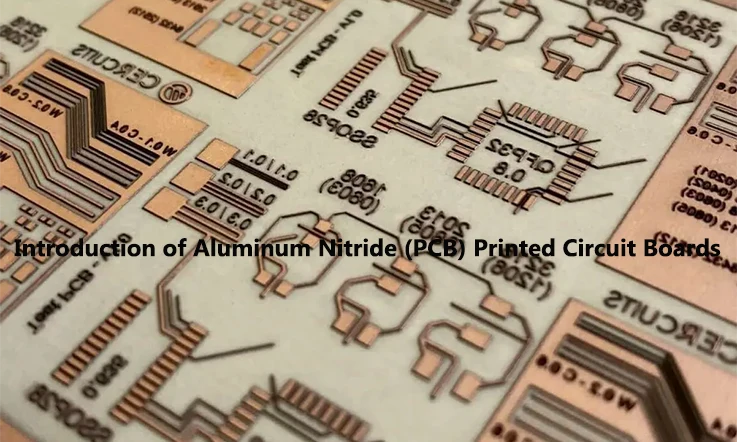
As high-power electronics continue to advance, managing heat and ensuring device reliability are growing challenges. Aluminum Nitride (AlN) PCBs have emerged as an effective solution, offering superior thermal conductivity, electrical insulation, and mechanical strength. Industries such as automotive, telecommunications, and power electronics are turning to Aluminum Nitride PCBs for their ability to support high-performance systems under demanding conditions.
This article delves into the properties, design, manufacturing, benefits, Limitations of Aluminum Nitride PCBs, exploring how they provide thermal efficiency and electrical reliability. From electric vehicles to LED lighting, AlN PCBs are transforming the way electronics handle heat and power, ensuring longevity and consistent performance in diverse applications. As the need for high-efficiency solutions grows, Aluminum Nitride PCBs are positioned to drive future advancements in power electronics.
Understanding Aluminum Nitride PCB Technology
As the demand for high-performance electronics continues to grow, Aluminum Nitride PCBs have emerged as a powerful solution to address challenges in thermal management and electrical insulation. Unlike traditional PCBs made from materials like FR4 or copper, Aluminum Nitride offers remarkable properties that make it a good choice for applications requiring superior heat dissipation and electrical performance. In this section, we will explore the fundamental technology behind Aluminum Nitride PCBs, including how they function and the benefits they offer in high-power environments.
What is Aluminum Nitride PCB and How Does It Work?
Aluminum Nitride PCB is a ceramic-based printed circuit board known for its excellent thermal conductivity and effective electrical insulation. These qualities make it well-suited for high-power applications where efficient heat management is necessary. The material’s performance relies on its unique structure and composition, which enable effective heat dissipation while maintaining electrical isolation.
At the heart of AlN PCB technology is the aluminum nitride ceramic, which has one of the highest thermal conductivity values of any known ceramic material, often exceeding 170 W/mK. This allows AlN PCBs to efficiently dissipate heat generated by high-power electronic components, thereby preventing overheating and extending the lifespan of the components.
Furthermore, Aluminum Nitride PCBs are electrically insulating, which means they prevent electrical short circuits or interference between conductive traces. This combination of thermal conductivity and electrical insulation makes AlN PCBs a go-to solution for demanding applications such as power supplies, LED lighting, and automotive electronics.
Example in Application:
In power electronics, where components like power transistors and power amplifiers generate significant heat, Aluminum Nitride PCBs help manage this heat efficiently. Without AlN, these components would overheat, leading to failure or reduced performance.
Key Properties of Aluminum Nitride PCB
Understanding the core properties of Aluminum Nitride PCBs can help us choose the right material for their applications. The primary attributes of AlN PCBs are:
1.High Thermal Conductivity-
As mentioned earlier, Aluminum Nitride has exceptional thermal conductivity, typically in the range of 170-200 W/mK, which is significantly higher than other materials like FR4 (around 0.3 W/mK) or ceramic-based boards like Alumina (typically around 30-40 W/mK). This high thermal conductivity ensures that heat generated by high-power devices is quickly transferred away from sensitive components, preventing overheating.
2.Electrical Insulation-
Aluminum Nitride not only offers superior heat dissipation but also excellent electrical insulation. This makes it ideal for circuits where electrical isolation is necessary, such as in high-voltage or RF (radio frequency) applications. The dielectric strength of AlN is also high, typically in the range of 10-15 kV/mm, ensuring that the material can safely handle high-voltage environments without breaking down.
3.Mechanical Strength-
Although Aluminum Nitride is a ceramic material, it maintains a high level of mechanical strength. This durability ensures that AlN PCBs can endure the stresses faced both during production and while in use. Additionally, Aluminum Nitride features a low coefficient of thermal expansion (CTE), which helps protect components from potential damage caused by the thermal cycles they undergo in high-performance environments.
Benefits of Using Aluminum Nitride PCBs in High-Power Electronics
When you compare Aluminum Nitride PCBs to more traditional materials like FR4 or copper, it’s easy to spot the differences. Aluminum Nitride PCBs bring advantages in both thermal conductivity and electrical isolation, making them the go-to choice for applications where heat management and insulation matter the most. With AlN PCBs, you’re not just getting a board – you’re getting a performance boost for your high-demand projects. These qualities make AlN PCBs a solid pick when you need reliable heat dissipation and stable electrical properties.
