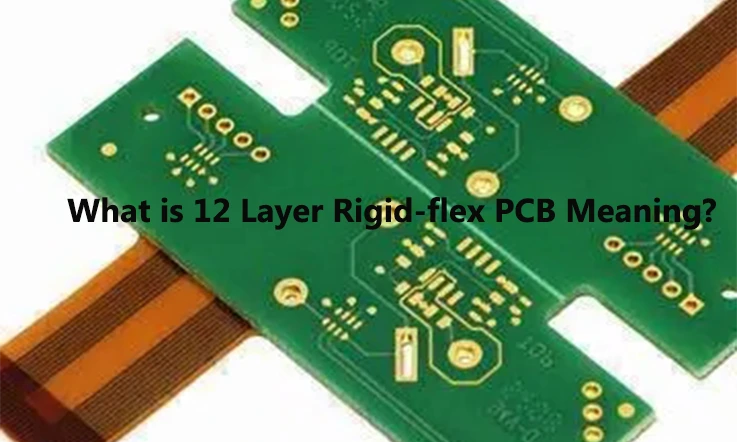
The goal of this discussion is to delve into the complexities and merits of 12-layer rigid-flex Printed Circuit Board designs. As technological advancement accelerates, the requirement for compact, multifunctional electronic products has surged. To meet this growing need, engineers and design experts turned to the 12-layer rigid-flex PCB, an excellent compromise that encapsulates both rigid and flexible PCB benefits. These specific PCBs provide unmatched design options, heightened reliability, and superior functionality across diverse sectors.
In this article, we will delve into the technical aspects, benefits, and applications of 12 layer rigid flex PCB circuit boards.
What is 12 Layer Rigid-flex PCB Meaning?
A 12 layer rigid flex PCB refers to a printed circuit board that combines both rigid and flexible substrates into a single construction with 12 distinct layers. Rigid flex PCB are designed to provide a combination of mechanical flexibility and electrical functionality, making them suitable for applications where traditional rigid PCBs or flexible circuits alone may not be sufficient.
The “12-layer” aspect refers to the number of layers within the PCB stack-up. These layers typically consist of conductive traces, signal and power planes, ground planes, and insulating layers, stacked together to create the desired electrical connectivity and functionality.
Incorporating both rigid and flexible substrates within one Printed Circuit Board (PCB) provides the ability for the board to curve or flex according to limited or unconventional spaces, and it ensures an enhancement in mechanical reliability and optimizes the use of space when compared to traditional rigid PCB. The flex region of the PCB provides the necessary flexibility, while the rigid sections offer structural support and host components, connectors and other circuit elements.
In the realm of sophisticated electronic devices and systems, the utilization of 12-layer rigid-flex PCB is quite prevalent. These PCB are found in myriad applications, such as in aerospace and defense machinery, healthcare technology, industrial automation interfaces, robotics, and elite consumer electronics. These advanced sectors typically demand a blend of flexibility and tightly-packed electrical components–a requirement aptly met by these unique PCB assemblies.
What Material About 12 Layer Rigid-flex PCB Stack-up?
Deciding on the appropriate materials for 12 layer rigid flex PCB stack-up is influenced by a multitude of aspects. These often include the requirements of the application, the desired mechanical and electrical performance, and the available manufacturing competencies. Following are the materials traditionally adopted for each layer in 12 layer rigid flex PCB stack-up:
Outer layers (rigid sections):
Copper foil: Typically used for signal traces and power distribution.
FR-4 (Fire-Resistant 4): A widely used epoxy-based laminate material that provides good electrical insulation and mechanical strength.
Inner layers (rigid sections):
Copper foil: Used for additional signal routing, power planes, or ground planes.
Prepreg: Layers of fiberglass cloth impregnated with epoxy resin, used for bonding the copper layers together.
Flex layers:
Polyimide : A highly flexible and heat-resistant material that serves as the base substrate for the flexible regions. It offers excellent mechanical properties and can withstand repeated flexing without degradation.
Adhesive: Used to bond the polyimide layers together in the flex region.
Vias:
Copper-plated vias: Used to provide electrical connections between different layers, including rigid and flex regions.
It’s important to note that the specific material choices and layer configurations within a 12-layer rigid-flex PCB stack-up can vary based on design requirements, manufacturing capabilities, and the choice of the PCB manufacturer. Collaboration with the PCB manufacturer and adherence to their guidelines are crucial to ensure the successful implementation of the desired material stack-up for a 12-layer rigid-flex PCB.
Benefits and Applications on 12 Layer Rigid-flex PCB
The use of 12-layer rigid-flex PCB offers several benefits and finds applications in various industries. Here are some key benefits and common applications:
Benefits:
Space optimization: With the ability to integrate rigid and flexible sections into a single PCB, 12-layer rigid-flex PCB enable efficient use of space, making them suitable for applications with limited board real estate or complex form factor requirements.
