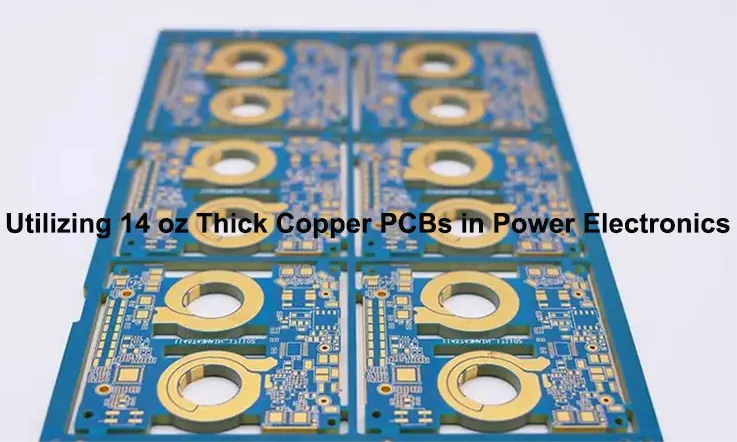
Power electronics establish a significant cornerstone in countless applications, covering renewable energy platforms, electric automotive technology, industrial equipment, and consumer electronics. The continual increase in power necessities propels engineers to persistently uncover novel solutions for boosting operational performance and energy efficiency. One such breakthrough is the application of 14 oz thick copper PCBs. These durable circuit boards provide an intensified capacity for carrying current and offer exceptional thermal control, hence making them ideally suited for usage in power electronic scenarios. This discussion will explore the advantages associated with 14 oz thick copper PCBs and their promise to transform power electronics design approach.
Overview of Thick Copper PCBs
Thick Copper PCBs, also referred to as Heavy Copper PCBs or Power PCBs, represent exclusive printed circuit boards engineered to support heightened power and current prerequisites. Unlike customary PCBs, which characteristically exhibit copper tracks between 1 ounce per square foot (oz/ft²) to 2 oz/ft², thick copper PCBs showcase distinctly thicker copper layers, generally ranging from 3 oz/ft² to 20 oz/ft² or even more.
Here is an exploration of the critical characteristics that define thick copper PCBs:
Amplified Current Capacitation:
The primary merit of thick copper PCBs emerges from their capability to sustain high currents. The substantial copper thickness reduces resistance, thereby lessening voltage drop and power loss, making these PCBs apt for applications demanding high-power transmission.
Effective Heat Transfer:
Thick copper layers enhance thermal conductivity, allowing proficient heat dispersion. This characteristic is particularly valuable in power electronics and applications where heat production can be a challenge.
Augmented Structural Durability:
The amplified copper density renders thick copper PCBs with enhanced mechanical robustness, making them more resistant to thermal strain, vibration, and mechanical shocks.
Boosted Dependability:
Thick copper PCBs boost reliability by diminishing the likelihood of trace burns or malfunctions due to high current or thermal strain. The increased copper thickness is instrumental in minimizing the risk of conductor fracture.
Multi-layer Structure:
Thick copper PCBs can be designed with multiple layers, facilitating the establishment of sophisticated circuitry and efficient space optimization. The inner layers can also be beefed up with thicker copper for effective power distribution within the PCB.
Expense Aspects:
It is pertinent to acknowledge that thick copper PCBs usually incur higher expenses than regular PCBs due to added material costs and specialized fabrication processes. The heightened copper mass and additional processing stages add to the complete manufacturing cost.
Applications of Thick Copper PCBs
Thick copper PCBs feature prominently across a variety of sectors and high-power electronic devices, encompassing:
Power Electronics: Thick copper PCBs are often essential in inverter modules, motor-operated drives, power conversion units, and power supply systems, where they manage hefty currents and efficiently dissipate heat.
Automotive Sphere: Electrically-powered vehicles (EVs), hybrid vehicles, and other automobile applications leverage thick copper PCBs to sustain high-power systems and endure intense operational circumstances.
Industrial Machinery: High-powered equipment, industrial regulation systems, automation mechanisms, and heavy machinery all utilize thick copper PCBs for their structural fortitude and the capacity to handle high currents.
Renewable Energy Systems: Solar inverters, wind-powered systems, and additional renewable energy mechanisms employ thick copper PCBs to manage significant currents and enable efficient thermal dispersion.
Aerospace and Defense: Due to their reliability and capability to cope with high power quotas, thick copper PCBs are vital for radar assemblies, satellite communication modules, power allocation units, and other aerospace and defense-related electronics.
Thick copper PCBs offer a reliable and effective resolution for demanding applications distinguished by substantial power and current necessities. Their unique characteristics position them aptly across a vast range of industries where reliable power transmission and effectual heat dissipation are of utmost importance.
Why Understanding 14 oz Thick Copper PCBs?
The 14 oz thick copper PCB is characterized by its impressive copper weight of 14 ounces (490μm), making it a highly robust board designed to accommodate high-current applications. The increased copper content facilitates superior current conductivity and ensures efficient thermal distribution across the board. Moreover, this type of PCB offers the advantage of accommodating complex switches within a limited space, enabling the implementation of intricate circuitry.