1.Improved Thermal Management-
Traditional PCBs struggle to manage heat in high-power environments, often relying on heat sinks or other external cooling mechanisms. Aluminum Nitride PCBs, on the other hand, offer intrinsic heat dissipation properties. This results in more efficient cooling without the need for bulky, external heat dissipation systems. For example, in automotive power modules, AlN PCBs ensure that high-power components like inverters operate efficiently, maintaining performance while preventing overheating.
2.Enhanced Component Lifespan and Reliability-
Overheating is one of the most common causes of failure in high-power electronics. By offering superior thermal conductivity, Aluminum Nitride PCBs help reduce the thermal stresses that components are exposed to, increasing their lifespan and reliability. For industries like LED lighting, where heat buildup can degrade performance and shorten operational life, AlN PCBs help maintain consistent performance and ensure longevity.
3.Versatility in High-Performance Applications-
AlN PCBs excel in applications where high voltage and current must be handled in combination with extreme thermal management needs. These include sectors such as telecommunications, solar power, and high-frequency electronics. For instance, in telecommunication infrastructure, where power components like RF amplifiers need both thermal and electrical insulation properties, Aluminum Nitride PCBs provide a reliable solution that maximizes both efficiency and reliability.
Case Study: LED Lighting Industry
The LED lighting industry has been one of the major beneficiaries of AlN PCB technology. LEDs generate substantial heat, and without adequate heat management, their performance would degrade. Aluminum Nitride PCBs allow for better thermal dissipation, helping LEDs maintain consistent brightness and reduce failure rates due to overheating.
What Are The Limitations Of Using Aluminum Nitride PCB?
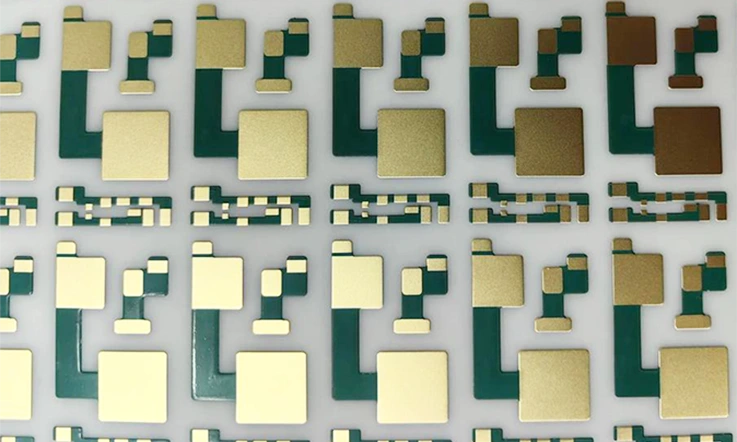
Aluminum Nitride PCBs are increasingly favored in high-performance electronic applications due to their remarkable thermal conductivity and electrical insulation properties. However, despite these advantages, there are some drawbacks that need to be taken into consideration when selecting this material for PCB designs. Understanding these limitations can help us make informed decisions when choosing materials for specific projects.
In this section, we’ll explore the key limitations of Aluminum Nitride PCBs, from the cost to safety considerations. By examining these factors, we can better understand where AlN PCBs may or may not be the best choice for your designs.
Higher Cost of Aluminum Nitride PCBs
One of the most significant disadvantages of using Aluminum Nitride PCBs is their higher cost compared to other materials, such as alumina or FR4 PCBs. While AlN PCBs offer superior thermal conductivity and electrical insulation, they come at a premium price, which can be a barrier in cost-sensitive applications.
Here’s a quick breakdown of the cost comparison:
Material Type | Cost (per square meter) | Thermal Conductivity (W/mK) | Applications |
Aluminum Nitride (AlN) | $200–$400 | 170–200 W/mK | High-power, high-frequency electronics |
Alumina (Al₂O₃) | $50–$150 | 30 -40W/mK | General electronics, low power |
FR4 (Fiberglass) | $10–$50 | 0.3 W/mK | Low-power, general use |
As shown in the table, Aluminum Nitride offers exceptional thermal performance, but its higher cost can be a deciding factor when the budget is a major concern. However, in applications requiring high thermal conductivity, such as power electronics or LED drivers, the higher cost of AlN is justified by the benefits it provides in terms of heat dissipation and reliability.
Health Risks and Safety Concerns
Another potential downside of using Aluminum Nitride PCBs is the health risk associated with exposure to aluminum nitride particles. While the material itself is stable in solid form, during manufacturing processes, such as laser cutting or sintering, fine aluminum nitride dust can be generated. If inhaled, ingested, or injected, aluminum nitride particles can pose health risks, including lung toxicity and bone toxicity.
Precautionary Measures-
●Dust Control: Ensure that dust generated during manufacturing is controlled with proper ventilation systems and dust extraction equipment.
●Protective Gear: Operators should wear appropriate personal protective equipment (PPE), including respirators, gloves, and eye protection.