Design flexibility: Rigid flex PCBs allow for flexibility in design, facilitating the creation of custom shapes, conformal layouts, and unique form factors. This enables innovative designs and the accommodation of mechanical movements or irregular spaces.
Reliability and durability: The elimination of connectors and reduction in interconnects improve the overall reliability and durability of 12 layer rigid flex PCB. They possess superior resistance to mechanical stressors, tremors, and shocks, thus rendering them optimally suited for operations that require sustained reliability.
Signal integrity and EMI mitigation: The multiple layers in a 12-layer rigid-flex PCB provide better signal integrity and noise reduction. Controlled impedance and improved shielding properties help minimize signal degradation, crosstalk, and electromagnetic interference (EMI).
Simplified assembly and reduced assembly time: Rigid-flex PCB simplify the assembly process by eliminating the need for complex interconnects and connectors. This reduces assembly time, labor costs, and potential failure points, leading to overall improved efficiency.
Applications:
Aerospace and Defense: The implementation of 12-layer rigid-flex PCBs across numerous aerospace and defense-related applications are noted, including but not limited to, radar systems, avionics, satellites, UAVs (unmanned aerial vehicles), and military-grade communication systems. Their compact dimensions synchronized with their credibility and flexible in harsh conditions render them quintessential for these rigorous applications.
Medical devices: Rigid-flex PCB find application in medical devices such as pacemakers, implantable devices, diagnostic equipment, and wearable health monitors. The flexibility of the PCBs allows them to conform to the body or fit within compact medical devices while maintaining reliability and signal integrity.
Automotive electronics: In automotive applications, 12-layer rigid-flex PCB can be utilized in advanced driver assistance systems (ADAS), infotainment systems, control units, and instrumentation panels. Their compact design, resistance to vibration, and improved thermal management make them well-suited for automotive environments.
Consumer electronics: Rigid flex PCB are employed in various consumer electronic devices, including smartphones, tablets, wearable and portable devices. Their compact size, enhanced durability, and improved signal integrity contribute to the performance and reliability of these devices.
Industrial automation and robotics: Rigid flex PCB find application in industrial automation equipment, robotics, and control systems. Their flexibility and compactness enable reliable operation in tight spaces and demanding industrial environments.
IoT and smart devices: With the growth of the Internet of Things, 12 layer rigid flex PCB are used in IoT devices, smart home systems, and connected devices. The flexibility and space-saving attributes of rigid-flex PCB make them essential for integrating sensors, communication modules, and miniaturized components.
Design Guidelines for 12 Layer Rigid-flex PCB
Design guidelines for 12-layer rigid-flex PCB typically include the following considerations:
Layer stack-up: Plan the layer stack-up carefully, considering the distribution of signal, power, and ground layers. Ensure appropriate isolation between signal layers and adjacent planes.
Trace routing: Follow best practices for trace routing to minimize crosstalk and impedance mismatch. Maintain proper trace widths, spacing, and differential pair routing guidelines. Consider signal integrity and impedance control throughout the design.
Component placement: Optimize the placement of components to minimize signal path lengths and ensure proper mechanical support. Consider thermal management, accessibility for assembly and testing, and any specific requirements for flex regions.
Power and ground planes: Distribute power and ground planes effectively, ensuring low impedance paths for power delivery and proper grounding. Use multiple vias for plane connections to reduce impedance.
Flex region design: Pay attention to the design of flex regions or areas where the PCB flexes or bends. Avoid placing components or vias in these areas as they can experience stress and may compromise reliability. Use gradual flex transitions and round corners to minimize stress concentrations.
Material selection: Choose appropriate flexible substrate materials that can withstand the intended mechanical stress and provide sufficient electrical performance. Consider factors such as flex life, temperature range, dielectric properties, and compatibility with the manufacturing and assembly processes.
Plated through-holes (PTHs): Minimize the number of PTHs passing through the flex regions, as they can introduce stress concentration points. Use filled and capped vias for improved reliability in flex areas.
Design for manufacturing and assembly (DFM/DFA): Consider manufacturability and assembly requirements during the design phase. Ensure adequate spacing for fabrication processes, conformal coating, and component placement. Collaborate with your PCB manufacturer to ensure the design meets their capabilities and guidelines.
Documentation and design validation: Provide detailed design documentation, including assembly drawings, fabrication notes, and any specific requirements. Validate the design using simulations, prototypes, or design rule checks to ensure compliance with electrical and mechanical specifications.
What are the Difficulties in Producing 12 Layer Rigid-flex PCB Circuit Boards?
Producing 12-layer rigid-flex PCB circuit boards can present several challenges due to the complexity and specific requirements of the design. Some of the difficulties encountered include:
Manufacturing complexity:
The production process for 12 layer rigid flex PCB is more complex compared to standard rigid or flexible PCB. It involves multiple layers of rigid and flexible materials, precise alignment and interconnections between the layers, which require advanced manufacturing techniques and equipment.