In general, a PCB is considered a thick copper PCB when it features a copper thickness exceeding 2 oz. With its 14 oz copper weight, the 14 oz thick copper PCB can be classified as an extremely thick board, ensuring optimal performance and durability.
The copper thickness in a PCB signifies the finished copper weight, which subsequently influences the thickness of the pads and tracks embedded within the board. For comparison, a 1 oz copper PCB houses a thickness of 35μm. Consequently, the 14 oz copper PCB, with its substantive 490μm copper thickness, offers exceptional conductivity and robustness. It is essential to highlight that the precise copper thickness of a PCB can be customized according to the demands of the specific application.
The 14 oz thick copper PCB is particularly well-suited for applications that demand high current capabilities. Manufacturers often utilize heavy copper foil for PCBs intended to handle substantial currents. By employing a 14 oz thick copper PCB, these applications can effectively manage excessive current loads and ensure reliable performance.
Why is PCB Copper Thickness Measured in Ounces?
Quantifying the copper thickness in ounces (Oz) on PCBs is an established convention due to its relation with the weight of the copper layer, which ultimately dictates the density of the copper coating on the board.
1 Oz copper Printed Circuit Board (PCB), the allotted copper density is architected such that a measure of one ounce of copper is evenly distributed over a surface area of one square foot. This assigned density translates to a relative thickness of approximately 1.37 mils, or a weight of 28.3495 grams. As in the instance of a 14 Oz copper PCB, to define the thickness of the copper stratum, one should perform multiplication of the base thickness of 1.37 mils by 14. The resultant calculation provides a deduced thickness of 19.18 mils, which is of paramount importance in ensuring the PCB’s operational efficacy with respect to electrical conductivity and thermal regulation.
The functionality of a PCB is amplified with a higher copper weight, as the increased copper content enriches its electrical properties. However, it’s significant to recognize that excessively thick copper PCBs present obstacles in the etching procedure. The act of etching considerable copper thickness proves more arduous compared to thinner ones.
Fabricators must confirm that the minimum pattern width or clearance on the PCB complies with specific criteria to uphold peak operation. The manufacturing progression involved with thick copper PCBs is inherently more intricate and challenging, requiring added time and work. This factor, therefore, contributes to their higher price-point compared to standard PCBs.
Design Considerations for 14 oz Thick Copper PCBs
When embarking on the design of a 14 oz thick copper PCB, it is imperative to address several crucial considerations to optimize both performance and manufacturability. Here are key design considerations to heed:
Copper Trace Width and Spacing:
Given the heightened copper weight, thicker traces are indispensable to accommodate increased currents. Ensure that trace widths are appropriately sized to carry desired currents without incurring excessive voltage drop or heat buildup. Additionally, maintain suitable spacing between traces to mitigate unintended electrical coupling or short circuits.
Thermal Management:
Thick copper PCBs are integral to high-power applications where effective heat dissipation is paramount. Integrate thermal management techniques such as expansive copper pours, thermal vias, or heat sinks to efficiently dissipate heat generated by high-current components. Thoughtful thermal design mitigates excessive temperature rise, safeguarding PCB reliability.
Component Placement:
Strategically position high-power components with consideration for their proximity to copper traces. Opt for placements that minimize trace length, reducing resistance and consequent voltage drop and power losses. Thoughtful component placement also aids in effective thermal management.
PCB Stackup:
The PCB stackup is instrumental in ensuring optimal signal integrity and power distribution. With thick copper PCBs, additional power and ground planes may be necessary to provide ample copper area for power distribution and maintain low impedance paths. Design the stackup meticulously to achieve desired electrical and thermal performance.
Manufacturing Constraints:
Manufacturing thick copper PCBs presents unique challenges compared to standard PCBs. The etching process for thick copper layers can be more intricate and time-intensive. Factor in the manufacturing capabilities of the PCB fabrication house and tailor the board design to adhere to feasible trace widths, spacing, and other manufacturing guidelines to ensure successful production.
Testing and Validation:
Given the specialized nature of thick copper PCBs, rigorous testing and validation are imperative. Conduct thorough electrical and thermal simulations to verify PCB performance, ensuring alignment with desired specifications and capability to meet intended high-current requirements.
Cost Considerations:
It’s essential to acknowledge that thick copper PCBs often entail higher manufacturing costs relative to standard PCBs, attributed to increased copper content and specialized manufacturing processes. Deliberate the project’s budgetary constraints and strike a balance between the advantages of thick copper and associated costs.
Comparing 14 oz Thick Copper PCBs and 16 oz PCBs
When comparing 14 oz thick copper PCBs and 16 oz PCBs,, key differences come to the fore, primarily associated with the copper weight or thickness of the PCBs:
Copper Weight Considerations: Within the sphere of Printed Circuit Boards (PCBs) designed with advanced copper density, a PCB boasting a 14 oz layer of copper carries a proportional weight of 14 ounces (roughly converted to a thickness of 490μm), while a 16 oz copper PCB presents a representative weight of 16 ounces (approximately quantifying to a thickness of 560μm). The quantitative flourish in copper weight across both configurations endows an escalated prowess for current conduction and superior thermal regulation, exceeding the functionalities of traditional PCBs with lower copper concentrations.