●Workplace Safety: Ensure that safety protocols are in place during AlN PCB fabrication and handling.
Safety Measure | Description | Example Equipment |
Dust Control Systems | Ventilation and extraction systems to minimize dust exposure | HEPA filtration, vacuum systems |
Personal Protective Equipment (PPE) | Respirators, gloves, and eye protection for workers handling AlN | N95 masks, gloves, goggles |
Training and Protocols | Safety training on handling AlN and risk awareness | Safety data sheets (SDS), OSHA training |
By adhering to proper safety protocols, the health risks tied to Aluminum Nitride PCBs can be significantly reduced. Handling and taking the right precautions ensures that workers remain safe while fully leveraging the excellent heat dissipation properties of AlN. Proper protective measures should be in place to avoid exposure to hazardous particles or fumes during manufacturing and assembly. With the right safety mindset, the benefits of AlN’s superior thermal performance can be enjoyed without compromising health or safety.
Fragility and Manufacturing Challenges
Aluminum Nitride PCBs are more fragile compared to other ceramic materials, such as alumina or silicon carbide. This fragility makes AlN prone to cracking or chipping during manufacturing processes or during assembly and soldering. Since AlN has a high melting point and is typically more brittle, handling it requires extra care.
The fragility of Aluminum Nitride creates certain manufacturing challenges, such as:
1.Handling and Cutting-
Special care must be taken when cutting and handling AlN substrates to avoid cracks or damage. Using precision laser cutting techniques and controlled environments can help reduce the risk of damage.
2.Bonding and Soldering-
AlN PCBs require specialized soldering techniques, such as active metal brazing (AMB) or high-temperature soldering, to ensure reliable bonding. These methods can be more complex and time-consuming than those used with other materials like FR4.
3.Thermal Expansion Issues-
Aluminum Nitride has a coefficient of thermal expansion (CTE) that is quite different from metals like copper, which are often used for PCB traces. This difference can lead to thermal stress during thermal cycling (heating and cooling), potentially causing delamination or cracking at the solder joints.
Manufacturing Process of Aluminum Nitride PCB
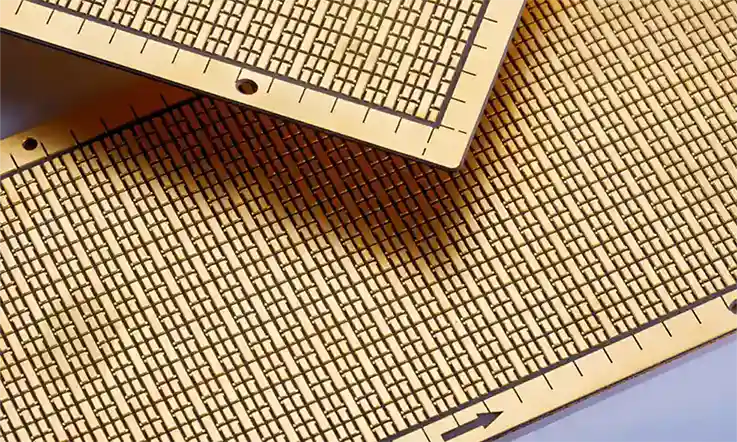
The manufacturing of Aluminum Nitride PCBs is a highly specialized process that involves a series of core steps, from substrate creation to final soldering. The performance of AlN PCBs—which is largely dictated by the material’s thermal conductivity and electrical insulation properties—depends greatly on the precision and control maintained during manufacturing. In this section, we’ll take a closer look at how AlN PCBs are made, the challenges faced in the process, and the innovative techniques that ensure a high-quality end product.
Key Steps in Fabricating Aluminum Nitride PCBs
The production of Aluminum Nitride PCBs requires a detailed and precise approach, starting with the creation of the ceramic substrate and moving through to the laser cutting, bonding, and soldering processes. Below are the key steps involved:
1.Sintering the Aluminum Nitride Substrate-
The first step in the production process involves heating aluminum nitride powder to high temperatures (typically between 1700°C and 1800°C) in a sintering furnace. This heat treatment forms a solid ceramic structure that demonstrates exceptional thermal conductivity and excellent dielectric properties. During this phase, the material is carefully monitored to maintain consistent density and ensure a smooth surface, which directly impacts the performance of the final PCB.
2.Substrate Shaping and Preparation-
After the sintering process, the AlN ceramic is shaped to the required specifications, typically through laser cutting or CNC machining. The material is carefully cut into precise shapes, such as round or rectangular formats, in preparation for the subsequent stages of the PCB manufacturing process. This step requires precision to ensure that the board performs as expected in both thermal conductivity and mechanical stability.
3.Thin Film Deposition-
After shaping, a thin film of metal—usually gold or copper—is deposited onto the Aluminum Nitride substrate to create conductive paths for the PCB. This step is often done using sputtering or electroplating techniques, ensuring that the metal layers bond strongly with the ceramic.
4.Laser Cutting and Drilling-
Once the metal film is in place, laser cutting is used to carve out the conductive tracks on the AlN PCB. This highly precise process is ideal for Aluminum Nitride, as it avoids the mechanical stress that could cause damage to the fragile ceramic material. Laser drilling is then used to create holes for component placement and electrical connections.