Material selection and compatibility:
Selecting appropriate materials for both rigid and flexible sections can be challenges. looking for upon materials that present exemplary electrical characteristics, mechanical flexibility and harmoniousness with the fabrication method involves a fine equilibrium. The compatibility of various material attributes, for example, coefficients of thermal expansion (CTE), demands thoughtful contemplation to certify structural integrity and reliability.
Alignment and registration:
Attaining precise alignment and registration amidst rigid and flexible sectors during the fabrication phase is paramount. Misalignment could potentially instigate dependability dilemmas, like stress concentrations, short circuits, or layer delamination. Sustaining alignment throughout the production process, encompassing drilling, laminating, and plating, necessitates professional maneuvering and adept manufacturing techniques.
Controlled impedance and signal integrity:
Managing controlled impedance and ensuring signal integrity become more challenging with increased layer count. Maintaining consistent impedance across multiple layers, managing cross-talk, and minimizing signal degradation due to electromagnetic interference (EMI) become critical design considerations. Advanced simulation tools and signal integrity analysis are often employed to address these challenges.
Flex region reliability:
The flexible portion of the PCB, also known as the flex region, experiences repeated bending and flexing during the device’s lifetime. Ensuring the reliability of the flex region, such as avoiding stress concentration points, preventing cracks in traces, and adhesive delamination, requires careful design considerations and appropriate material selection.
Assembly and testing:
The intricacy of assembling components on a 12 layer rigid flex PCB escalates due to the amplified layer count and the hybridization of rigid and flexible zones. Specialized assembly techniques like controlled reflow profiles are perhaps required catering to the dissimilar thermal expansion traits of the materials. Stringent examination and testing approaches, including electrical evaluation and mechanical simulations, emerge as indispensable to ensure the structural integrity of the produced 12 layer rigid flex PCB.
How to Find a Reliable 12 Layer Rigid-flex PCB Manufacturer?
Finding a reliable 12 layer rigid-flex PCB manufacturer requires careful research and evaluation. Here are some steps you can follow to identify a reputable manufacturer:
Define your requirements: Clarify your specific requirements, including the project specifications, quantities, quality standards, budget, and any specific certifications or industry standards that need to be met. This will help you narrow down potential manufacturers that align with your needs.
Ask for recommendations: Seek recommendations from industry professionals, colleagues, or online forums. Their experiences and insights can provide valuable information about reliable manufacturers they have worked with or heard good things about.
Conduct online research: Search for PCB manufacturers specializing in rigid flex PCB. Visit their websites, review their capabilities, manufacturing processes, certifications and customer testimonials. Look for manufacturers with a proven track record in producing high-quality 12 layer rigid flex PCB.
Assess manufacturing capabilities: Evaluate the manufacturer’s manufacturing capabilities, such as their equipment, production capacity, and quality control processes. Consider factors like their experience with complex layer stack-ups, ability to handle advanced materials, and adherence to industry standards.
Request samples or prototypes: Request samples or prototypes of 12 layer rigid flex PCB from shortlisted manufacturers. Evaluate the quality, workmanship, and performance of the samples to assess the manufacturer’s capabilities. This step can help you verify if they can meet your specific requirements.
Engage in communication: Contact the manufacturers directly to discuss your project requirements and expectations. Evaluate their responsiveness, willingness to collaborate, and ability to provide technical support or design assistance. Clear and effective communication throughout the manufacturing process is essential for successful collaboration.
Quality control processes: Inquire about the manufacturer’s quality control processes. Ask about their testing methods, inspection procedures and certifications, such as ISO standards or compliance with industry-specific quality requirements. A reliable manufacturer should have robust quality assurance measures in place.
Cost and lead time considerations: Obtain detailed quotes from the manufacturers for your project. Compare the pricing structures, payment terms and lead times. Keep in mind that while cost is an important factor, compromising on quality for lower prices may lead to unsatisfactory results.
Customer references: Request references from the manufacturer’s previous clients. Contact these references to gather feedback on their experiences, reliability, delivery times, and overall customer satisfaction. Their insights can provide valuable information to help you make an informed decision.
Visit the facility: If feasible, consider visiting the manufacturer’s facility to assess their infrastructure, production processes, and overall working environment. This can provide valuable firsthand impressions and insights.
Summary
In summation, 12 layer rigid flex PCB circuit boards signify a paradigm shift in electronic design and manufacturing processionals. With their ability to combine rigid and flexible sections into a single board, they offer numerous advantages such as space optimization, design flexibility, improved reliability, and signal integrity.. Their application is hence impeccably suited to sectors like aerospace, medical devices, automotive electronics, consumer electronics, industrial automation, and IoT devices.
However, it is essential to work with experienced and reliable PCB manufacturers (JarnisTech), we specialize in 12 layer rigid flex PCB to ensure successful production and optimum performance. As technology continues to evolve and demands for compact and high-performance devices persist, 12 layer rigid-flex PCB circuit boards will play an increasingly critical role in driving innovation and meeting these challenges in various industries.