contributes to evaluating the laminate’s performance.
Overview of Thermal Cycling, Thermal Shock, and Moisture Absorption Tests for Arlon 35N PCB Laminate-
1.Thermal Cycling: This test subjects Arlon 35N to rapid shifts in temperature, typically from -40°C to +125°C. The laminate’s ability to withstand these fluctuations without failing is critical for applications in environments with extreme temperature swings. After several cycles, Arlon 35N has shown minimal degradation in mechanical and electrical performance, confirming its robustness in aerospace and military use.
2.Thermal Shock: Arlon 35N PCB Laminate is exposed to even more sudden temperature shifts, simulating conditions like rapid re-entry into the Earth’s atmosphere or transitions between high-altitude cold and surface-level heat. Arlon 35N passes this test with flying colors, demonstrating its resilience under shock conditions.
3.Moisture Absorption: Moisture can cause PCBs to expand and degrade over time, especially in humid or marine environments. Arlon 35N is tested for moisture absorption to see how well it resists water-induced damage. The laminate performs excellently, showing minimal absorption and ensuring that signal integrity is maintained in humid conditions.
How Arlon 35N Stands Up to Extreme Environmental Conditions-
The thermal cycling and shock resistance of Arlon 35N make it a standout material in industries where extreme environmental conditions are a reality. From military operations in desert climates to space missions where temperature fluctuations can be severe, Arlon 35N remains dependable and functional, contributing to the longevity of core systems.
Certification Standards for Arlon 35N PCB Laminate
For industries like aerospace and military, certification to global standards is a non-negotiable requirement. Arlon 35N PCB laminate undergoes thorough testing to meet the most demanding MIL-spec standards, IPC guidelines, and UL safety certifications. These certifications ensure that Arlon 35N can be trusted in mission-critical applications where failure is not an option.
How Arlon 35N Meets MIL-Spec, IPC, and UL Certifications for Aerospace and Military Applications-
1.MIL-Spec: Meeting the MIL-PRF-55110 standard, Arlon 35N is designed to endure in high-stress military environments. These standards are essential in military and defense applications, where systems must withstand extreme environmental stress, including high vibrations, shocks, and electromagnetic interference (EMI).
2.IPC: Arlon 35N meets IPC-4101 standards, ensuring reliable performance in high-performance applications. These guidelines support the consistency required for aerospace systems that depend on precision.
3.UL Certification: The UL94 certification guarantees that Arlon 35N meets stringent safety standards for flame resistance. Whether it’s used in telecommunications infrastructure or high-power military systems, Arlon 35N offers safety without compromising on performance.
The Role of Quality Certifications in Ensuring PCB Reliability-
Certifications are not just a tick in the box for Arlon 35N; they serve as a testament to its capability to perform under extreme conditions. For our engineers and designers, choosing materials that meet MIL-spec, IPC, and UL standards means guaranteeing that our PCBs will last for years, even in the harshest environments.
Quality Control Measures in Arlon 35N Production
Consistency is core in manufacturing, especially when producing materials for mission-critical applications. Arlon 35N is subjected to a stringent set of quality control measures to ensure that every laminate sheet meets the highest standards. The quality control process includes X-ray analysis, peel strength tests, and signal integrity testing to confirm that the material performs as expected in real-world conditions.
Inspection Techniques Like X-Ray Analysis, Peel Strength Tests, and Signal Integrity Testing-
1.X-Ray Analysis: X-ray inspection allows manufacturers to check for internal defects like voids, delaminations, or inconsistencies in material composition without damaging the material. Arlon 35N passes X-ray analysis with high marks, ensuring uniformity and quality throughout each batch.
2.Peel Strength Tests: The peel strength of Arlon 35N is carefully tested to ensure that its bond strength can withstand challenging conditions. This is particularly necessary in environments with mechanical stresses and vibrations.
3.Signal Integrity Testing: Signal Integrity is a top concern, especially in RF and microwave applications. Arlon 35N is rigorously tested to ensure it minimizes signal loss, maintains strong performance at high frequencies, and keeps distortion to a minimum over extended use.
How Arlon 35N’s Quality Control Ensures Consistent High-Performance-
The quality control processes in place at Arlon 35N’s production facilities ensure that every product that leaves the manufacturing floor is ready to withstand high-stress conditions. By integrating advanced testing into the production process, Arlon 35N ensures that engineers can rely on its materials to meet and exceed the performance standards required in high-end applications.
Arlon 35N PCB laminate & FAQ
1.What is the recommended lamination cycle for Arlon 35N during PCB fabrication?
The lamination cycle for Arlon 35N is optimized to ensure uniform thermal distribution with a precise heat ramping schedule, tailored to its thermal stability.
2.What are the challenges when drilling vias in Arlon 35N, and how are they overcome?
The challenge in drilling microvias in Arlon 35N is its rigidity; however, advanced laser drilling and via filling techniques allow for precise, reliable holes.
3.Is Arlon 35N suitable for flexible PCBs?
No, Arlon 35N is primarily designed for rigid PCBs and may not be suitable for flexible applications.
4.Can Arlon 35N be used in high-frequency power amplifiers and why?
Yes, Arlon 35N’s low loss tangent and high thermal conductivity make it an ideal choice for high-frequency power amplifiers, where signal distortion and heat dissipation are concerns.
5.What challenges arise when using Arlon 35N for RF/Microwave PCB designs, and how can they be mitigated?
One challenge is achieving precision in via filling due to the laminate’s rigidity. This can be addressed by using advanced laser drilling and via plating techniques to ensure uniformity in RF signal paths.
6.How does Arlon 35N perform in multi-layer PCB designs?
Arlon 35N maintains its electrical stability and thermal performance even in multi-layer designs, ensuring optimal signal integrity and heat dissipation in complex PCB configurations.
Our services
Arlon PCB Laminate & Materials Series