Manufacturing Process-
Step | Description | Key Considerations |
Sintering | Sintering of AlN powder at high temperatures | Temperature control, uniform density |
Shaping & Preparation | Laser cutting or CNC machining to shape the substrate | Precision in dimensions, surface smoothness |
Thin Film Deposition | Sputtering or electroplating of metal layers | Ensuring strong adhesion and conductive paths |
Laser Cutting & Drilling | Precision laser cutting and drilling for track creation and component placement | High accuracy to avoid stress cracks in the ceramic |
Challenges in Aluminum Nitride PCB Manufacturing
Manufacturing Aluminum Nitride PCBs isn’t without its challenges. While the material’s thermal conductivity and electrical insulation properties are highly desirable, there are several production hurdles that we must overcome to produce high-quality AlN PCBs. Below are the key challenges faced:
1.Handling Ceramic Substrates-
Aluminum Nitride is a ceramic material, which, while strong in many ways, is also brittle. This makes it difficult to handle during the manufacturing process. Breakage or cracking can occur during cutting, drilling, or even transportation of the substrates. Special care must be taken during each stage to prevent material failure.
2.Thermal Expansion Mismatch-
One of the most significant challenges in the AlN PCB manufacturing process is dealing with the coefficient of thermal expansion (CTE) mismatch between the ceramic substrate and the metals used for conductive traces. Aluminum Nitride has a CTE that is more closely aligned with semiconductors, but the difference in expansion rates between the ceramic and metals during heating and cooling cycles can cause stress fractures or delamination if not properly managed.
3.Precise Bonding Techniques-
The bonding of Aluminum Nitride to metals or solder is another challenge. Since AlN is a ceramic material, it doesn’t naturally adhere to metallic surfaces without special treatments. Using active metal brazing (AMB) or sintering to bond AlN PCBs requires extremely careful control to ensure that the bond is both strong and thermally conductive. If the bond is weak, it could compromise the PCB’s performance, especially in high-power applications.
Challenges-
Challenge | Description | Solutions |
Handling Ceramic Substrates | Brittle nature of AlN makes handling difficult | Use of specialized equipment and handling procedures |
Thermal Expansion Mismatch | Mismatch between ceramic and metal CTE during thermal cycling | Careful material selection, specialized bonding techniques |
Bonding Techniques | Difficulty in bonding AlN with metals | Active metal brazing (AMB) or sintering to ensure strong bonds |
Advanced Techniques for Bonding and Soldering Aluminum Nitride PCBs
To ensure Aluminum Nitride PCBs perform at their best in high-power applications, we must employ specialized bonding and soldering techniques. Below are some of the advanced techniques commonly used in the industry:
1.Active Metal Brazing (AMB)-
Active metal brazing (AMB) is a process where a metal layer is bonded to the AlN substrate using a specially formulated metal alloy that reacts chemically to form a strong bond between the ceramic and metal. AMB is particularly useful for creating high-performance thermal and electrical connections.
2.Sintering-
Sintering is another advanced technique where the metal is heated to a point just below its melting temperature, causing the metal particles to fuse together with the ceramic substrate. This technique is commonly used for bonding Aluminum Nitride to copper or gold films to create strong electrical connections and maintain thermal conductivity.
3.Soldering and Flux Application-
Soldering Aluminum Nitride PCBs requires specialized techniques to ensure proper bonding without damaging the ceramic. A special flux is used to prevent oxidation and improve the adhesion between AlN and solder. This technique is particularly useful in automotive electronics, where AlN PCBs are used for power inverters and other heat-sensitive applications.
Bonding and Soldering-
Technique | Description | Benefits |
Active Metal Brazing (AMB) | Metal bonding using a reactive alloy to ensure strong thermal and electrical connections | Ideal for high-performance applications |
Sintering | Bonding metal to AlN substrate by heating below metal’s melting point | Strong bond, excellent thermal conductivity |
Soldering and Flux | Soldering AlN PCBs using special flux to prevent oxidation | Enhanced adhesion, suitable for power electronics |
Design Considerations for Aluminum Nitride PCB
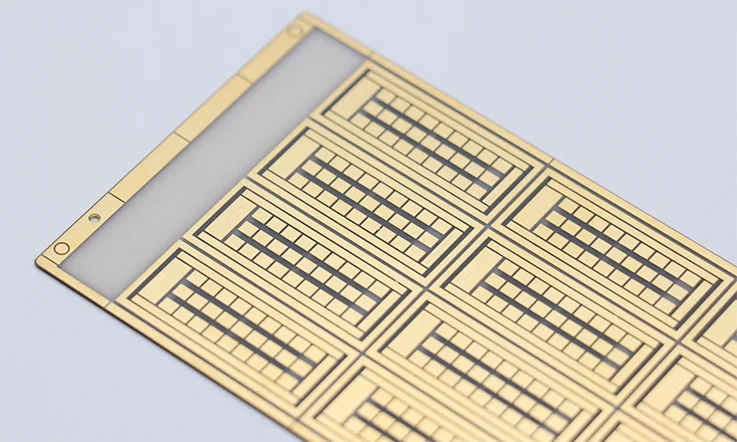
Designing Aluminum Nitride PCBs involves considering several factors that directly influence the performance and reliability of the final product. AlN is commonly used in high-power, high-temperature environments, where effective thermal management is necessary. From reducing thermal expansion to maintaining electrical signal consistency, these design elements directly affect the PCB’s effectiveness in demanding conditions. . Below, we’ll dive into the essential aspects of designing AlN PCBs for power electronics and other demanding applications.
