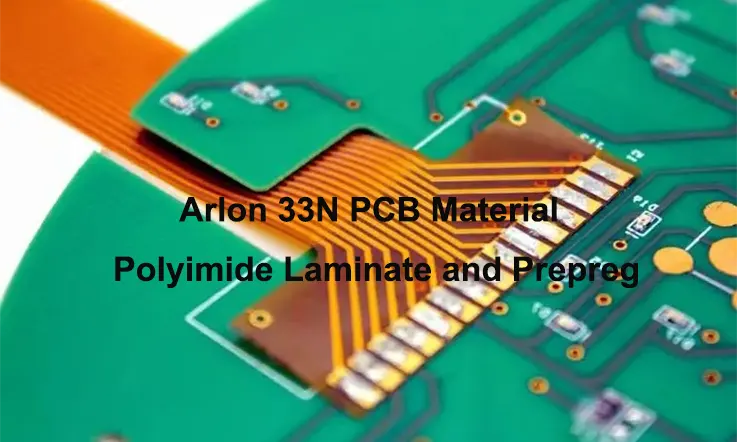
As a PCB layout engineer, selecting the right materials is crucial for achieving optimal performance and reliability in electronic designs. One such exceptional material is Arlon 33N, a high-performance polyimide laminate and prepreg. With its unique properties and advanced characteristics, Arlon 33N offers numerous advantages for demanding electronic applications.
What is Arlon 33N PCB Materials?
Arlon 33N: Polyimide Laminate and Prepreg
33N is a polyimide laminate and prepreg system that has been specifically designed to exhibit excellent flame retardance, as proven by its UL94 V-0 rating. This system combines the outstanding high performance properties of polyimide with the crucial requirement of flame retardance. With a high glass transition temperature (Tg) of 250°C, this material demonstrates minimal z-axis expansion, thereby reducing the likelihood of latent plated through hole (PTH) defects during service.
Features of Arlon 33N PCB Laminate Materials
Arlon 33N PCB Laminate Materials possess several notable features that make them stand out in the industry:
1.Compliance: These materials meet the rigorous standards set by IPC4101/40 and /41 in terms of description and specification. This ensures their reliability and adherence to industry requirements.
2.Fire Safety: The laminates are UL recognized as UL94 V-0, indicating their excellent flame retardant properties. This certification assures that the materials meet stringent safety standards.
3.Exceptional Thermal Performance: Arlon 33N exhibits best-in-class thermal properties, with a glass transition temperature (Tg) exceeding 250d°C. This high Tg value ensures the laminate’s stability and reliability under elevated temperatures.
4.Low Z-Axis Expansion: The laminate has a low Z-axis expansion coefficient of only 1.2% between 50-260°C, which is significantly lower than the 2.5-4.0% typically observed in high-performance epoxies. This characteristic minimizes the risk of latent PTH (Plated Through-Hole) defects that can occur during solder reflow and device attachment processes.
5.Enhanced High-Temperature Performance: Arlon 33N surpasses typical high-performance epoxies with its impressive decomposition temperature of 390°C (compared to 300-360°C in other materials). This outstanding long-term high-temperature performance ensures the reliability and durability of the laminate in demanding applications.
6.Toughened Chemistry: The laminate employs a toughened chemistry that effectively resists resin fracturing. This characteristic enhances the material’s mechanical strength and durability, reducing the likelihood of failure due to environmental stresses.
7.Lead-Free Processing Compatibility: Arlon 33N is fully compatible with lead-free processing techniques. This feature allows for seamless integration into modern manufacturing processes that prioritize environmental sustainability and regulatory compliance.
8.Regulatory Compliance: The laminate is compliant with RoHS/WEEE regulations, further underscoring its commitment to environmental responsibility and ensuring its suitability for use in diverse industries.
Overall, Arlon 33N PCB Laminate Materials offer a comprehensive range of features that make them an ideal choice for demanding applications. Their compliance with industry standards, exceptional thermal properties, low Z-axis expansion, high-temperature performance, toughened chemistry, compatibility with lead-free processing, and adherence to regulatory requirements make them a reliable and versatile option for professional PCB layout engineers.
Arlon 33N PCB Materials: Applications
Arlon 33N PCB Laminate Materials are particularly well-suited for a variety of applications, especially those that involve high temperatures and long-term exposure to elevated thermal conditions. Some typical applications where Arlon 33N is commonly utilized include:
1.PCBs in High-Temperature Processing:
These laminates are ideal for PCBs that undergo processes involving high temperatures, such as lead-free soldering, HASL (Hot Air Solder Leveling), and IR (Infrared) reflow. The exceptional thermal properties, including the high glass transition temperature (Tg) and low Z-axis expansion, make Arlon 33N reliable and resilient during these demanding manufacturing processes.
2.Aircraft Engine Instrumentation:
Arlon 33N is suitable for applications within aircraft engines, particularly for instrumentation systems. These systems often operate in extreme temperature environments, and the laminate’s outstanding long-term high-temperature performance ensures the reliability and durability of the PCBs in these critical systems.