Amplified Electrical Capacity: PCB constructs with the specification of 14 oz and 16 oz copper thicknesses are astutely engineered to endure substantially high electrical currents as opposed to their standard analogues. The surplus copper weight inherent in the 16 oz construct further bolsters its capability to cater to heightened current requisitions, thus making it an ideal fit for applications necessitating stringent electrical demands.
Efficiency in Thermal Management: The augmented copper constituents in the 14 oz and 16 oz PCB variants considerably uplift their heat dissipation efficacy. Nonetheless, the 16 oz PCB, outfitted with its more hefty layer of copper, could command a marginally elevated thermal performance. This defined trait assures enhanced thermal conductivity and heat diffusion, critical to sustain optimal operational temperatures, thereby safeguarding the durability of the PCB along with its components.
Fabrication Complexity: Thick copper PCBs, including both 14 oz and 16 oz variants, are more complex to manufacture compared to standard PCBs. The etching operation for thicker copper layers proves more complex and time-consuming, urging the need for specialized production techniques. As the copper mass escalates, so does the fabrication complexity, potentially deeming 16 oz PCBs more arduous and expensive to produce relative to 14 oz PCBs.
Design Considerations: When strategizing PCBs with denser copper layers, crucial design elements such as trace widths, spacing, thermal control, and component arrangement become remarkably important. Both 14 oz and 16 oz PCBs mandate precise planning and compliance with these design considerations to ascertain optimal performance, dependability, and manufacturability.
Ultimately, the preference between a 14 oz thick copper PCB and a 16 oz PCB is contingent on the detailed requirements of the application. In conditions demanding extraordinarily high current-carrying capacity and intense thermal control, a 16 oz PCB might be the best fit. In contrast, for applications with modestly lower current necessities, a 14 oz thick copper PCB could deliver suitable performance while possibly being more cost-effective and easier to manufacture.
Quality Control in 14 oz PCB Manufacturing
Assuring quality control in the fabrication process of 14 oz PCBs is pivotal to certify the dependability and performance of the end product. Here are some essential procedures that can be adapted to uphold high-quality standards:
Vendor Selection:
Opt for a credible and seasoned PCB fabricator with a history of delivering high-quality thick copper PCBs. Undertake thorough research, scrutinize customer reviews, and evaluate their certifications and quality management methodology to ensure their capabilities align with your requirements.
Design for Manufacturability (DFM):
Work closely with the PCB fabricator during the design stage to ascertain the design is primed for manufacturability. Pay heed to their specific competencies and guidelines for managing thick copper layers. Resolve any manufacturing constraints early in the design process to circumvent potential issues during production.
Material Scrutiny:
Employ superior quality materials that satisfy the demanded standards for thick copper PCBs. This includes picking suitable copper foil thickness, prepregs, and cores specifically purposed for thick copper applications. Collaborate meticulously with the fabricator to determine the optimum materials for your specific requirements.
Procedural Oversight:
Adopt stringent procedure oversight measures throughout the fabrication process. Supervise critical parameters such as temperature, pressure, and etching intervals to ensure uniformity and accuracy. Regularly calibrate equipment, conduct quality checks, and perform procedural audits to identify and rectify any deviations or abnormalities.
Review and Validation:
Settler comprehensive review and validation protocols to authenticate the quality of the fabricated PCBs. This includes visual checks, dimensional assessments, electrical testing, and heat testing. Perform sample-based inspections and institute statistical procedural control techniques to monitor the quality of the production batches.
Documentation and Traceability:
Preserve exhaustive documentation of each fabrication step, including materials employed, procedural parameters, and inspection outcomes. Establish traceability arrangements to map the components and procedures engaged in the production of each PCB. This enables effective root cause analysis and facilitates swift recognition and resolution of any quality issues that might arise.
Continual Enhancement:
Inculcate a culture of continual enhancement by routinely reviewing and analyzing quality data. Use feedback from the fabrication process and customer feedback to spot areas for enhancement. Employ corrective and preventive actions to address any quality issues and augment the overall fabrication process.
By adopting these measures, you can ensure effective quality control throughout the fabrication of 14 oz PCBs, resulting in dependable and high-functioning products that meet the demanded standards and specifications.
Conclusion
The employment of 14 oz thick copper PCBs in power electronics ushers in a wealth of opportunities for engineers and designers. Their superior power-hefting capability, efficient thermal dispersal, and enhanced dependability position them as an enticing option for high-power applications. As technological inclinations progress and power requirements continue to incline, exploiting the potential of 14 oz thick copper PCBs becomes increasingly pivotal. By capitalizing on their advantages, engineers can sculpt power electronic systems that yield exceptional performance, refined efficiency, and fortified durability. Adopting this progressive technology lays the groundwork for a new epoch of power electronics revolution.