Optimizing Aluminum Nitride PCB for High-Power and High-Temperature Applications
In high-power and high-temperature applications, Aluminum Nitride PCBs offer unparalleled performance in managing heat dissipation. However, the design of these PCBs must be carefully optimized to handle the specific thermal demands of the application. Here’s how you can design an AlN PCB to operate at its best:
1.Managing Heat Dissipation-
The ability of Aluminum Nitride to conduct heat efficiently is one of the material’s standout features. For high-power electronics, such as automotive inverters or LED drivers, thermal management is a design focus. Using AlN PCBs with high thermal conductivity (up to 170 W/mK) allows heat to move away from sensitive components, reducing the risk of overheating and improving the overall longevity of the device.
2.Proper Layer Stack-up-
A properly designed PCB stack-up is fundamental for achieving top-tier thermal management in high-temperature settings. In applications where heat is a major concern, layering AlN ceramic strategically can help distribute heat more evenly across the board. Pairing AlN with conductive materials like copper in the right spots allows heat to be transferred efficiently, while still providing solid electrical insulation where needed. This combination of materials ensures that the PCB can perform under high thermal loads while maintaining its structural integrity.
3.Use of Thermal Via Technology-
Integrating thermal vias into the AlN PCB design can enhance heat dissipation by providing a direct path from the heat-sensitive components to the backside of the PCB. Thermal vias allow heat to travel efficiently through the Aluminum Nitride material, preventing excessive heating on the top layer.
Optimizing Design-
Design Consideration | Description | Solution |
Heat Dissipation | Managing thermal conductivity to prevent overheating | Use AlN with high thermal conductivity (up to 170 -200W/mK) |
Layer Stack-up | Properly structuring PCB layers for thermal performance | Combine AlN with metals like copper for efficient heat transfer |
Thermal Via Technology | Direct heat transfer from components to the backside | Integrate thermal vias for enhanced heat flow |
Thermal Expansion and Mechanical Stress in Aluminum Nitride PCB Design
One of the most challenging aspects of designing Aluminum Nitride PCBs is managing the thermal expansion and mechanical stress that occurs in high-frequency circuits or semiconductor applications. Given the coefficient of thermal expansion (CTE) of Aluminum Nitride, which is about 4.0-4.5 x 10-6 /°C, it’s need to design PCBs that can withstand extreme temperature fluctuations without incurring damage. Here’s how to manage this some factor:
1.Thermal Expansion Compatibility-
When designing AlN PCBs, it is essential to select materials for the electrical traces and components that can tolerate the same thermal expansion rate as the AlN ceramic. Mismatches in CTE between the substrate and metals can lead to cracks, delamination, or mechanical failure over time. Therefore, materials such as copper and gold are often chosen for their low CTE and their ability to expand similarly to Aluminum Nitride.
2.Reducing Mechanical Stress-
Mechanical stress can arise when components are mounted on the AlN PCB, especially in high-power applications where heat cycling is frequent. A well-designed component placement strategy can help reduce thermal stress by positioning heat-sensitive parts away from hot spots on the PCB. Additionally, stress-relieving techniques like flexible bonding are employed to distribute mechanical forces more evenly.
3.Use of Stress Simulation Software-
In modern PCB design, using simulation software to predict thermal expansion and stress in Aluminum Nitride PCBs is a must. Simulation tools such as ANSYS or COMSOL Multiphysics allow designers to model how a PCB behaves under thermal cycling, giving them the chance to adjust the design and material choices ahead of actual production. This approach helps spot potential issues early, making sure that the final product can handle the high-stress conditions without any surprises once it hits the real world.
Thermal Stress and Mechanical Considerations-
Design Factor | Description | Solutions |
Thermal Expansion Compatibility | Matching the CTE of AlN and metals to prevent failure | Choose low CTE materials like copper and gold for the metal traces |
Mechanical Stress Reduction | Managing the mechanical forces during operation | Proper component placement and flexible bonding techniques |
Stress Simulation | Predicting thermal stress and mechanical issues | Use ANSYS or COMSOL for thermal and stress simulation |
Electrical Performance and Signal Integrity in Aluminum Nitride PCB Design
In high-power electronics, ensuring signal integrity and electrical insulation is as critical as managing thermal performance. Aluminum Nitride PCBs are excellent for both electrical insulation and thermal conductivity, but the design must account for factors like impedance control, signal routing, and electrical isolation. Here’s how to design AlN PCBs that deliver exceptional electrical performance:
1.Minimizing Signal Loss-
Aluminum Nitride has low dielectric loss and can be engineered to ensure minimal signal loss across high-frequency circuits. We must optimize the trace width and spacing between the signal traces to ensure that signal integrity is maintained, especially in high-frequency designs used in RF applications.