3.Down Hole Drilling:
In the oil and gas industry, down hole drilling equipment operates in harsh and high-temperature conditions. Arlon 33N laminates can withstand the demanding thermal environment encountered in these drilling applications, ensuring the reliable operation of the PCBs used in control systems, sensors, and data acquisition modules.
4.Under-Hood Automotive Controls:
PCBs in automotive applications located under the hood are subjected to high temperatures due to engine heat. Arlon 33N laminates provide the necessary thermal stability and durability required for automotive control modules, ensuring the reliable operation of critical systems like engine management, transmission control, and powertrain control units.
5.Burn-In Boards:
Burn-in boards are used to stress test electronic components by subjecting them to elevated temperatures for extended periods. Arlon 33N laminates excel in these applications due to their exceptional long-term high-temperature performance, ensuring the reliability and longevity of the burn-in boards during the rigorous testing process.
6.Industrial Sensors:
Industrial sensors used in various applications, such as manufacturing, chemical processing, and power generation, often operate in high-temperature environments. Arlon 33N laminates provide the necessary thermal stability and mechanical strength for PCBs used in these sensors, ensuring accurate and consistent data acquisition under demanding conditions.
Arlon 33N PCB Material: Properties
Arlon 33N PCB Laminate Material possesses several key properties in the areas of thermal, electrical, and mechanical performance:
Thermal Property:
●Decomposition Temperature: 353 °C
●Td (Temperature at 5% weight loss): 389 °C
●Glass Transition Temperature (Tg): >250 °C (TMA)
●Z-Axis Coefficient of Thermal Expansion (CTE): Below Tg: 53 ppm/°C, Above Tg: 164 ppm/°C
●Thermal Conductivity: 0.200 W/m-K
Electrical Property:
●Dielectric Constant (Dk): 4.25 (at 1 MHz)
●Dissipation Factor (Df): 0.01 (at 1 MHz)
●Volume Resistivity (C96/35/90): 7.2 x 107 MΩ-cm
●Volume Resistivity (E24/125): 4.5 x 108 MΩ-cm
●Surface Resistivity (C96/35/90): 4.1 x 108 MΩ-cm
●Surface Resistivity (E24/125): 1.6 x 109 MΩ-cm
Mechanical Property:
●Water Absorption Rate: 0.21%
●Peel Strength to Copper at Elevated Temperatures: 7.2 (1.2) Ib/in (N/mm)
●Peel Strength to Copper after Process Solutions: 7.5 (1.3) Ib/in (N/mm)
These properties contribute to the high performance and reliability of Arlon 33N PCB material. It exhibits a high decomposition temperature, exceptional glass transition temperature, low Z-axis CTE, and low water absorption rate, making it well-suited for high-temperature applications and providing thermal stability. Additionally, its high dielectric constant, low dissipation factor, and good electrical resistivity make it suitable for insulation in electronic circuits. The peel strength to copper at elevated temperatures and after process solutions ensures the material’s mechanical integrity during manufacturing and operational conditions.
Arlon 33N: Recommended Process Conditions
For optimal results, the following process conditions are recommended for working with Arlon 33N PCB Laminate Materials:
1. Inner Layer Processing:
●Follow standard industry practices for developing, etching, and stripping inner layers.
●Apply brown oxide on inner layers, ensuring a uniform coating by adjusting the dwell time in the oxide bath.
●Prior to lay-up, bake the inner layers in a rack for 60 minutes at a temperature range of 107°C – 121°C (225°F – 250°F).
2. Prepreg Handling:
●Vacuum desiccate the prepreg for 8 – 12 hours before lamination.
3. Lamination Cycle:
1) Pre-vacuum: Perform pre-vacuuming for 30 – 45 minutes.
2) Heat Rise Control: Control the heat rise rate between 4.5°C – 6.5°C (8°F – 12°F) per minute within the temperature range of 100°C and 150°C (210°F and 300°F).
3) Cure Temperature: Set the cure temperature at 213°C (415°F). Start the cycle timer when the product temperature reaches 210°C (410°F).
4) Cure Time: Maintain the product temperature at the cure temperature for 90 minutes. For sequential lamination, use 60 minutes for the first lamination and 90 minutes for the final lamination.
5) Cool Down: Allow the laminated product to cool down under pressure at a rate of ≤ 6°C/min (12°F/min).
It is important to note that these recommended process conditions are specific to Arlon 33N PCB Laminate Materials and have been established to ensure optimal performance and reliability. Following these guidelines will help achieve consistent and high-quality results during the manufacturing process.
Conclusion
Arlon 33N stands as a top choice for PCB layout engineers seeking high-performance polyimide laminate and prepreg. Its superior thermal stability, outstanding electrical properties, and robust mechanical strength make it ideal for applications where reliability, durability, and performance are paramount.
By utilizing Arlon 33N in electronic designs, PCB layout engineers can ensure the production of high-quality, high-reliability PCBs that meet the stringent requirements of modern electronic systems. Embracing Arlon 33N empowers engineers to push the boundaries of technology and deliver innovative solutions to the ever-evolving electronics industry.
Our services
Arlon PCB Laminate & Materials Series