2.Impedance Control-
For high-speed digital circuits or RF designs, AlN PCBs need precise impedance control. This can be achieved through careful design of the trace geometry, substrate thickness, and copper foil characteristics. We can use tools like S-parameters and TDR (time-domain reflectometry) to ensure that the PCB maintains the required impedance levels, minimizing signal reflection and electrical noise.
3.Electrical Isolation-
Aluminum Nitride (AlN) is known for its strong dielectric strength, making it suitable for applications requiring electrical isolation. In power electronics, where high-voltage and low-voltage sections must be kept separate, AlN provides the necessary insulation without compromising thermal performance. This balance allows it to work effectively in environments where both electrical separation and heat management are required.
Electrical Performance-
Design Factor | Description | Solutions |
Signal Loss Minimization | Minimizing loss of signal in high-frequency circuits | Optimize trace width and spacing for better signal integrity |
Impedance Control | Ensuring proper impedance in RF or digital circuits | Use S-parameters and TDR tools to design the optimal trace geometry |
Electrical Isolation | Maintaining high dielectric strength for electrical isolation | Use AlN for insulation in high-voltage applications |
How to Verify the Quality of Aluminum Nitride PCBs?
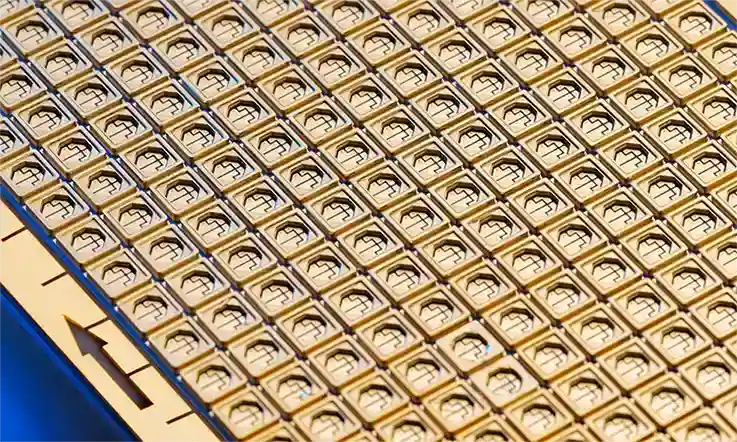
Ensuring the quality of Aluminum Nitride PCBs demands a step-by-step approach. These high-performance components are commonly found in environments that require effective heat dissipation and reliable electrical insulation. To verify their functionality and performance, it’s essential to go through a comprehensive quality assurance process. Below is a rundown of how to confirm that AlN PCBs meet the required standards and perform as expected in their demanding applications.
1. Visual Inspection: The First Line of Defense
Begin by inspecting the PCB visually for defects that could impair its function. Look for surface flaws like cracks, chips, or delamination. The visual check should also assess the uniformity in texture and color—this can help you spot issues like contamination or processing errors that could impact the thermal or electrical properties of the PCB.
Things to check:
●Surface defects: Small cracks or chips can compromise the mechanical integrity of the PCB.
●Uniformity: Any discoloration or uneven textures may signal overheating or poor manufacturing.
●Bonding issues: Ensure that copper traces are properly bonded to the AlN substrate, free from any separation or gaps.
2. Dimensional Accuracy: Fit and Precision Matter
For an Aluminum Nitride PCB to perform as expected, it needs to meet the precise dimensions set during the design phase. Accurate measurements ensure that the PCB fits properly within its assembly and helps avoid problems like short circuits or uneven heat distribution. Correct dimensioning is necessary to ensure that the PCB can meet the thermal and electrical requirements of its intended use.
What to do:
●Measuring tools: Use precision tools such as calipers or micrometers to measure the length, width, and thickness of the PCB.
●Comparison with specifications: Ensure that the measurements align with the design specifications. Even slight discrepancies can affect overall performance, especially in high-density or high-power applications.
3. Electrical Testing: Verifying Continuity and Resistance
Electrical testing ensures that the PCB’s electrical paths are intact and performing as expected. This includes checking for continuity between traces, insulation resistance, and impedance consistency.
Tests to run:
●Continuity Test: Use a multimeter to check for proper connections and ensure there are no open circuits or faulty solder joints.
●Insulation Resistance: With a megohmmeter, test the insulation resistance between different traces. This ensures there’s no electrical leakage.
●Impedance Matching: Particularly in high-frequency applications, ensuring the PCB maintains consistent impedance is needed to signal integrity.
4. Thermal Testing: Ensuring Efficient Heat Dissipation
Aluminum Nitride is well-regarded for its ability to conduct heat. Thermal testing confirms the PCB’s ability to distribute heat across its surface and prevent hotspots.
Thermal checks include:
●Thermal Cycling: The PCB undergoes repeated temperature cycles to ensure it can handle the stresses of expansion and contraction without cracking.
●Thermal Imaging: Infrared cameras or thermocouples can measure temperature distribution during operation, highlighting any areas of concern where heat isn’t properly dissipated.
●Heat Dissipation Performance: Test how well the PCB maintains thermal stability under load. This is must in high-power environments, such as power amplifiers or computing systems.
5. Dielectric Strength Testing: Verifying Electrical Insulation
A well-designed Aluminum Nitride PCB should be able to withstand high voltages without failure. Dielectric strength testing checks that the insulation between electrical traces can handle the stress of high-voltage environments.
Steps to follow:
●Dielectric Strength Tester: This tool applies voltage to the PCB, testing for the point where electrical insulation fails.
●Testing Range: For high-power applications, expect to see a breakdown voltage between 8–10 kV, depending on the design.
6. Reliability Testing: Ensuring Long-Term Performance
Reliability testing simulates the conditions the PCB will face over time in real-world applications. This can include thermal cycling, humidity exposure, vibration, and other factors that could affect long-term performance.
Tests involved:
●Thermal Cycling: The PCB is subjected to constant temperature changes to simulate normal operating conditions.
●Vibration and Shock: Simulate physical stresses that could occur during transportation or use in rugged environments.
●Humidity Exposure: The PCB is tested in high humidity to ensure it maintains performance even in challenging environments.
7. Quality Management Systems and Standards: Ensuring Consistency
Finally, when verifying the quality of an Aluminum Nitride PCB, it’s need to confirm that the manufacturer follows standardized processes. Adhering to established quality management systems, such as ISO 9001, helps maintain a consistent and dependable production process. This approach ensures that every PCB meets the necessary specifications without any unexpected variations.
What to verify:
●ISO 9001 Certification: This is a recognized standard for maintaining quality across production processes.
●Material Traceability: Confirm that the materials used in the PCB manufacturing are traceable and meet the required specifications for performance.
Aluminum Nitride PCB Vs. Aluminum Oxide (Al2O3) PCB
When comparing Aluminum Nitride (AlN) and Aluminum Oxide (Al2O3) PCBs, a few standout differences come into play that can impact your choice depending on your application:
1.Thermal Conductivity: AlN really takes the lead here with a much higher thermal conductivity of around 170W/mK, compared to Al2O3, which falls between 30-40W/mK. If heat dissipation is something you can’t overlook, AlN PCBs have the upper hand.
2.Dielectric Properties: AlN offers slightly better dielectric properties, with a constant between 8-9, while Al2O3 comes in at 9-10. This means AlN is a better fit for situations where you need top-notch signal integrity and insulation.
3.Operating Temperature: AlN PCBs handle higher temperatures, exceeding 350ºC, while Al2O3 tends to top out at lower temperatures. So, if your setup demands heat resistance, AlN will keep on trucking in those intense conditions.
4.Mechanical Strength: When it comes to toughness, AlN holds its own. It has superior mechanical strength and hardness compared to Al2O3, so it can handle more mechanical stress without cracking or deforming.
5.Cost: AlN does carry a higher price tag due to the costlier material and the more involved manufacturing process. If you’re watching the bottom line, Al2O3 might be a more budget-friendly pick.
6.Availability and Manufacturing: Al2O3 is more commonly available and widely used across various industries, making it easier to source and more familiar to most manufacturers. AlN, on the other hand, while growing in popularity, may require specialized equipment and processes.
What is the Cost of Aluminum Nitride PCBs?
When considering the cost of Aluminum Nitride PCBs, several variables play into the final price. These factors include the design complexity, dimensions, quantity, specific material requirements, and the manufacturer selected. AlN PCBs generally come at a higher price point than traditional PCB materials like FR-4, primarily due to their advanced properties and the specialized manufacturing processes required.
Key Cost Determinants of Aluminum Nitride PCBs:
1. Material Properties:
Aluminum Nitride substrates are prized for their superior thermal conductivity and electrical insulation capabilities. These properties make AlN PCBs suitable for high-power and high-temperature applications, such as power electronics, automotive systems, and high-performance computing. However, the materials themselves are more expensive than standard PCB materials like FR-4, which is commonly made from epoxy-based substrates.
2.Manufacturing Complexity:
The fabrication of AlN PCBs requires specialized equipment and a highly controlled manufacturing process. The material itself needs to be processed under precise conditions, including sintering, metallization, and bonding techniques, all of which require advanced technology. This specialized process can increase production costs.
3.Design and Application Requirements:
The complexity of the PCB design also affects the price. More intricate designs with higher layer counts, fine traces, or specific thermal management needs will require additional time and resources to manufacture. Additionally, the application (such as for power electronics or high-voltage systems) may require specific quality checks, which contribute to the overall cost.
4.Quantity and Order Volume:
Like most manufacturing processes, the quantity of PCBs ordered can influence the unit price. For large-scale orders, manufacturers may be able to reduce costs per unit, while small-volume orders may cost more due to the setup costs and smaller production runs.
5.Manufacturer and Location:
Different manufacturers have varying levels of expertise and production capabilities, which can influence pricing. For example, manufacturers in regions with higher labor costs or more stringent regulatory standards may have higher prices. Additionally, the manufacturer’s reputation and track record of delivering high-quality PCBs can factor into the price.
How to Get a Quote?
To get a precise price for Aluminum Nitride PCBs, it’s best to connect directly with manufacturers who specialize in AlN PCBs. For example, companies like JarnisTech can provide detailed quotes based on the design, material specifications, and production quantities that meet your project needs. We will also help navigate any unique requirements, such as specific testing for thermal or electrical performance.
Why Should You Import Aluminum Nitride PCBs From JarnisTech?
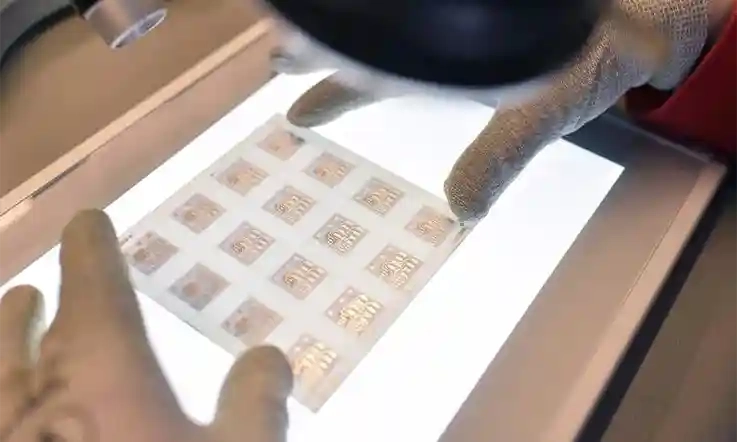
Finding a reliable manufacturer for Aluminum Nitride PCBs is essential to the success of your project. JarnisTech is a trusted choice for AlN PCB production, providing high-quality manufacturing, cutting-edge production methods, timely delivery, and customized solutions that align with your specific design needs. Here’s why JarnisTech should be your top pick for Aluminum Nitride PCBs.
1. Strong Manufacturing Capabilities
JarnisTech operates a state-of-the-art facility equipped with the latest technologies for Aluminum Nitride PCB production. The factory uses advanced equipment that specializes in the precision and quality needed for AlN PCBs, ensuring that each board meets the highest standards of performance and reliability. From automated production lines to specialized handling systems, our manufacturing process is designed to produce AlN PCBs that meet the most demanding applications. Whether you need standard boards or more complex designs, JarnisTech has the expertise to deliver.
2. Advanced Production Techniques
The production of Aluminum Nitride PCBs requires specialized techniques to ensure that the unique properties of AlN—such as its high thermal conductivity and excellent electrical insulation—are fully realized. At JarnisTech, we utilize advanced fabrication processes like sintering, copper bonding, and precision metallurgy to manufacture high-performance AlN PCBs. Our skilled technicians and engineers are experienced in optimizing these processes, ensuring that your PCBs will perform optimally in high-power applications. We also incorporate stringent quality control measures throughout every stage of production to prevent defects and guarantee the consistency of the end product.
3. Fast and Reliable Delivery Times
In today’s competitive electronics market, on-time delivery is non-negotiable. JarnisTech gets it—your project timeline is a big deal. That’s why we provide fast, dependable lead times for Aluminum Nitride PCBs. Whether you’re testing prototypes in small batches or ramping up for large-scale production, we’ve got you covered. Our streamlined production process, paired with smart logistics, ensures that your orders arrive exactly when you need them, without missing a beat. You can count on us to keep things moving and help you hit your milestones with no hang-ups.
4. Customized PCB Solutions
One of the standout features of working with JarnisTech is our ability to offer customized PCB solutions tailored to your exact specifications. Whether you require specific dimensional tolerances, unique layer configurations, or specialized thermal and electrical properties, we can work with you to design the perfect PCB for your needs. Our in-house design team collaborates closely with customers to ensure that all requirements are met, from thermal management to electrical performance. Additionally, we offer complete PCB assembly services, enabling you to receive fully assembled and tested boards ready for integration into your product.
5. Comprehensive Support and Expertise
JarnisTech isn’t just a supplier; we’re a full-service partner. Our team of experienced engineers and technical experts is available to provide ongoing support throughout your project. From initial design consultations to final assembly, we’re here to ensure that your Aluminum Nitride PCBs meet your performance, reliability, and budget goals. If you’re unsure about the best PCB design for your specific application, our team can offer guidance and suggestions based on years of industry experience.
JarnisTech – A Trusted Partner for Your AlN PCB Needs!
Importing Aluminum Nitride PCBs from JarnisTech means more than just purchasing high-quality boards; it’s about partnering with a manufacturer that values precision, timely delivery, and customer satisfaction. Get in touch with us today and let JarnisTech be the partner you trust for all your Aluminum Nitride PCB requirements.
Aluminum Nitride PCBs &FAQ
1. Can Aluminum Nitride PCBs handle high-voltage?
Yes, they can withstand high voltages, with dielectric strength typically around 8-10 kV.
2. Can Aluminum Nitride PCBs be flexible?
Typically, no. Aluminum Nitride PCBs are rigid but can be customized for certain flexible applications.
3.Can Aluminum Nitride PCBs be used in RF (Radio Frequency) circuits?
Yes, AlN’s low dielectric constant makes it suitable for RF and high-frequency applications.
4.Is it possible to integrate Aluminum Nitride PCBs with traditional PCB materials like copper?
Yes, AlN can be combined with copper or other metals for the conductive layer, providing both thermal management and electrical performance.